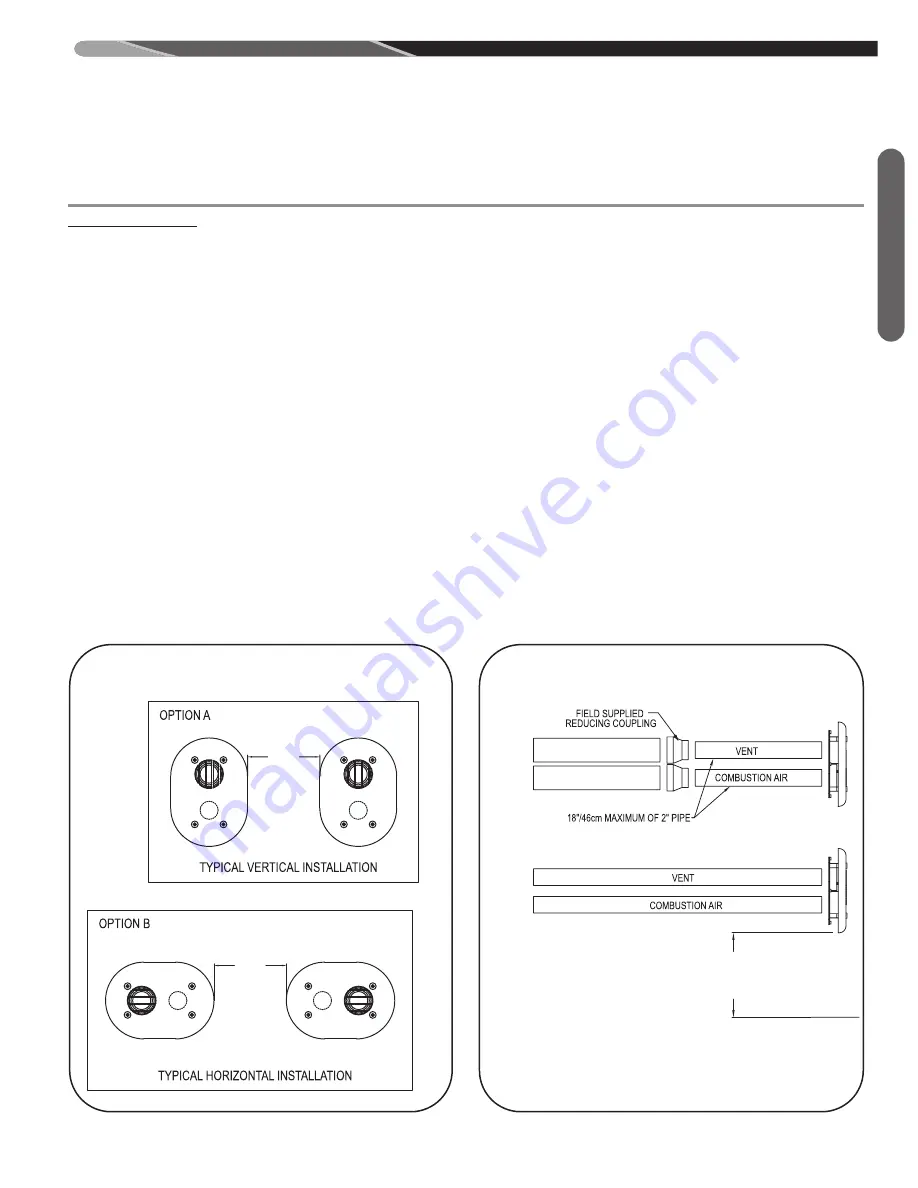
39
Ve
ntin
g
OPTIONS 8 & 9: 2
(
& 3
(
SIDE WALL VENT TERMINATIONS (Figures 24 & 25)
FOR 2
(
PIPE: RxGy-G02
FOR 3
(
PIPE: RxGy-G01
DIRECT VENT (cont.)
GENERAL VENTING REqUIREMENTS AND
GUIDELINES
MAINTAIN 12”/31cm FOR THE U.S. AS THE
MINIMUM CLEARANCE ABOVE THE HIGHEST
ANTICIPATED SNOW LEVEL OR GRADE WHICHEVER
IS GREATER. IN CANADA TERMINATIONS MUST CONFORM
TO CSA B149.1-10, SECT. 8.14.
3” PIPE
WITH
OPTIONAL
2” TERMINATION
2” PIPE
(RXGY-G02)
OR
3” PIPE
(RXGY-G01)
This termination is for horizontal venting only. This termi-
nation may be installed with either a non-direct-vent or a
direct-vent system. When installed as non-direct vent,
only one wall penetration is necessary for the exhaust
vent.
IMPORTANT:
Do not install on the prevailing winter wind
side of the structure.
IMPORTANT:
Maintain a minimum of 12 inches (U.S.)
above grade or the highest anticipated average snow level
(whichever is greater) to the bottom of the vent cover or, in
Canada, terminations must conform with CSA B149.1-10,
Sect. 8.14, Canadian Natural Gas and Propane Installa-
tion Code.
NOTE:
Dimensions between the inlet and outlet pipes (di-
rect-vent only) are fixed by the sidewall termination. Other
drawings in this manual which specify minimum and/or
maximum distances (vertical and horizontal) between
pipes do not apply to the sidewall termination kit.
NOTE:
Multiventing – NO COMMON VENTING IS PER-
MITTED WITH THIS KIT.
NOTE: With this option a trap on the inlet combustion
air pipe is NOT required.
NOTE:
Install the vent and air intake piping into the vent
plate openings. Seal all gaps between the pipes and wall.
BE SURE TO USE SILICONE SEALANT
to seal the vent
pipe to the vent cap to permit field disassembly for annual
inspection and cleaning. Also seal all pipe penetrations in
the wall.
DO NOT INSTALL VENT kITS ONE ABOVE
THE OTHER
to prevent the possibility of condensate
freeze-up or recirculation.
NOTE:
Vent should protrude a maximum of 2-1/4 inches
beyond the vent plate. Air intake should protrude a maxi-
mum of 1 inch beyond the vent plate.
NOTE:
The RXGY-G02 termination can be used with 3”
vent pipe. A maximum of 18” of 2”
B
pipe can be used be-
fore penetrating the wall.
Complete installation instructions are included with these
kits.
ST-A1194-46
ST-A1194-46
8”
MIN.
8”
MIN.
FIGURE 25
TyPICAL INSTALLATION – DIRECT VENT
FIGURE 24
VENT kIT INSTALLATION OPTIONS
Summary of Contents for (-)98VA060M317USA
Page 12: ...Field Conversions FIELD CONVERSIONS 12 ...
Page 13: ...FIELD CONVERSIONS Field Conversions 13 SEE NExT PAGE FOR APPLICABLE CONFIGURATIONS ...
Page 15: ...Field Conversions 15 ...
Page 16: ...Field Conversions ST A1194 68 00 16 ...
Page 17: ...Field Conversions 17 ...
Page 18: ...Field Conversions 18 ...
Page 92: ...92 Diagnostics TABLE 19 R98V FAULT CODES WITH DESCRIPTIONS AND SOLUTIONS ...
Page 93: ...93 TABLE 19 continued R98V FAULT CODES WITH DESCRIPTIONS AND SOLUTIONS Diagnostics ...
Page 94: ...94 Diagnostics TABLE 19 continued R98V FAULT CODES WITH DESCRIPTIONS AND SOLUTIONS ...
Page 95: ...95 TABLE 19 continued R98V FAULT CODES WITH DESCRIPTIONS AND SOLUTIONS Diagnostics ...
Page 96: ...96 Diagnostics TABLE 19 continued R98V FAULT CODES WITH DESCRIPTIONS AND SOLUTIONS ...
Page 97: ...97 TABLE 19 continued R98V FAULT CODES WITH DESCRIPTIONS AND SOLUTIONS Diagnostics ...
Page 98: ...98 Diagnostics TABLE 19 continued R98V FAULT CODES WITH DESCRIPTIONS AND SOLUTIONS ...
Page 99: ...99 TABLE 19 continued R98V FAULT CODES WITH DESCRIPTIONS AND SOLUTIONS Diagnostics ...
Page 100: ...100 Diagnostics TABLE 19 continued R98V FAULT CODES WITH DESCRIPTIONS AND SOLUTIONS ...
Page 101: ...101 TABLE 19 continued R98V FAULT CODES WITH DESCRIPTIONS AND SOLUTIONS Diagnostics ...
Page 105: ...105 FIGURE 67 MODULATING ECM FURNACE WIRING DIAGRAM Troubleshooting ...
Page 106: ...106 ...
Page 107: ...107 ...
Page 108: ...108 CM 0717 ...