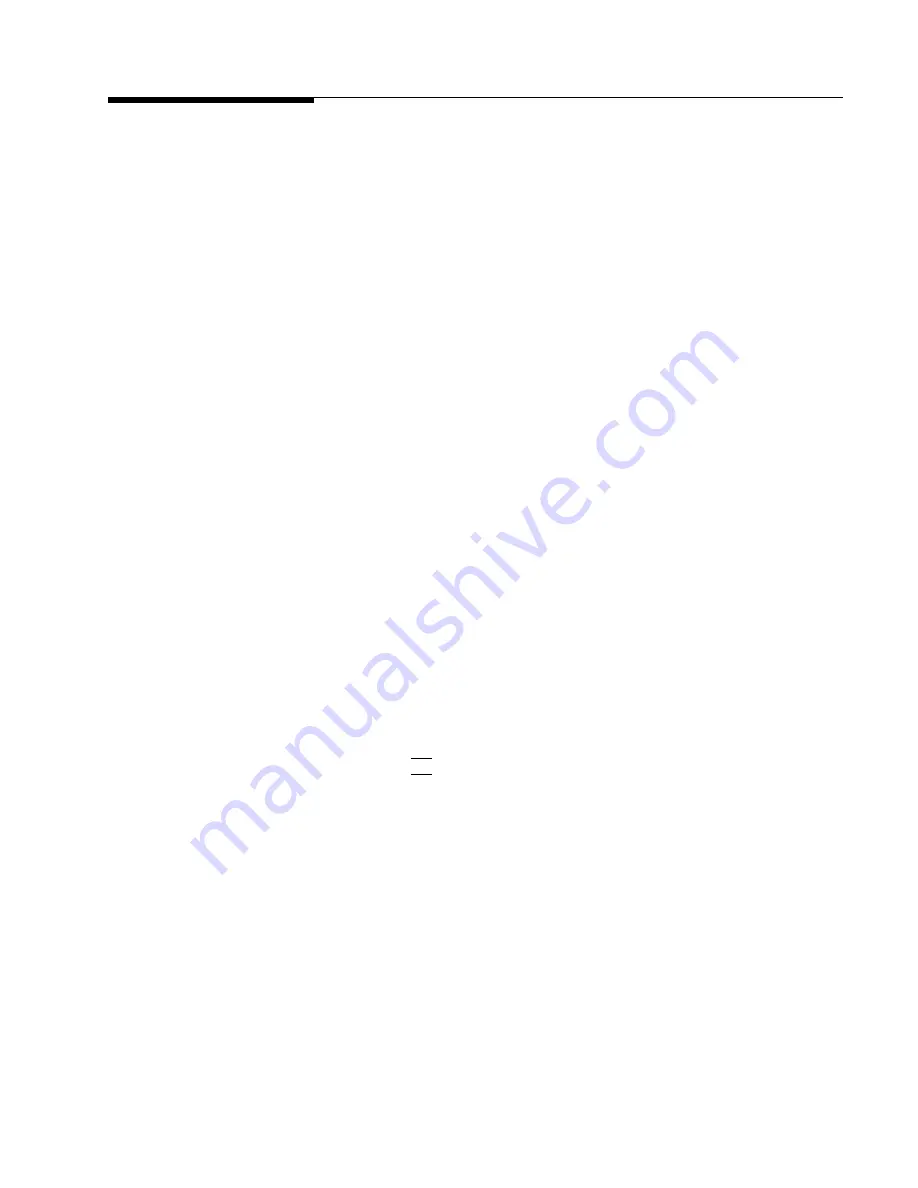
Characterizing
the
Detector
(P
erforming
a
P
o
w
er
Calibration)
T
o
obtain
the
b est
accuracy
,
and
to
meet
the
\corrected"
dynamic
accuracy
sp ecications,
eac
h
detector
m
ust
b e
c
haracterized
on
the
8757D
input
on
whic
h
it
will
b e
used.
The
c
haracterization
routine
simultaneously
corrects
b oth
A
C
and
DC
measuremen
ts.
This
routine
is
also
useful
as
an
op erator's
c
hec
k
to
ensure
the
detector
is
op erating
prop erly
.
Only
the
8757D
with
an
Option
002
p o
w
er
calibrator
ha
v
e
this
capabilit y
.
Detector
c
haracterization
b egins
at
+20
dBm
and
decreases
in
1
dB
incremen
ts
do
wn
to
035
dBm.
T
o
reduce
measuremen
t
time,
p o
w
er
steps
are
larger
than
1
dB
at
low
er
p o
w
er
lev
els.
Correction
v
alues
will
b e
generated
o
v
er
this
range
if
the
detector
is
op erational.
It
will
also
correct
for
an
y
loss
in
the
detector
up
to
ab out
50
dB.
F
or
example,
lets
assume
a
DC
detector
has
a
dynamic
range
of
+20
to
050
dBm.
A
30
dB
attenuator
is
then
placed
on
the
detector
and
a
c
haracterization
is
p erformed.
Up on
completion,
the
detector
will
b e
c
haracterized
from
+20
to
020
dBm.
Applying
a
0
dBm
signal
to
the
detector/pad
com
bination
will
result
in
a
0
dBm
reading;
not
a
030
dBm
reading
whic
h
is
what
the
detector
itself
is
actually
seeing.
A
loss
of
more
than
ab out
50
dB
may
result
in
an
error
message
b eing
display
ed
on
the
analyzer.
This
could
o ccur
if
the
detector
is
defectiv
e
or
if
y
ou
simply
forgot
to
connect
the
detector
under
test
to
the
P
o
w
er
Cal
Output
of
the
8757D.
Up on
completion
of
this
routine,
the
dynamic
range
of
the
detector
will
b e
display
ed;
v
erify
that
it
is
correct
for
the
curren
t
detection
mo
de,
taking
in
to
accoun
t
an
y
attenuation
due
to
added
pads
or
other
devices,
or
due
to
inheren
t
loss,
suc
h
as
in
a
directional
bridge
whic
h
t
ypically
has
12.5
dB
of
loss.
T
o
c
haracterize
the
detector
(p erform
a
p o
w
er
cal),
connect
the
detector
to
the
desired
input
of
the
8757D.
Connect
the
RF
input
of
the
detector
to
the
calibrator
output.
Make
sure
the
analyzer
has
b een
on
and
the
detector
connected
for
at
least
30
min
utes.
1.
Press
4
CAL
5.
2.
Select
NNNNNNNNNNNNNN
MORE
.
3.
Select
NNNNNNNNNNNNNNNNNNNNNNNNNNNNN
POWER
CAL
.
4.
Select
NNNNNNNNNNNNNNNNNNNNNNNNNNNNNNNNNNNNNNNNNNNN
DET
A,B,C
or
R
.
5.
Select
NNNNNNNNNNNNNNNNNNNNNNNNNNNNN
START
CAL
.
A
complete
c
haracterization
for
one
detector
takes
ab out
60
seconds.
Once
c
haracterized,
do
not
unplug
the
detector
from
the
analyzer
or
y
ou
will
ha
v
e
to
p erform
another
c
haracterization.
This
is
b ecause
the
8757
automatically
recalibrates
itself
when
it
senses
a
detector
has
b een
remov
ed
or
connected
to
the
detector
inputs.
Ho
w
ev
er,
the
analyzer
c
an
b e
turned
o
and
on
again
without
losing
this
information.
P
erform
the
c
haracterization
at
least
once
p er
da
y
and
more
often
if
the
temp erature
v
aries
b
y
more
than
65
C.
Operation
3-7
Summary of Contents for 85037A
Page 19: ...Figure 2 3 SMA and 3 5 mm Connector Cross Sections and SWR Performance Installation 2 5...
Page 22: ......
Page 30: ......
Page 46: ...4 16 Performance Tests...
Page 50: ...4 20 Performance Tests...
Page 54: ......
Page 62: ...Figure 6 2 Module Exchange Program 6 4 Replaceable Parts...
Page 64: ......
Page 68: ...Repair Figure 7 2 Cable Connections 7 4 Service...
Page 74: ......