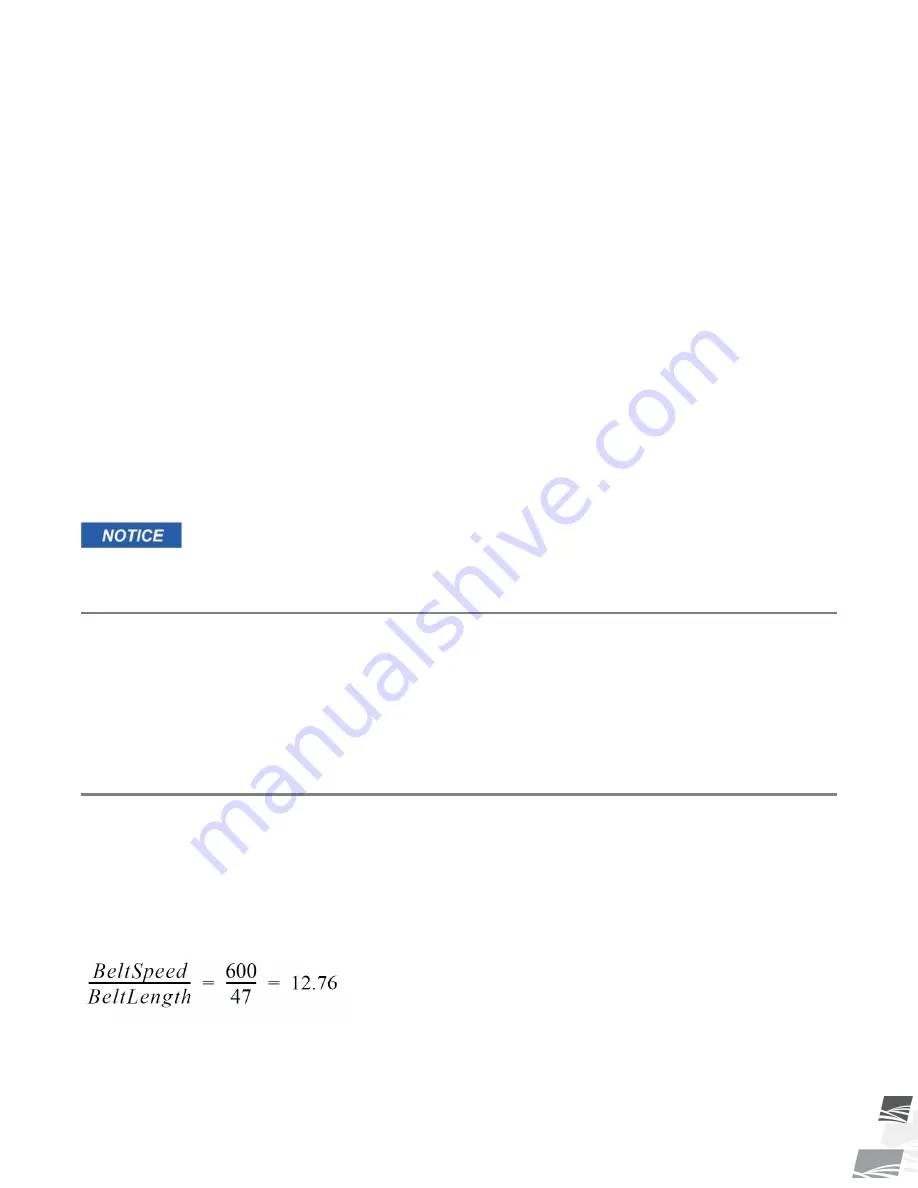
P1512137 R3
47
3. Align the tractor axis with the conveyor input shaft to minimize the angles of the universal joints on the PTO
driveline.
Important
Check that the PTO does not exceed the maximum operating angle, refer to
.
4. Ensure the PTO drive on the tractor is in the off position before starting the tractor.
5. Start tractor engine at low idle, slowly engage the PTO with the tractor idling to prevent unneeded stress on
the drive components and shear bolts.
6. If everything is operating normally, start running grain through the conveyor and increase the tractor PTO to
the specified full speed to produce the required flow.
7. To shut down, reduce the speed to low idle and lock out the PTO.
8. Disconnect the PTO driveline from the tractor and secure it to the PTO transport saddle with the safety
chain and keep it in transport saddle when transporting.
When raising or lowering the conveyor:
Disconnect the PTO driveline.
When starting under load:
If restarting the conveyor under load (tube is full), engage the PTO with the tractor idling.
Engaging the PTO at high engine speed under load will result in equipment damage.
6.6. Loading Area
To achieve maximum capacity:
• Feed material onto the belt until the material tube clearance is 1/2”.
• Direct the flow of material into the input hopper in the direction of the belt travel for the best capacity.
Do not flood feed the hopper.
6.7. Conveyor Belt Speed
The best results are obtained when the input drives are set to provide a conveyor belt speed of 500 to 600 ft/
min on the 1500 series, and 600 to 650 ft/min on the 1800, 2000, and 2400 Series.
Count the number of belt revolutions per minute to determine belt speed. See Specifications for belt length.
Note
Use the connector splice as a reference when counting belt revolutions.
To calculate, for example, 600ft/minute belt speed for a 47ft belt:
Therefore, 12.76 or approximately 13 belt passes per minute will provide a 600ft/min belt speed.
Contact your dealer or the factory for the appropriate drive components to give the recommended belt speed.
S-DRIVE STANDARD CONVEYOR – PORTABLE GRAIN BELT CONVEYOR