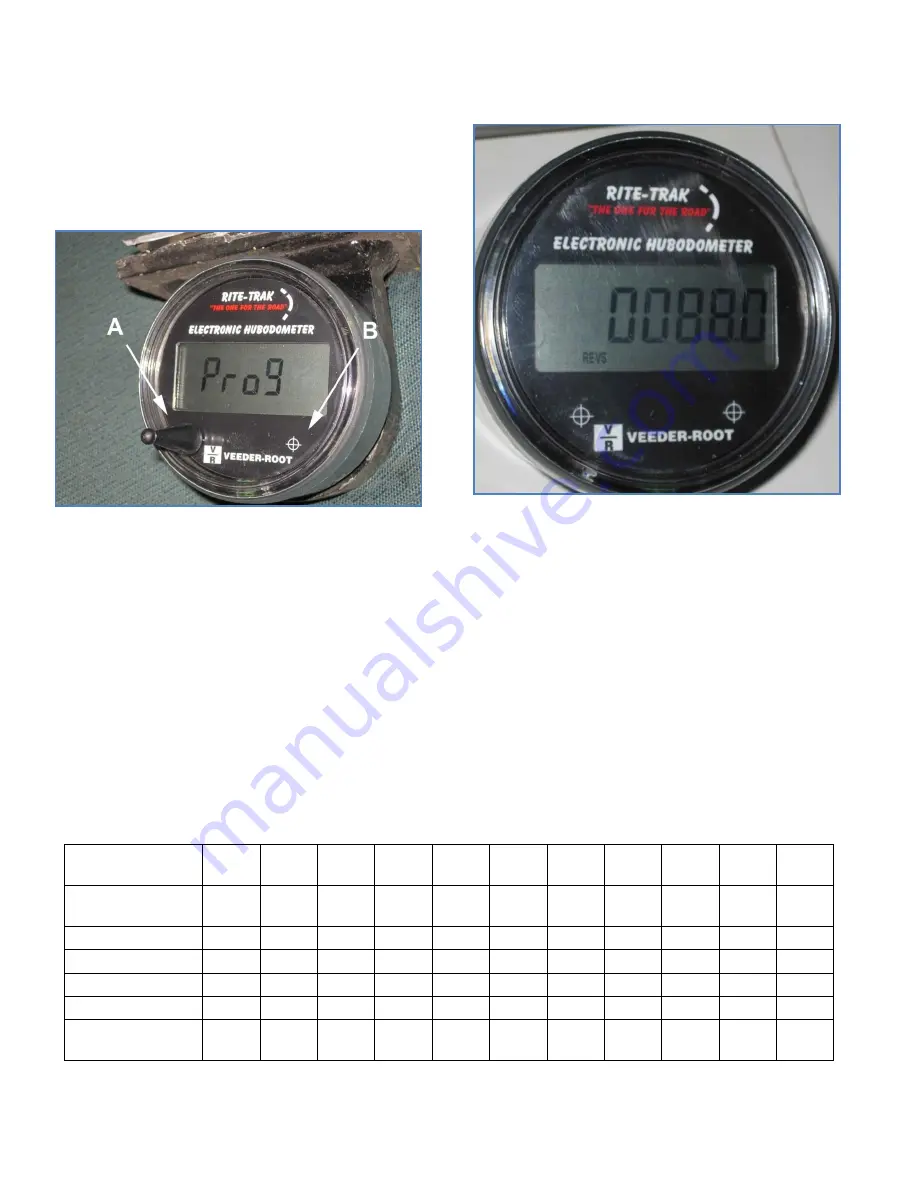
28
5.7. ACRE METER OPTION
The option electronic hubodometer threads into a ½”
fine hole tapped into the end of the right hand center
roller shaft. Install the acremeter with a oil filter wrench
to 23 lb foot of torque with a lock washer to ensure that
the unit is not lost. t is protected by a flange welded
onto the The Veeder Root electronic acre meter.
FIGURE 25 ACREMETER TO PROGRAM
MODE
See Figure 25 ACREMETER TO PROGRAM
MODE above.
The acre meter calibration is done by touching a
magnet to the outside of the face of the odometer on a
Left spot marked “A” and Right spot marked “B” The
simplified instructions to set to 88.0 for a 45 foot
LandRoller are:
1) Hold magnet on the left position-
“A” – in 6
seconds will read serial number, leave on
MUCH longer
– until PROG shows on screen.
2) Lift off of left calibration for 1 second, touch
magnet down to see units= “acres” set already
3) Lift and touch left again advance to revolutions
per acre, 0000.0 acres per revolution will
show
—should be 0088.0 for a 45 foot –
FIGURE 26 CALIBRATING "REVS" FOR 45
4) Touch left to advance to second left zero-
5) Touch left again to have the third left digit of
0000.0 flashing,
6)
Touch right “B” eight times to have the 0
advance to first “8” of 0088.0
7) Touch left to advance to fourth left digit of
0000.0.
8)
Touch right “B” 8 times to advance to “8” in
the fourth digit.
9) Do nothing for 10-20 seconds, and front
screen will come up reading 88.0 revs acres in
lower left. DO NOT continue to more
programming as the counter may become
locked and of no value.
Consult the tabled below for other calibration numbers.
machine width
feet
17.0
20.0
31.0
40.0
45.0
46.0
52.0
62.0
66.0
70.0
80.0
machine width
meters
5.2
6.1
9.5
12.2
13.7
14.0
15.9
18.9
20.1
21.3
24.4
acres per 1/2 mile
1.0
1.2
1.86
2.4
2.7
2.76
3.2
3.8
4.0
4.2
4.8
rev per one acre
233.0 198.1 127.8
99.0
88.0
86.1
76.2
63.9
60.0
56.6
49.5
rev per 1 hectare
575.8 489.5 3.161 244.7 217.5
213. 188.3 157.9 148.3 139.8 122.4
acres / hour @5
mph
10.3
12.1
18.76
24.2
27.3
27.9
31.5
37.6
40.0
42.4
48.5
Summary of Contents for LandRoller
Page 2: ...PAGE 2 ...
Page 4: ...PAGE 4 ...
Page 15: ...15 ...
Page 16: ...16 ...
Page 33: ...33 7 2 CENTER FRAME ASSEMBLY ...
Page 34: ...34 7 3 INNER WING FRAME ASSEMBLY ...
Page 37: ...37 7 6 CENTER SECTION 5 SECTION 62 FOOT END OF ROLLER ...
Page 38: ...38 7 7 CENTER SECTION WHEELS HYDRAULICS ...
Page 39: ...39 7 8 62 FT 5 SECTION RH WING ...
Page 40: ...40 7 9 62 FT 5 SECTION LH WING ...
Page 41: ...41 7 10 OUTER FRAME ROLLER 5 SECTION 62 FT ...
Page 44: ...44 7 13 SPINDLE AND HUB PARTS 8 BOLT 113686 ...
Page 45: ...45 7 14 HYDRAULIC SCHEMATIC 5 SECTION 62 FT BOOM ...
Page 47: ...47 This page intentionally blank ...
Page 49: ...49 ITEM ITEM The end ...
Page 54: ...54 ...
Page 55: ...55 ...