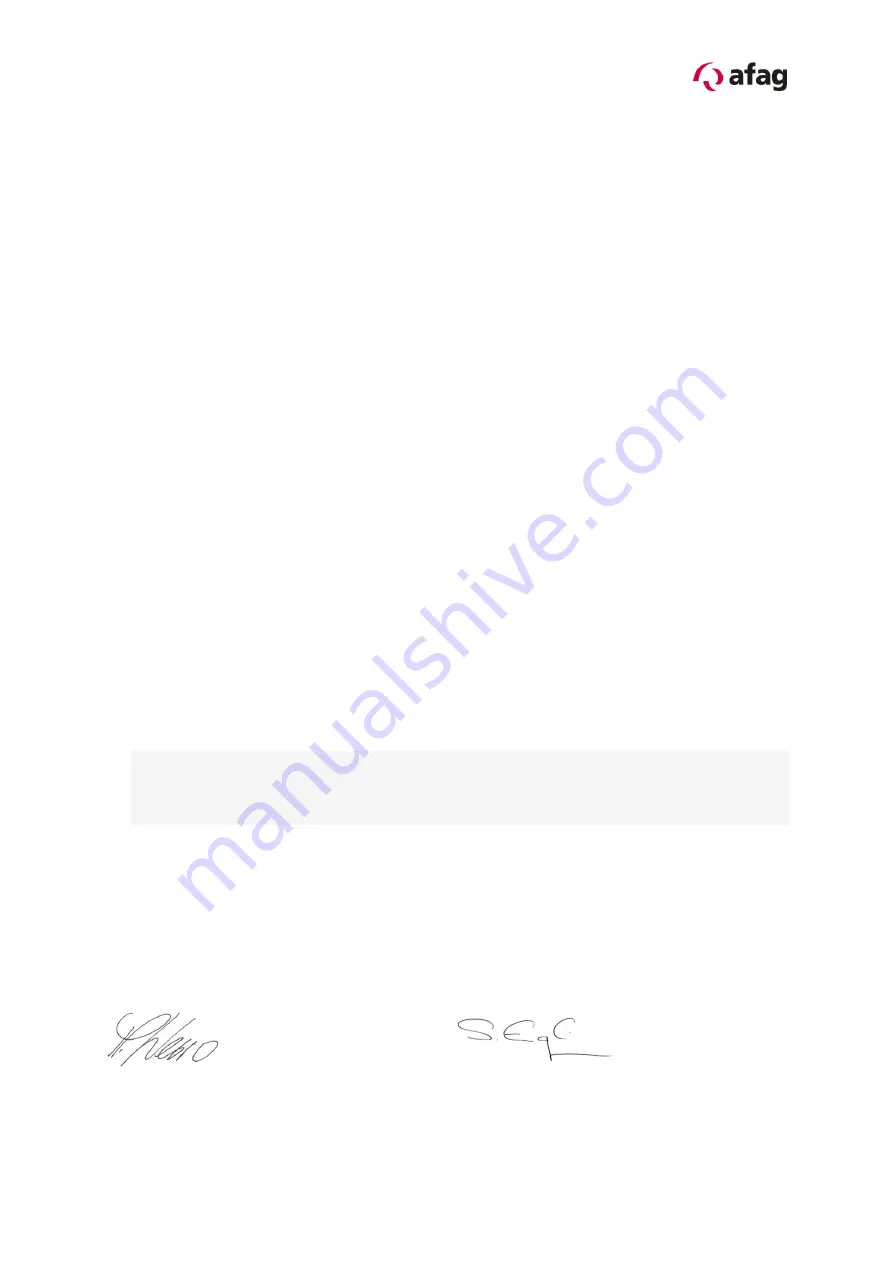
SA-1-OI-vers. 2.2 gb.23.07.14
1.0.0 EC Declaration for Incorporation
1.1.0 According to 2006/42/EC dated 09. June 2006, Appendix II B VI for
Incorporation of partly completed machinery.
The manufacturer:
Afag Automation AG, Fiechtenstrasse 32, CH-4950 Huttwil
Tel. +41 62 959 87 02, www.afag.com
As manufacturer of the partly completed machine we declare that:
-
The specified machine corresponds to the listed essential requirements of the
directive 2006/42/EG, wehere applicable the other directives and standards
listed below.
Designation:
Telescope spindle axis
(electrical)
Type :
SA-1-50 / SA-1-100 / SA-1-150
Sequential series
No. 50xxxxxx
-
Machinery Directive 2006/42/EC
-
Low voltage Directive 2006/42/EG
-
The relevant technical documentation is complied in accordance with part B of
Annex VI
-
The relevant technical documentation in accordance with part B of Annex VI
will be transmitted in response to a reasonable request by the national
authorities in printed from or in electronic from (pdf).
Notes to the Declaration of Incorporation according to the Machinery Directive
2006/42/EC, Annex IIB, section 4
(Checklist on accurate and basic health and safety requirements).
-
1.1; 1.1.1; 1.1.2; 1.2; 1.2.1; 1.2.3; 1.2.4.4; 1.2.5; 1.3; 1.3.3; 1.3.5; 1.3.6; 1.3.7;
1.3.8.1; 1.3.8.2; 1.3.9; 1.4; 1.4.1; 1.5; 1.5.1; 1.6; 1.6.1; 1.6.3; 1.6.4; 1.7; 1.7.1; 1.7.4.;
1.7.4.1; 1.7.4.2; 1.7.4.3; 3.3.5; 3.4.1
-
Increase of the harmonized standards applied:
-
EN 349; EN ISO 12100-1; EN 12100-2; EN ISO 14121-1; EN 60204-1: 2006
partly
fulfilled
-
This partly completed machinery must not be put into service until the final machinery
into which it is to be incorporated has been declared in conformity with the provisions
of this Directive 2006/42/EC, where appropriate.
Name and address of the person authorised to compile the relevant technical documentation:
Lanz Beat, PM & Marketing-Services, Afag Automation AG
Place/Date: Huttwil, 23.07.2014
Markus Werro
Managing Director
Afag Automation AG
Siegfried Egli
Head of HT
Afag Automation AG
5
Summary of Contents for SA-1 Series
Page 10: ...SA 1 OI vers 2 2 gb 23 07 14 2 1 4 Slide unit load factors 10 ...
Page 18: ...SA 1 OI vers 2 2 gb 23 07 14 2 2 2 SE 24 18 ...
Page 19: ...SA 1 OI vers 2 2 gb 23 07 14 2 2 3 SE 48 19 ...
Page 20: ...SA 1 OI vers 2 2 gb 23 07 14 2 2 4 SE Power 20 ...
Page 21: ...SA 1 OI vers 2 2 gb 23 07 14 2 2 5 Servo controller 21 ...
Page 30: ...SA 1 OI vers 2 2 gb 23 07 14 3 1 6 Dimension for SA 1 30 ...
Page 31: ...SA 1 OI vers 2 2 gb 23 07 14 3 1 7 Technical data 31 ...