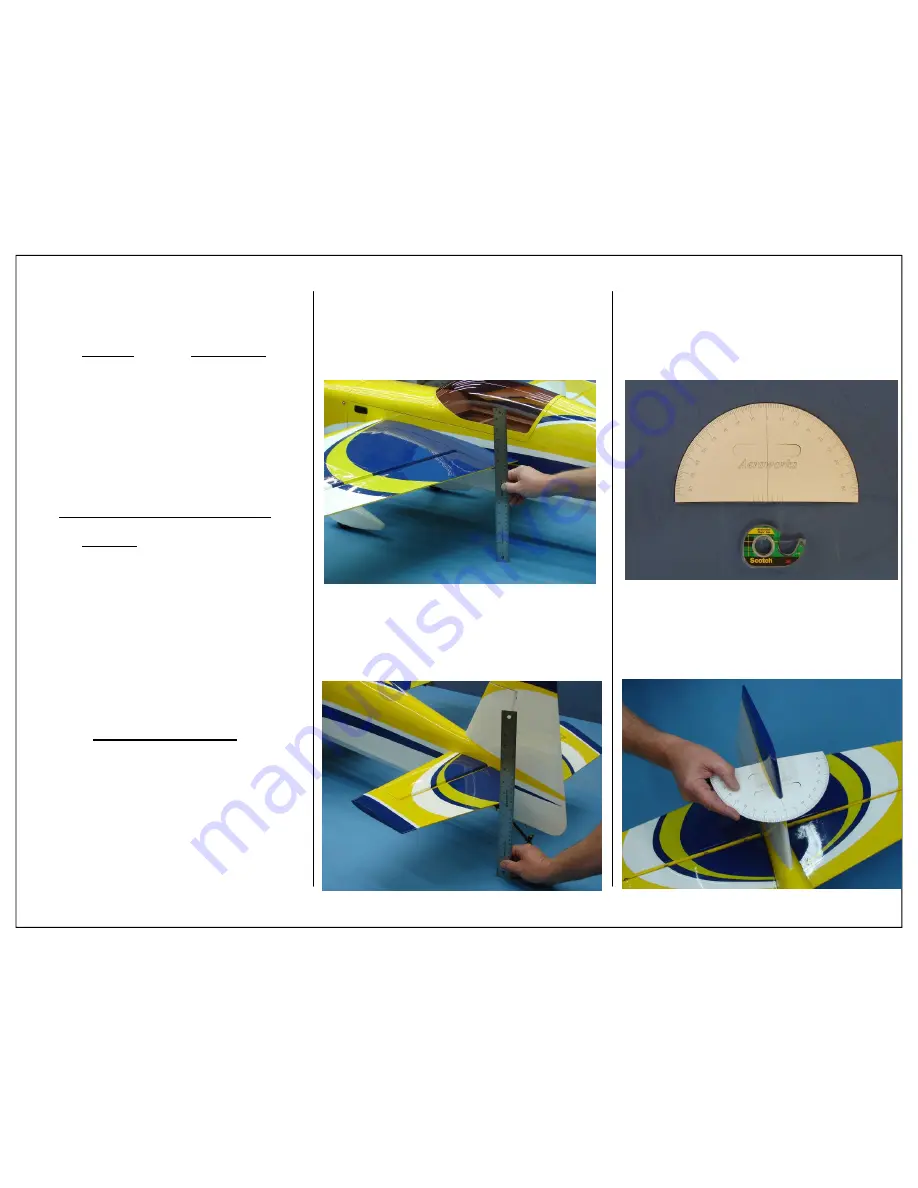
48
Aeroworks 30cc Freestyle Extra 260 Assembly Manual
1. Use the widest part of the aileron as shown to
measure the aileron throw in inches.
2. Use the widest part of the elevator as shown to
measure the elevator throw in inches.
Low
Rate Medium
Rate
Aileron
1 1/2” or 15˚ up
2 1/4” or 25˚ up
1 1/2” or 15˚ down 2 1/4” or 25˚ down
Rudder
15˚ left
30˚left
15˚ right
30˚right
Elevator
7/8” or 12˚ up
1 1/2 ” or 20˚ up
7/8” or 12˚ down
1 1/2” or 20˚ down
For 3D flying use the following throws:
High
Rate
Aileron
3 1/2” or 40˚ up
3 1/2” or 40˚ down
Rudder
45˚ left
45˚ right
Full rudder deflection is typically
recommended for all out 3D
Elevator
3 3/4” or 50˚ up
3 3/4” or 50˚ down
Recommend Expediential:
25% expediential on low rates
45% expediential on medium rates
60% expediential on high rates
Use the given rates as a starting point. Then
adjust rates to suit your own flying style.
CONTROL THROW
DEFLECTION TABLE
3. Gather the Aeroworks Rudder Throw Meter
(
Supplied
) and clear tape.
4. Slide the throw meter under the rudder boost tab.