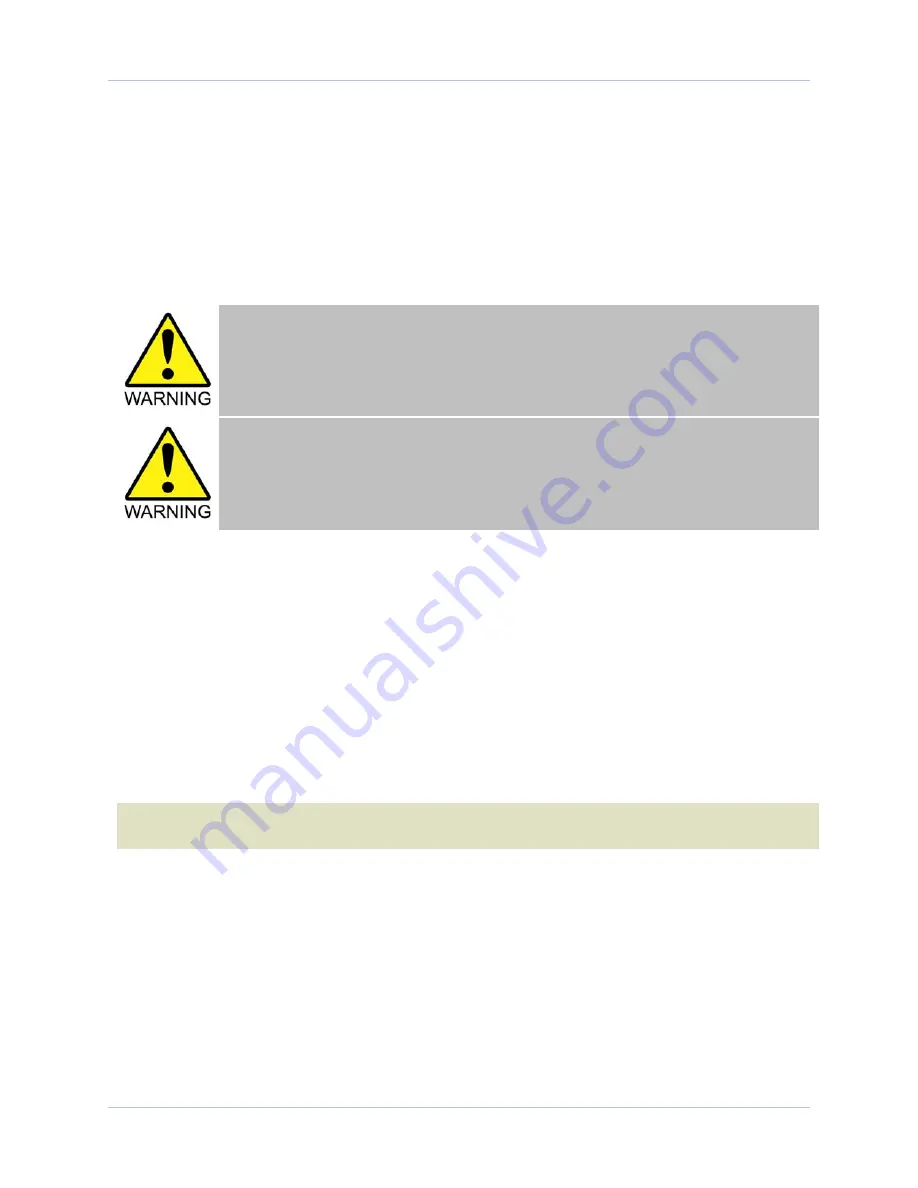
Installation
ASR1200 Rotary Stage User's Manual
2.6. Electrical Installation
Aerotech motion control systems are adjusted at the factory for optimum performance. The ASR1200 series
stage is part of a complete Aerotech motion control system. Setup involves connecting the stage and motor
combination to the appropriate drive chassis with the cables provided. Connect the provided cables to the
feedback and motor connectors on the stage.
Labels on the drive indicate the appropriate connections. Refer to your drive manuals and documentation for
additional installation and operation information. In some cases, if the system is uniquely configured, a draw-
ing showing system interconnects is supplied.
Never connect or disconnect any electrical component or connecting cable while power is
applied, or serious damage may result.
Use only the cables provided by Aerotech as part of the complete motion control system.
2.7. Air Requirements
The air pressure supplied to the collet chuck is important in ensuring that the material or tool is released prop-
erly.
l
If compressed air is used, it must be filtered to 0.25 microns, dry to 0º F dew point, and oil free.
l
If nitrogen is used, it must be 99.99% pure and filtered to 0.25 microns.
The chuck becomes fully open at approximately 4-5.5 bar (60-80 psig) depending on the collet size. Higher
pressures will not cause damage to the rotary union, but high flow rates will result. Because of the non-
contact rotary union design on collet-equipped stages, a small amount of leakage will occur. Approximate
leakage rates of between 10 Lpm (0.5 CFM) and 40 Lpm (1.4 CFM), depending on pressure, will be observed
when the collet is open.
N O T E :
When operating the ASR1200 it is recommended that 5 psi be supplied to the collet at all times.
This will act as an air purge and help prevent contaminants from entering rotary union.
2.8. Wet Cut Fluid Requirements
Water or cutting fluid used during wet cut operations must be conditioned to meet certain requirements ensur-
ing seal functionality and service life of the wet cut rotary union.
l
Water or cutting fluid must be filtered to 5 microns or better.
l
Fluid filter must be installed upstream of the rotary union between pump outlet and rotary union inlet.
16
Chapter 2
www.aerotech.com