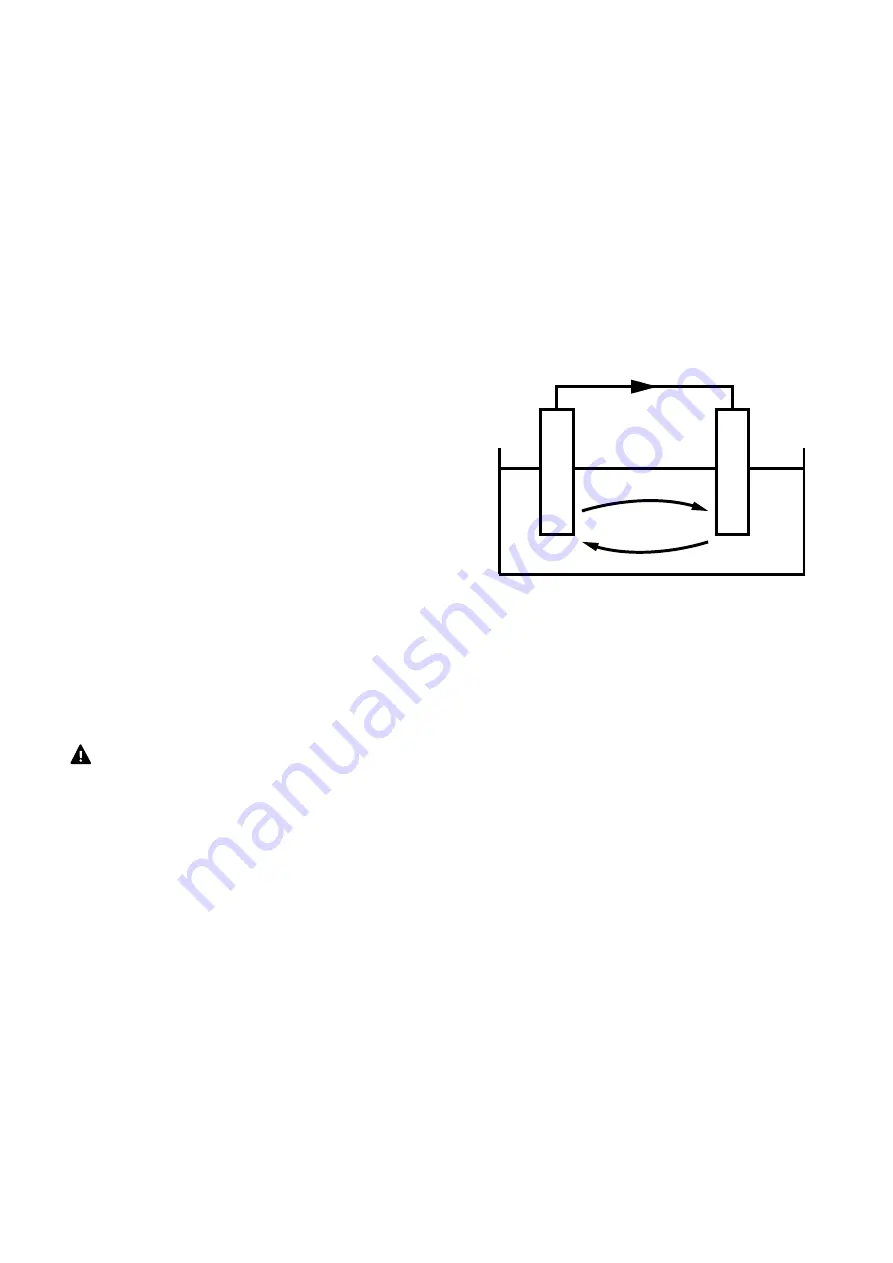
16
The main material in Aermec heat exchangers is aluminium.
Aluminum is a very reactive metal, which is easily oxidized on its surface. As
long as this hard layer of aluminum oxide remains intact, the aluminum at
the base will remain resistant to corrosion (unlike other materials, such as
steel, where the oxide layer peels off the surface and flakes off, allowing the
constant attack of the underlying metal).
However, aggressive environments can damage the oxide layer, which may
not regenerate as quickly as necessary to provide the product with sufficient
protection.
These harsh environments are typified by very high or very low pH levels.
Normally, aluminum’s protective oxide layer is generally stable in the pH
range of 4.5 to 8.5; the lack of exposure to excessively acidic or basic pH
conditions is not in itself sufficient to exclude the need for appropriate pro
-
tective treatments on the batteries.
The presence of salt (associated with marine environments) as well as the
presence of other aggressive substances can in fact induce widespread or
localized galvanic corrosion (pitting or anthill corrosion).
OTHER RISK FACTORS FOR CORROSION
The principal cause of corrosion is elevated humidity and/or temperatures
in the presence of contaminant gases. These conditions alone, or in combi
-
nation, accelerate the natural corrosion process in metals.
Humidity
Moisture in air can be considered the lifeblood of galvanic corrosion. A gal
-
vanic corrosion cell requires an electrolyte or current carrying media, to
reach a dynamic state. The electrolyte can be water or any water-soluble
substance with good conducting properties. Moisture in the air is one such
electrolyte. Humid air contaminated with corrosive gasses further accelera
-
tes the corrosion rate as the air’s current carrying otential increases.
Temperature
Chemical reactions generally depend on the temperature, for reactions that
involve corrosion of aluminum by an increase in temperature, faster reac
-
tion frequencies usually arise.
Corrosive gases
Not all gases cause corrosion. Specifically, we are concerned with three
types of gases:
—
Acidic gases, such as hydrogen sulfide, sulfur oxides, chlorides, hydrogen
fluoride (HF) and nitrogen oxides;
—
Caustic gases, such as ammonia;
—
Oxidizing gases, such as ozone
Of the gases that can cause corrosion, the acidic gases are typically the
most harmful.
FLOW OF ELECTRONS
FLOW OF IONS (+)
FLOW OF IONS (-)
ELECTROLYTE
ANODE
AND-
CATHODE
Keeping the surfaces of the microchannel coils clean is essential to ensure
the correct operation of the unit and to avoid punctures on the coil with the
consequent loss of refrigerant gas which would lead to the replacement of
the coil itself.
WARNING Damage to the coil due to neglect or lack of or poor clea
-
ning is not covered by the warranty.
Dirt, grease, oil, and other foreign material must be removed periodically from
the surface of the battery according to the following recommendations.
Required elements:
—
Personal protective equipment
—
Hot water
—
High-pressure washing
Procedure:
Use a high-pressure washer with a large cast and enough force to remove all
foreign material, proceed with care to avoid damage and possible wear of the
louvers.
Lastly, also rinse the carpentry and the fans thoroughly to be sure that all im
-
purities have been removed.
Aermec assume no liability for the completeness of the information con
-
tained in this document.
BASIC PRINCIPLES ON MICROCHANNEL COIL CORROSION
CLEANING MICRO-CHANNEL COIL
Summary of Contents for NRV 0550
Page 2: ......