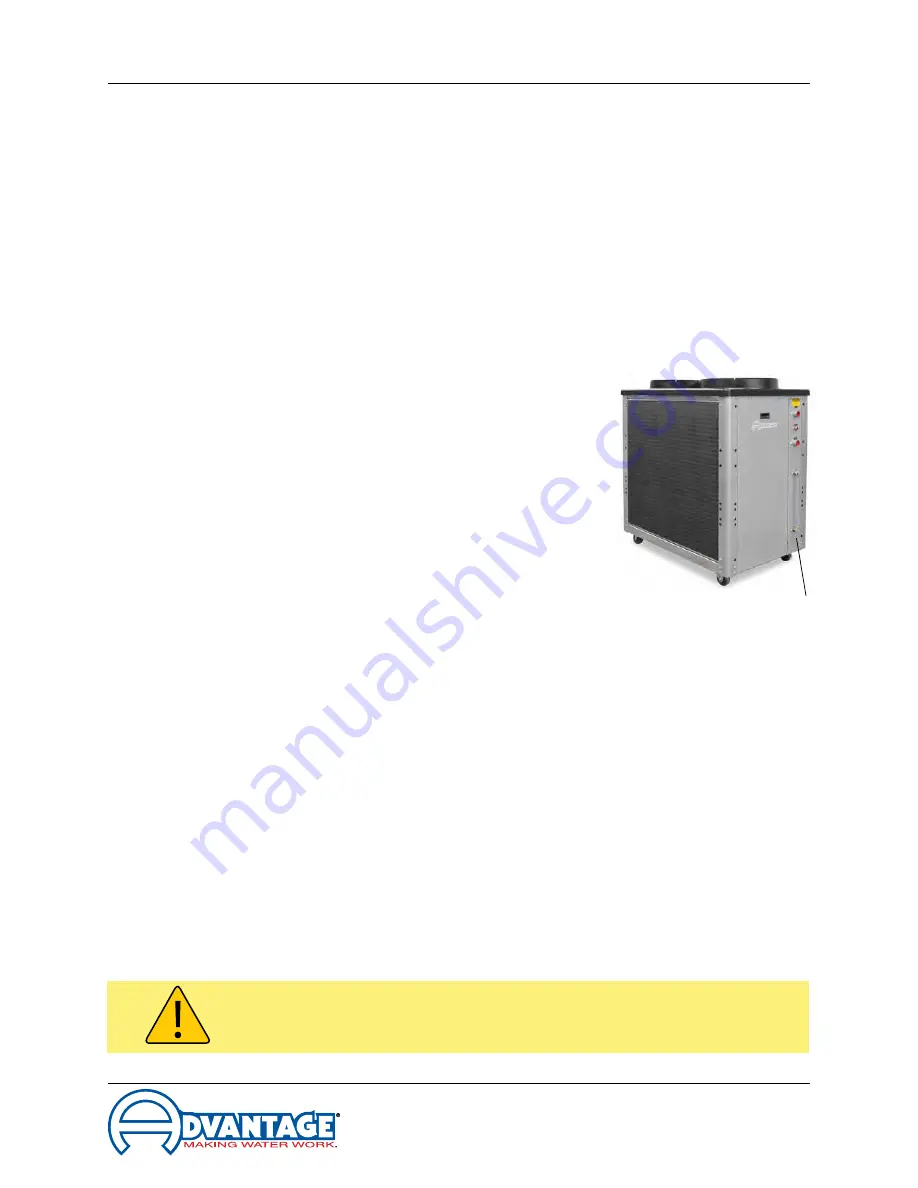
Glycol Chillers : BC Series with MG Control Instrument
Page: 23
ADVANTAGE ENGINEERING, INC.
525 East Stop 18 Road Greenwood, Indiana 46142
317-887-0729 Fax: 317-881-1277
Service Department Fax: 317-885-8683
Email: [email protected]
3.
WATER QUALITY CONTROL. Lack of, as well as, improper water treatment can
damage the chilling unit. The services of competent water treatment specialist
should be obtained and their recommendations followed. It is the equipment
owner’s responsibility to prevent damage from foreign material or inadequate
water treatment. See water treatment section in section 1.6 of this manual for
more information.
4.
FOR AUTOMATIC FILL: Always install a manual shut off valve on the make-up
water supply on the outside of the unit. When electrical power is applied to the
unit and the display is in “Standby” or “Standby Ready” open the owner supplied
shut off valve. The level switch will activate the make-up solenoid which will open
and the water supply will fill the reservoir tank. Do not use automatic fill when
operating at a set point temperature below 48°F with glycol. Dilution may
occur resulting with significant equipment damage.
5.
MANUAL FILL: Disconnect and lock out the
electrical power supply and remove all necessary
cover panels to access the reservoir. Add fluid
directly to the reservoir. When the pump is first
started, as process lines are filled and air is purged,
additional fluid may be required to restore the
reservoir to the correct level. Verify reservoir level
via the coolant sight glass.
6.
Do not use straight deionized or RO (reverse
osmosis) water in this unit unless your unit was
specifically designed for use with deionized water.
Consult factory if not certain.
B.
PROPER ROTATION (PHASING) OF SCROLL COMPRESSORS & PUMPS & FANS
1.
Correct compressor(s), propeller fan(s), centrifugal blower(s) (on air-cooled units)
and pump(s) rotation is critical for unit performance and to avoid severe damage
to the compressor.
2.
All compressor(s), propeller fan(s), centrifugal blower(s) (on air-cooled units)
and pump(s) will be set to rotate in the same direction during the testing process
at the factory except for units with outdoor remote condensers. The rotation of
compressors and pumps on units with remote condensers must be independently
field checked for correct rotation by others.
3.
After electrical installation the rotation must be checked by observing the pump
motor shaft on the end of the pump and comparing its rotation to the directional
arrow on the motor. If the rotation needs to be changed it should be done at the
main power entry by switching any two power conductors at the terminal block or
customer supplied main power disconnect. Recheck rotation before operating the
units.
Typical coolant sight glass
WARNING: The electrical power is engaged at this point. Caution must be observed while the
electrical supply is engaged and cabinet panels are removed and opened.