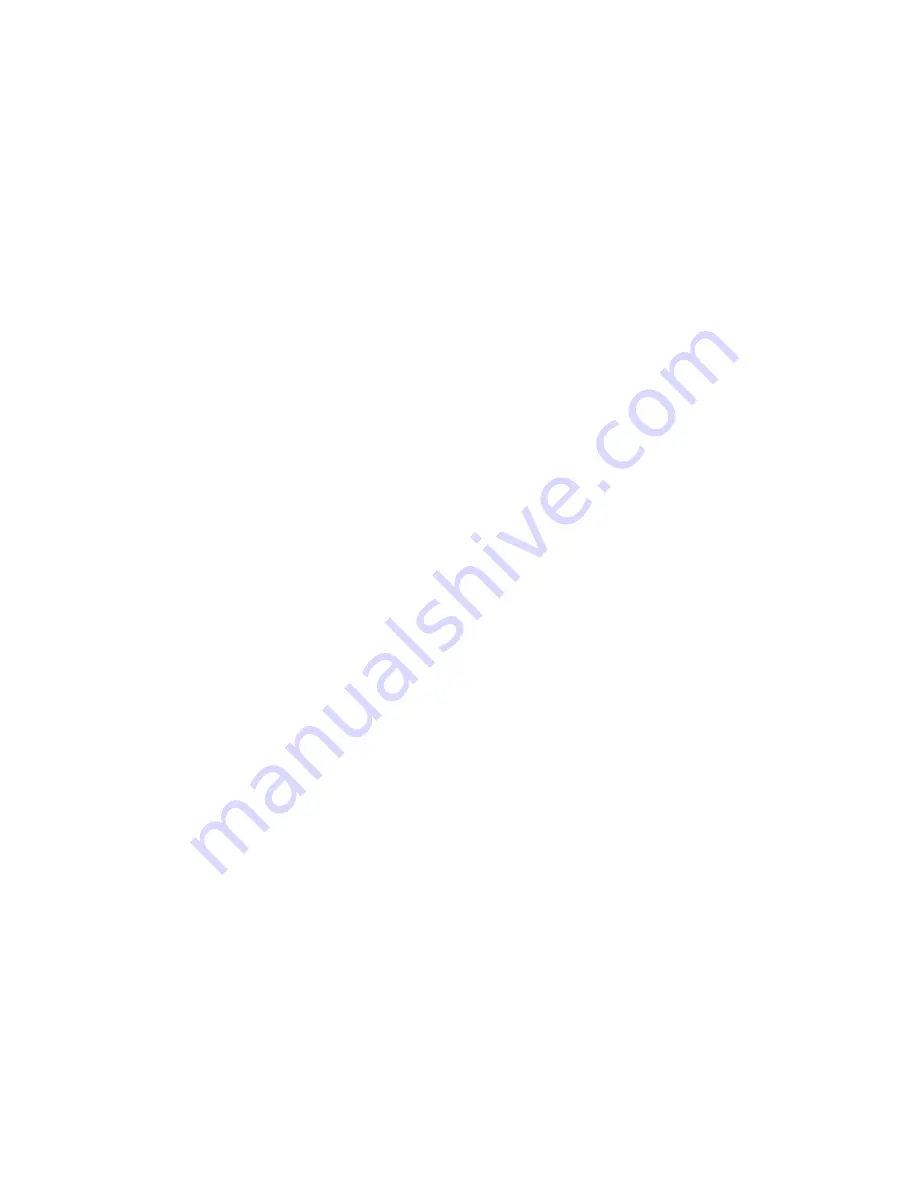
23
4.1 Machine Adjustments
Periodically, the T-300 / T-375 will require readjustment or realignment of components to ensure proper
operation. Adjustments may be required after transportation, excessive handling, or due to normal wear
and tear.
Caution: Machine adjustments, electrical troubleshooting and component replacement should be
performed by qualified maintenance technicians, familiar with safety practices including but not limited
to equipment lock-out/tag-out, voltages, and pneumatics. If you are not familiar with the equipment or
have not received training on the T-300 / T-375, you should consult with APPI technical support before
attempting adjustments or repairs.
4.2 Tracking and Alignment Adjustments
Bags that are not tracking properly can cause product to spill out of the chute or funnel onto the floor.
Tracking problems can also cause the thermally printed information to be out of the proper location.
To avoid spillage or printing problems, machine adjustments to correct the tracking and alignment of the
web of bags may be required.
However, before considering adjustment, check that there is sufficient tension on the web of bags. When
feeding or stopping, the bag roll should not spin freely or feed excess film. The web of bags should not
come in contact with the bottom plate inside the machine. To increase web tension, loosen the knob that
holds the roll and chucks in position, push the roll to the right, into the plastic core plug on the bag roll
and tighten the knob. When pressing the left chuck to the right, the right chuck must not move. See Fig
4-1.
Unwind the bags by hand and check the tension. Then, cycle the machine several times to ensure that the
bags do not break prematurely (too much tension) or does not free wheel (too little tension). For
narrower or shorter bags, proper tension is more critical.
4.3 Compression (NIP) Roller Adjustment
The drive roll compression is the force that exists between the two feed rolls (rubber covered grooved roll
and grooved steel roll). Not enough drive roll compression will prevent the bags from
tearing off
after
each sealing operation. Too much drive roll compression will cause extra wear on the drive roll and the
motor.
Turn the power switch to the OFF position and unplug the power cord. Remove the top cover. The
compression adjustment is located on the latch assembly. See Fig. 4-2.
Compression adjustment is a three-step process. First, the upper and lower roller are adjusted to make the
lower roller parallel to the upper roller. Then, the upper roller is adjusted (lowered) for proper
compression. Finally, the stop bolts are checked to ensure that the latch mechanism is not overextending.
Step 1: Parallel adjustment.
On both the left panel and right panel, loosen the two locking bolts on the upper block of the compression
tension assembly. Loosen the nut on the adjustment screw. With the inner frame locked in the UP
position, lower the lower roller by turning the adjustment screws counter-clock wise until the lower roller
is parallel to the upper roller and leaving 1/16" gap between the rollers. Turn the adjustment screw
clockwise alternatively, keeping the lower roller parallel with the upper roller until the rollers come in
contact across the width of the rollers. Slightly lower the inner frame and raise again to ensure that when
raised again, the rollers touch simultaneously. Then "snug" the upper block bolts and recheck the
alignment.
Note (TIP): A light source (lamp) positioned to the rear of the T-300 / T-375 showing light in the gap of
the rollers will assist in judging whether the upper and lower roller are parallel.