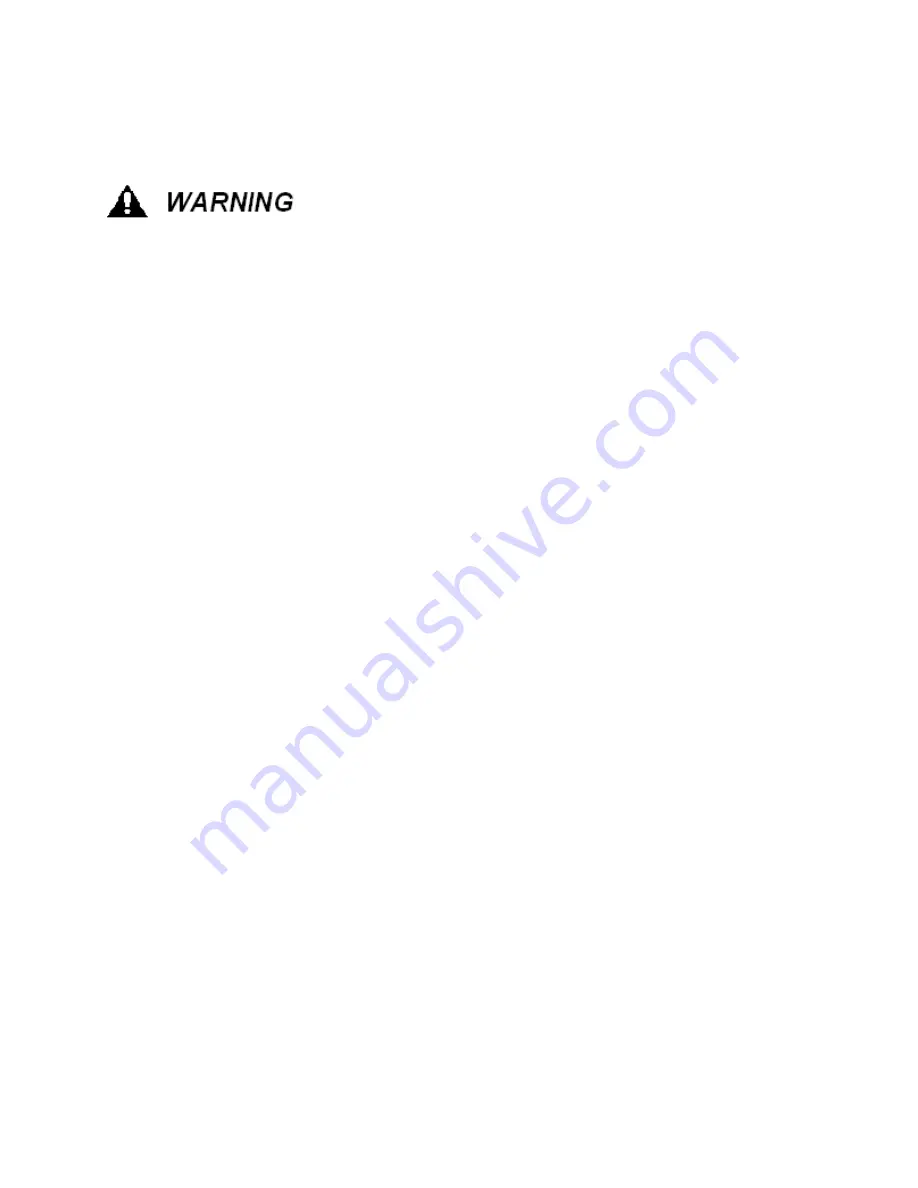
Maintenance
5-2
Roller open and close rate
The rollers must open and close evenly to prevent excessive wear on the cylinders and bearings. This
rate is set at the factory, but can be adjusted in the field. Follow the procedure below to adjust either the
pull rolls or nip rolls.
Maintenance that requires working on the machine while power and
air are connected poses and imminent danger of electrocution or
extremities being caught in rotating parts. Only qualified personnel
should work on a machine in this state
1. There are flow control fittings on both cylinders, but the fittings on the left hand cylinders will require
most of the adjusting.
2. To increase the rate, turn the adjustment screw counter clockwise, to decrease the rate turn the
adjustment screw clockwise. The upper fitting controls the “Open” rate, and the lower fitting controls
the “Close” rate. Do not rotate the screw more than ½ turn at a time.
3. Adjust the open rate until the rolls open correctly, then proceed with the close rate.
4. Lock the adjustment screw in place with the jam nut. Be careful not to turn the adjustment screw as
you tighten the nut.
5. Replace enclosure covers.
Lubrication
Inspect the nip roll bearings at least weekly for grease outside the seals, regrease as necessary. The
bearings on the lower pull roll should be checked for grease leakage after 3 months of use and then every
6 months from there on. The grease should be added slowly with the shaft turning until a slight bead
forms at the seal.
Manufacturer lubrication recommendations:
Std. Temp Bearings: Shell Alvania Grease No. 3
When the bearings are being greased, the bearing gibs should also receive a coating of lithium grease.
The chain should be lubricated as needed with a Lubriplate spray chain lubricant. The tension in the
chain should be checked at 6 months and tightened to take up any stretching that may have occurred,
and then inspected yearly from that point on.