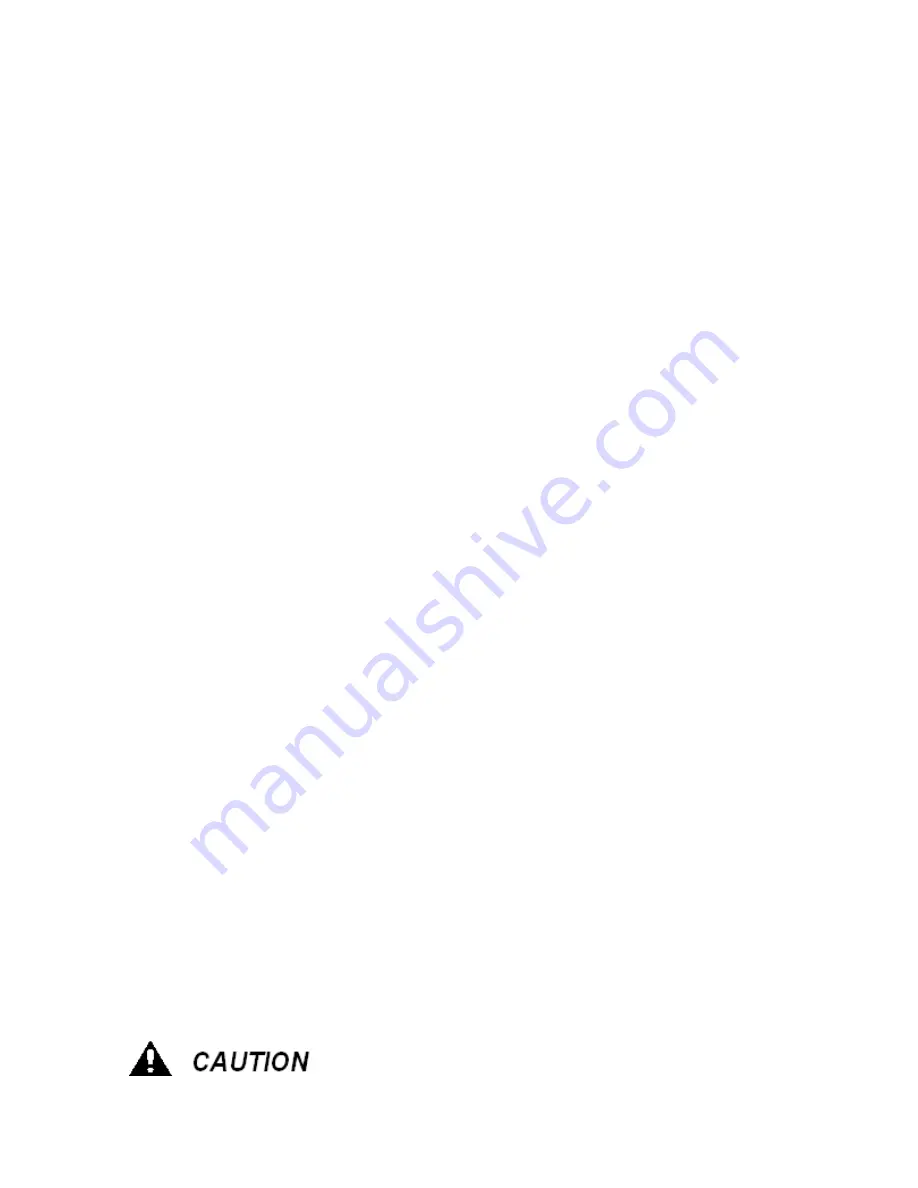
Operation
4-4
Laminator Setup
Your laminator has been designed to make the setup and lamination process as easy and repeatable as
possible, however, there will be techniques that make this phase easier that you will only learn by using
the machine. Do not get frustrated if the setup process takes longer than you expected, the process will
get quicker and easier the more you use your laminator.
The set up process is comprised of the following steps:
1. Loading and positioning the film.
2. Webbing the laminator.
3. Setting the process controls to initial settings.
4. Warm up time (if required by process)
Loading and Positioning the Film
1. Determine the way the film is wound, adhesive inside or outside. This will determine the way it is
placed on the unwind shaft. If the adhesive is wound to the inside, the web will be pulled from the
bottom of the supply roll. The web path configuration figures show the film in this configuration.
2. Press and hold the “Press to Retract” button to pull the retaining sleeve back. Rotate the shaft
out of the sleeve.
3. Remove the locking core chuck and the core idler. The locking core chuck has rollers that rotate
out to hold the core as it turns. Slide the locking core chuck, film roll, and core idler onto the
shaft.
4. Press and hold the “Press to Retract” button to pull the retaining sleeve back. Rotate the shaft
back into position and release the button.
5. Measuring from the sideplates, make sure the film is centered on the shaft. Once the
measurements from each end of film to the sideplates are equal, tighten the locking core chuck
and core idler down.
6. Repeat this process on any other unwind station or rewind using an empty core.
7. If the film is a pressure sensitive with a release liner, you will need to set up a wind up station.
This is done by webbing the film under an idler and separating the film and liner. Once the liner
has been separated from the film, it must be routed up over the second idler and taped to a
windup core.
8. Tape the release liner to the core and windup any slack by hand. Feed the film with adhesive
around and through the nip opening.
Note: You may require feeder stock to keep the film
from
sticking to the lower nip roll.
Webbing the Laminator
The term webbing means routing the film through the laminators’ idlers and nip rolls and thus creating
a web. The easiest way to web the machine up after loading the film is by using a piece of feeder
stock. The stock can be anything that is relatively stiff, but still flexible enough to route around the nip
roll. A common example would be tag board.
The first step in webbing the machine is to have a planned web path configuration. There are two
web path configurations shown for two different processes in this manual. The encapsulation process
uses pressure sensitive film from top and bottom to “encapsulate” the substrate being fed into the
laminator. This process seals the edges and protects the substrate. Refer to figure 4 as the webbing
process is described below.
Pressure Sensitive Process
1. Load film on the rear upper unwind station. Turn the selector switch on this station to “Off”.
2. Set the shim wheels to “0”, place a piece of feeder stock into the nip rolls with plenty of stock
hanging out the front. Close the nip rolls onto the piece of feeder stock.
The nip section can pull you into laminator! Do not place fingers
into the nip section when the rolls are rotating. It is recommended
that operators tie long hair back and not wear neckties, loose clothing and jewelry since they
can be caught in the nip section and pull the operator into the machine