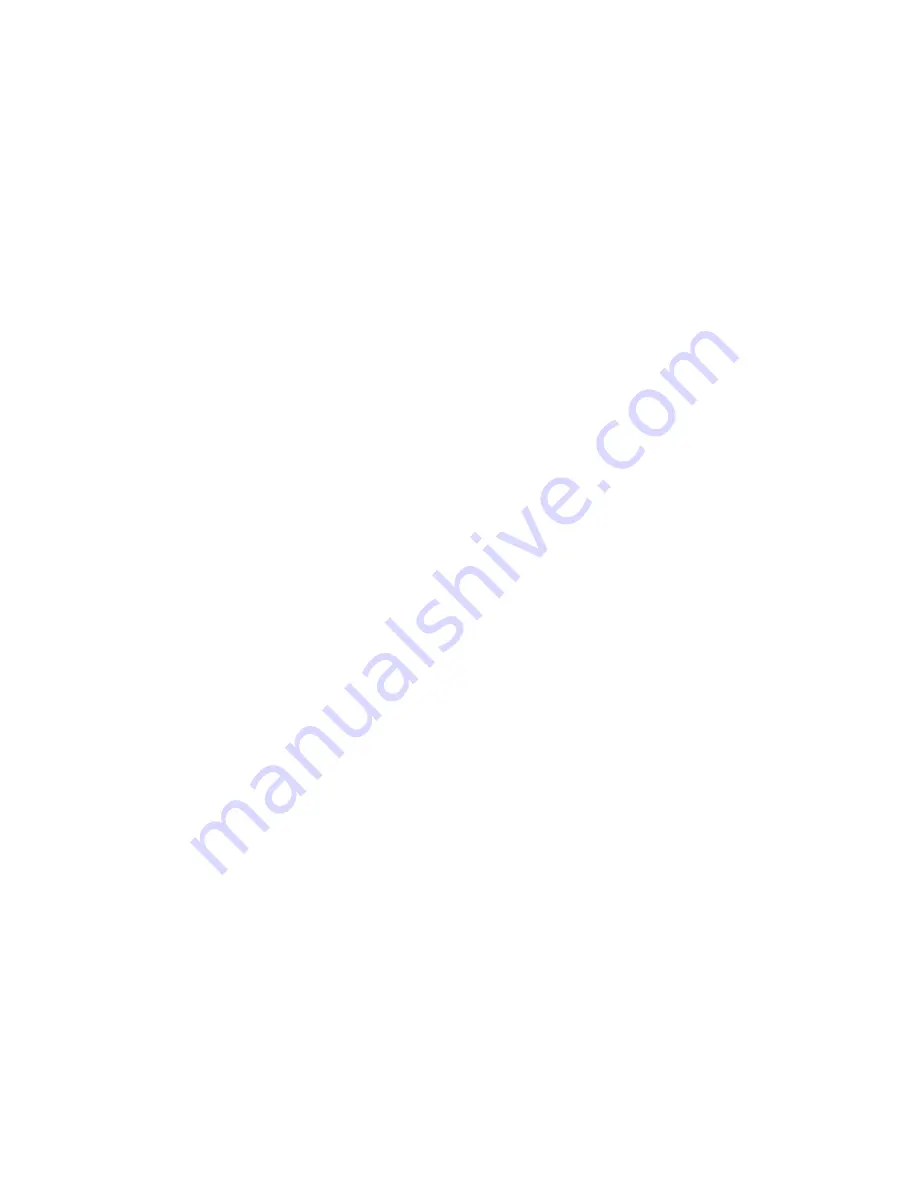
Operation
4-10
Wrinkles in Product
1. Check the adhesive stock for wrinkles while operating. If wrinkles exist, this is a
manufacturing material defect, and must be cut out of the roll. A laminator will not correct
material defects.
2. String the web straight and square between the unwind and the windup shafts. If it is not
straight and square, the tension will not be even across the web and will cause wrinkling.
3. If the web is loose between the unwind and the drive roll, there is not enough tension on the
unwind brake. Increase the tension on the unwind brake to correct.
4. If the web is loose between the windup and the drive roll, there is not enough tension on the
windup clutch. Increase the tension on the windup clutch to correct.
5. If the web gets narrow between the unwind and the drive roll, there is too much tension on
the unwind brake. Decrease the tension on the unwind brake to correct.
6. Top and bottom laminating rolls may not be parallel. Make sure spacer shims are the same
size, then zero the nip. Refer to
Zeroing the Nip
in the maintenance section.
Poor Lamination
1. All substrate materials must be cleaned and free of dust, dirt, grease, and any other type film.
2. Poor lamination is usually caused by thickness variation in the substrate materials such as
plywood, hard board or other such non-precisely made materials. To overcome this, cylinder
spacers may have to be removed and materials laminated without the use of cylinder
spacers, or the next smaller spacer may be used or special spacer utilized.
3. Materials such as Plexiglas or glass sometimes carry a greasy or oily film. These materials
may need to be cleaned with a solvent prior to lamination.
4. Poor lamination can be caused by defective material. To correct this, replace defective
material with higher quality material.
Bubbles in Product
1. Visually inspect materials, mounting or overlays for any voids in the adhesive film. If any
exist, it cannot be corrected by any laminating machine - that part of the material should be
discarded.
2. Low pressure on nip rolls
Increase air pressure to nip rolls.
3. Incorrect shim setting
Adjust shim wheel to correct setting.
4. Nip “zero” setting may be incorrect
Check nip setting and adjust if necessary. Refer to
Zeroing the Nip
in the maintenance section.
Process Control Charts
In order to consistently output high quality product, the operator must have a definite starting point on the
many process variables. This can be achieved by having the operators document system settings when
you have achieved acceptable quality output. The process control chart will allow any operator to set the
machine up for a given process. Keep in mind that the system variables may require adjusting as the
process is being run, but the chart gives an excellent starting point. Factors such as temperature,
humidity, changing film roll diameters all affect the process, therefore, operator technique in running the
machine is inevitable. There is a blank process control chart located on page 4-10, copy this page as
often as needed for new processes.