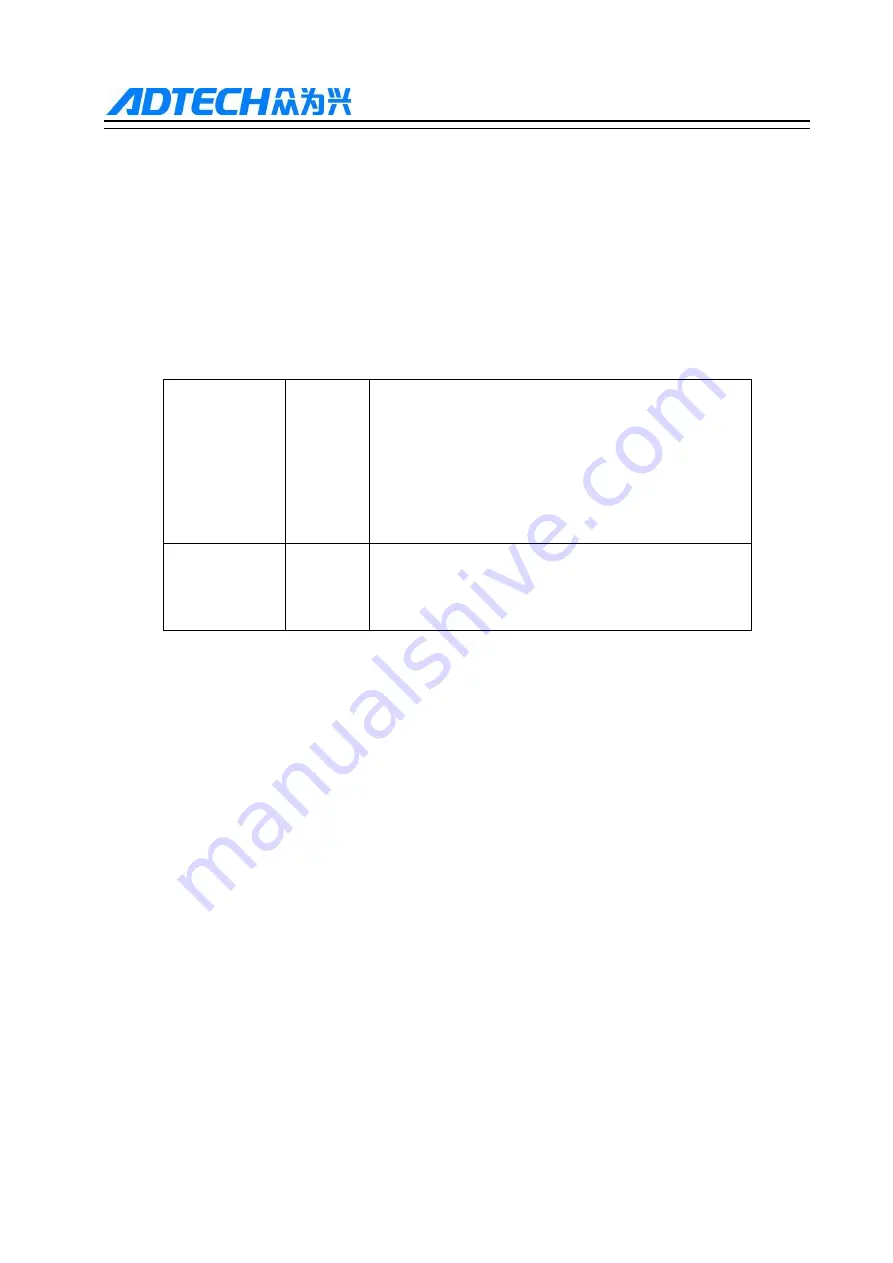
ADTECH9 Series CNC Programming Manual
The working temperature range is between 0
℃
~60
℃
Avoid using it in the environments with high temperature, humidity, dust, or corrosive gas.
Provide rubber rails for buffering in the place with strong vibration.
※
Maintenance
The following items can be conducted for daily and regular inspection, under the general usage conditions
(environmental conditions: daily average temperature: 30
℃
, load-carry duty: 80%, and operational rate: 12
hours per day)
Daily inspection
Daily
Confirm environmental temperature, humidity, dust and
foreign matter;
Check whether there are abnormal vibration and sounds
Check whether vents are blocked by yarns
Regular
inspection
One year
Check whether solid components are loose
Check whether terminal blocks are damaged
Summary of Contents for CNC9640
Page 1: ...ADTECH9 Series CNC Programming Manual ...
Page 21: ...ADTECH9 Series CNC Programming Manual Workpiece Coordinate System Diagram ...
Page 44: ...ADTECH9 Series CNC Programming Manual 2 Occasions that inner corner rotates ...
Page 45: ...ADTECH9 Series CNC Programming Manual ...
Page 62: ...ADTECH9 Series CNC Programming Manual Manual insertion ...
Page 65: ...ADTECH9 Series CNC Programming Manual Tool radius compensation start and axis Z cut in action ...
Page 117: ...ADTECH9 Series CNC Programming Manual ...
Page 118: ...ADTECH9 Series CNC Programming Manual ...
Page 142: ...ADTECH9 Series CNC Programming Manual ...
Page 143: ...ADTECH9 Series CNC Programming Manual ...