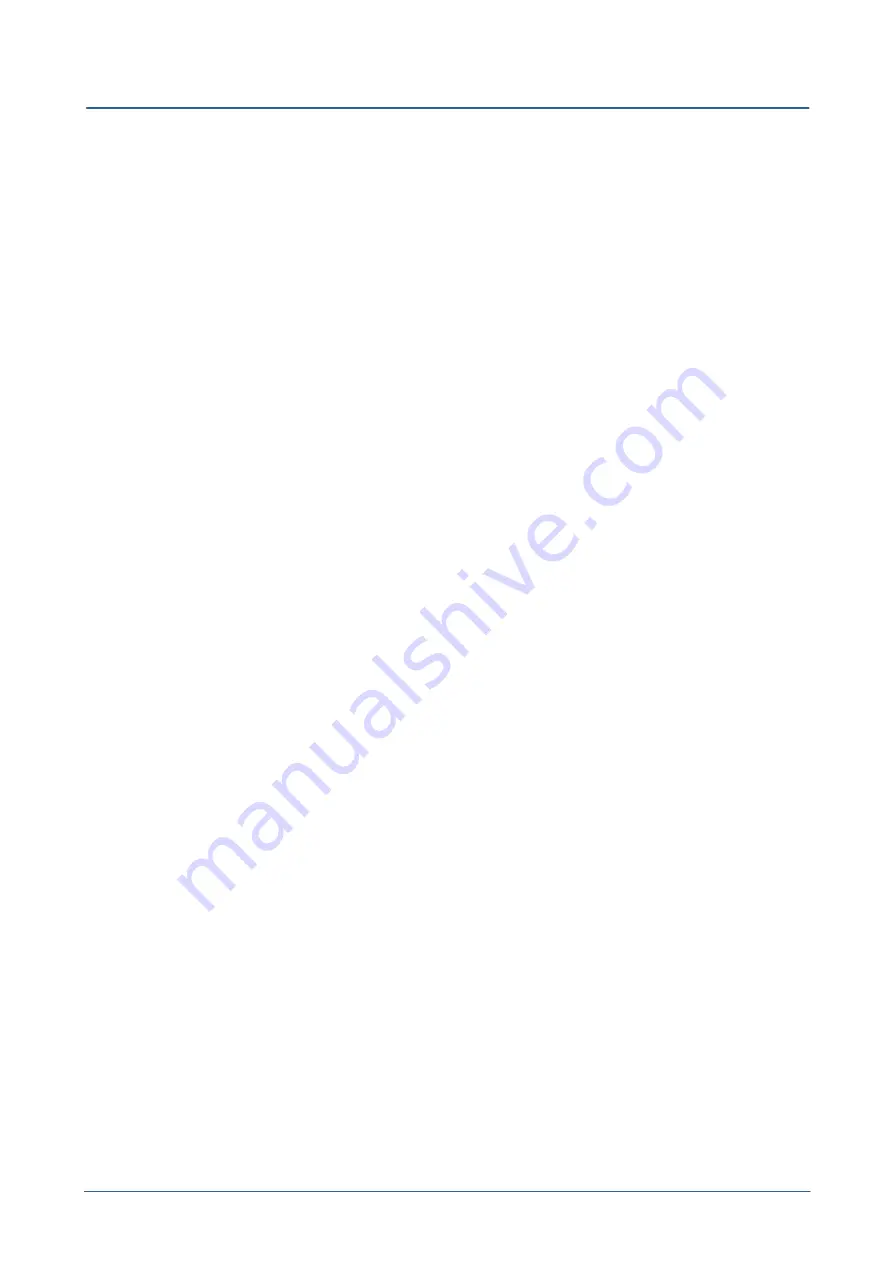
9
A1207 PenGauge
© 2022 Acoustic Control Systems – ACS Group
Operation manual
Operation manual
layer (0.1-0.3 mm). At that, the result of the measurements will include the thickness
value of the paint layer.
If there is a thick layer of paint on the surface or the paint starts to pill off, then remove it
since the thick paint layer reduces the signal and can produce a false echo resulting in
false measurement results.
1.3.2.2
Putting the piezoelectric transducer onto the surface
The piezoelectric transducer should be tightly pressed to the surface of the tested item to
provide a good transmission of the ultrasonic sound into the material.
When measuring the wall thicknesses of the cylindrical objects, minimal diameters, we
recommend using viscous lubricant (viscous contact liquid) and applying more liquid to
the point of contact.
Tightly pressing the piezoelectric transducer to the tube's surface and watching the
instrument's readings, lean the transducer from side to side in the plane perpendicular to
the tube's axis. At that move, the transducer gradually along the tube's wall. Do not slide
along the wall to decrease the wearing of the working surface of the piezoelectric
transducer.
If scanning is required, e.g., when searching for local thin areas of the material, then do it
as gently as possible, do not apply strong pressure, and use clean contact grease only
on the pre-cleaned surface.
The instrument's readings when the transducer is leaning from the middle position will be
increased a little. The minimum steady reading of the instrument contacting the tube’s
wall with the middle of the working surface of the piezoelectric transducer will be
considered the actual value of the measured thickness. If the transducer strongly leans
from this position, then the instrument's readings could increase in discrete steps.
The tested objects with double convex curvature (tubes’ bends, spherical coverings and
so on) are the most difficult for inspection since they can be contacted in a single point
only. If so, the transducer should contact the object in the middle of its working surface.
1.3.2.3
Non-parallelism or eccentricity
If the external and internal surfaces of the inspected material are not parallel or are
eccentric to each other, then the reflected wave (echo – signal) will deviate from the
required direction, and the accuracy of the readings will decrease.
1.3.2.4
Acoustic properties of the material
Some properties of the constructive materials can essentially limit the measurement
accuracy and measurable thickness range, and they can also increase the measurement
error.
1.3.2.4.1 Sound dispersion
In some materials (some types of stainless steel, cast-iron, composites), the sound
energy is being dispersed (on the crystallite molding or additions in the composites). This
effect reduces the possibility of the quality receipt of the signal reflected from the
backside of the tested object, thus limiting the abilities of the ultrasound measurements.
1.3.2.4.2 Variation of velocity
Sound velocity can vary essentially when the sound goes from one point to another in
some materials. This effect in some types of cast stainless steel and copper is caused