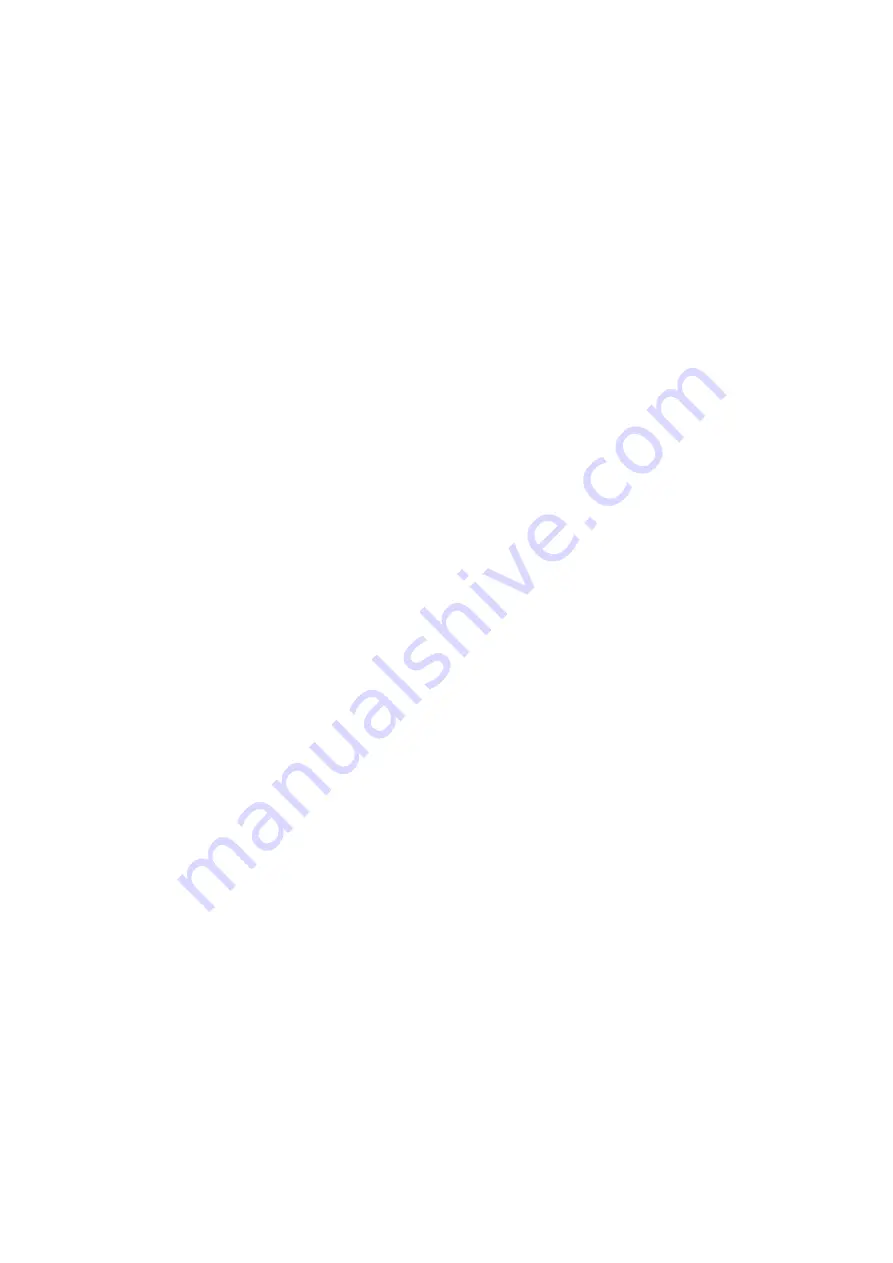
818~2040 PD
___________________________________________________________________________
5-9
5.4 WORKPIECE SIDE SURFACE GRINDING
5.4.1PURPOSE OF WORKPIECE SIDES GRINDING
The top / bottom sides, right / left and front / back sides of flat and rectangular workpieces must be
ground to accurate squareness and parallelism. This means when grinding a big surface to desired size,
its four sides and top / bottom sides must also be ground to be square and parallel. These surfaces will
be used as reference for line marking and boring.
5.4.2
GRINDING
ALLOWANCE
Any surface to be ground requires a proper grinding allowance for grinding out marks of planning
and milling and for grinding to an accurate size. The surface finish and accuracy may vary with different
machining methods, therefore grinding allowance required is different for various machining method. In
general, grinding allowance for each surface should be added by at least 0.25mm, that ensures cutting
marks can be ground out and achieves accurate squareness, parallelism and reference.
5.4.3 PRIORITY OF GRINDING SURFACE
If all surface of a rectangular workpiece need to be ground, performing grinding according to
correct procedures. Normally a large surface should be ground at first, then grinding its parallel surface.
These ground surfaces will be used as reference when grinding side surfaces.
5.4.4 MOUNTING WORKPIECE
A.
Application of angle plate: when grinding workpiece side surfaces and end surfaces, the fastest
and the most convenient mounting method is to apply angle plate for clamping the ground
surfaces for performing grinding operations. This may ensure accurate squareness. If the
workpiece is not so big, two adjacent surfaces can be ground with one setup.
B.
Clamping workpiece by angle plate:
1.
Remove all burrs on the workpiece.
2.
Thoroughly clean the magnetic chuck and the angle plate.
3.
Place a thin paper on the magnetic chuck, which size is slightly bigger than the angle plate.
4.
Place one end of the angle plate on the magnetic chuck, as shown on the left figure on page 5~10. The
number marked on the workpiece is the grinding step.
5.
Place workpiece against angle plate
Place the ground surface against the angle plate, and have one side surface or end surface of
workpiece supported by the magnetic chuck.
Adjust the top side and one side of wrokpiece so that they protrude over the angle plate at least
12.5mm. If the side surface can’t protrude over the top of angle plate, you can insert a parallel block
between the magnetic chuck and the bottom of wrokpiece, as shown on the left figure on page 5~10.
6.
Hold the workpiece against the angle plate, then increase magnetic force of the chuck.
7.
Use a clamp for clamping the workpiece on the angle plate. Make sure the clamp position does not
interfere against grinding motion. Fit a soft aluminum or bronze between the clamp and workpiece,
which will avoid damage to the ground surface when clamping.
8.
Disconnect magnetic force of the chuck. Without change of mounting condition, place the base of
angle plate on the magnetic chuck, shown as left figure below.
9.
Increase magnetic force, and have the clamping plate located at the chuck position.
10.
If necessary, use two additional clamps at the other side of workpiece to avoid displacement during
grinding
.
Summary of Contents for Supra 2040PD
Page 57: ...818 2040PD 3 CHAP 1 CONTROL PANEL OPERATION 1 1 LAYOUT OF CONTROL PANEL ...
Page 58: ...818 2040PD 4 1 2 MAIN DISPLAY AND BUTTON NUMBERS ON CONTROL PANEL ...
Page 59: ...818 2040PD 5 1 3 GRINDING SETTING DISPLAY AND BUTTON NUMBERS ...
Page 75: ...818 2040PD 21 3 5 SCREEN CONTRAST BRIGHTNESS WINDOW ...
Page 82: ...818 2040PD 28 4 5 SYSTEM PARAMETER Enter from 4 5 1 OPERATOR ...
Page 83: ...818 2040PD 29 SYSTEM MAINTENANCE PERSONNEL ...
Page 84: ...818 2040PD 30 4 5 2 SETTING PASSWORD TABLE ...
Page 85: ...818 2040PD 31 4 5 3 SYSTEM DATE TIME ...
Page 86: ...818 2040PD 32 4 5 4 ADJUSTING CONTRAST BRIGHTNESS ...
Page 91: ...818 2040PD 37 5 2 10 SYSTEM DATA SETTING KEEP SET SYSTEM DISPLAY ...
Page 178: ...1020 PD 1224 PD LUBRICATION SYSTEM 258 PL 16 ...
Page 183: ...14 16 PD SPINDLE PL 01 ...
Page 185: ...14 16 PD COLUMN 3821 3821H 14SERIES 4821 4821H 16SERIES PL 02 ...
Page 187: ...14 16 TD WHEEL GUARD WHEEL FLANGE PL 04 ...
Page 208: ...14 16PD LONGITUDINAL HYDRAULIC SYSTEM PL 10 ...
Page 222: ...14 16 PD LUBRICATION SYSTEM 368 PL 15 ...
Page 225: ...ACER Taiwan ...
Page 226: ...ACER Taiwan ...
Page 227: ...ACER Taiwan ...
Page 228: ...ACER Taiwan ...
Page 229: ...ACER Taiwan ...
Page 230: ...ACER Taiwan ...
Page 231: ...ACER Taiwan ...
Page 232: ...ACER Taiwan ...
Page 233: ...ACER Taiwan ...
Page 234: ...ACER Taiwan ...
Page 235: ...ACER Taiwan ...
Page 236: ...ACER Taiwan ...
Page 237: ...ACER Taiwan ...
Page 238: ...ACER Taiwan ...