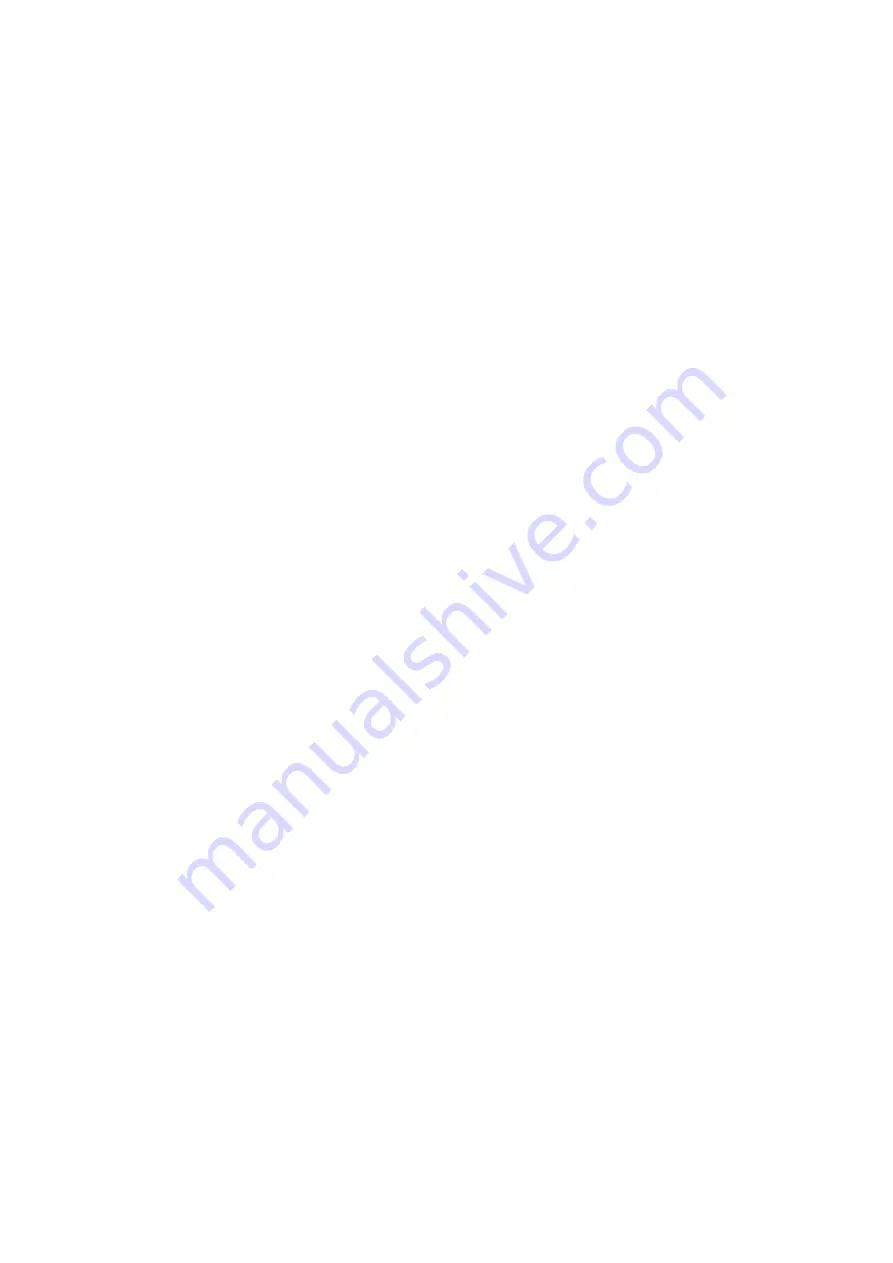
818~2040 PD
___________________________________________________________________________
5-13
5.5.5 VERTICAL SURFACE GRINDING PROCEDURES
A. Install a grinding wheel especially suitable for vertical surface grinding. You also need to balance, shape and
sharpen the grinding wheel.
B. Mount a diamond dresser on the magnetic chuck. Cut the grinding wheel side at 1.5mm position from the
circumference toward the flange into a concave shape. Its height should be over the surface to be ground.
C. Remove all burrs on the workpiece.
D. Clean the magnetic chuck, and then mount the workpiece. Place a sheet of thin paper between the workpiece
and chuck.
E. Calibrate parallelism between the workpiece surface and table.
a. Apply a dial gauge for calibration. If workpiece is too small, place metallic pieces or parallel plates around
the workpiece to fix, which may avoid workpiece displacement when grinding.
b. Calibrate stop bar on the magnetic chuck, and hold the workpiece against the stop bar or parallel plate.
F. Increase magnetic force. Check if the workpiece is held securely, then check if parallelism calibration made with
above procedure is proper or not.
G. Adjust the table reversing dog position, so that the workpiece travel is over 25mm at each end.
H. Start the grinding wheel running. Move workpiece to approach the concave side of the grinding wheel.
I.
Lower the grinding wheel to a 0.075mm position above the surface.
J. Move table slowly. Feed workpiece to just touches the grinding wheel and sparks occur.
K. Perform coarse grinding on the vertical surface until a 0.05mm allowance before the final size is obtained.
Perform cross feed of table with 0.0125mm at each pass.
L. If required, use a strip dresser to slightly dress the side of grinding wheel.
M. Perform fine grinding until your desired size is achieved. The table feed amount per pass is about
0.0025~0.0075mm.
N. Before removing workpiece from the chuck, you should check the grinding size again.
5.6 ANGULAR SURFACE GRINDING
5.6.1 ANGULAR SURFACE GRINDING METHODS
There are two grinding methods usually applied for angular surface grinding:
●
Install the workpiece at an angular position as your desired angle. Apply the straight face of a straight
grinding wheel for grinding.
●
Install the workpiece in a flat condition. Dress a grinding wheel to the desired angle for angular surface
grinding.
5.6.2 MOUNTING WORKPIECE TO A DESIRED ANGLE
Workpiece can be mounted according to its shape and your desired angle, which can be
clamped by various devices, such as angle plate, sine chuck, adjustable angle plate and
adjustable angular vise, etc.
A.
Apply a sine bar and block for mounting workpiece on an angle plate: This method allows workpiece to
be quickly adjusted to your desired angle on the angle plate.
a. CONSTRUCTION OF SINE BAR: The sine bar consists of strip block and two rollers with same
diameter on the base. The two rollers are manufactured from hardened steel, precision ground and
polished. The distance between two rollers is normally 125mm. The strip block is manufactured from
tool steel, hardened, precision ground and polished for high accuracy. Any angle can be adjusted by
placing a block under the roller at one end of strip block. The sine bar and block must be used on a flat
enough plate.
b. PRINCIPLE OF SINE BAR: The strip block of the sine bar represents the hypotemus of a right
triangle. The block forms the opposite side of the desired angle. The plate serves as the base of a
Summary of Contents for Supra 2040PD
Page 57: ...818 2040PD 3 CHAP 1 CONTROL PANEL OPERATION 1 1 LAYOUT OF CONTROL PANEL ...
Page 58: ...818 2040PD 4 1 2 MAIN DISPLAY AND BUTTON NUMBERS ON CONTROL PANEL ...
Page 59: ...818 2040PD 5 1 3 GRINDING SETTING DISPLAY AND BUTTON NUMBERS ...
Page 75: ...818 2040PD 21 3 5 SCREEN CONTRAST BRIGHTNESS WINDOW ...
Page 82: ...818 2040PD 28 4 5 SYSTEM PARAMETER Enter from 4 5 1 OPERATOR ...
Page 83: ...818 2040PD 29 SYSTEM MAINTENANCE PERSONNEL ...
Page 84: ...818 2040PD 30 4 5 2 SETTING PASSWORD TABLE ...
Page 85: ...818 2040PD 31 4 5 3 SYSTEM DATE TIME ...
Page 86: ...818 2040PD 32 4 5 4 ADJUSTING CONTRAST BRIGHTNESS ...
Page 91: ...818 2040PD 37 5 2 10 SYSTEM DATA SETTING KEEP SET SYSTEM DISPLAY ...
Page 178: ...1020 PD 1224 PD LUBRICATION SYSTEM 258 PL 16 ...
Page 183: ...14 16 PD SPINDLE PL 01 ...
Page 185: ...14 16 PD COLUMN 3821 3821H 14SERIES 4821 4821H 16SERIES PL 02 ...
Page 187: ...14 16 TD WHEEL GUARD WHEEL FLANGE PL 04 ...
Page 208: ...14 16PD LONGITUDINAL HYDRAULIC SYSTEM PL 10 ...
Page 222: ...14 16 PD LUBRICATION SYSTEM 368 PL 15 ...
Page 225: ...ACER Taiwan ...
Page 226: ...ACER Taiwan ...
Page 227: ...ACER Taiwan ...
Page 228: ...ACER Taiwan ...
Page 229: ...ACER Taiwan ...
Page 230: ...ACER Taiwan ...
Page 231: ...ACER Taiwan ...
Page 232: ...ACER Taiwan ...
Page 233: ...ACER Taiwan ...
Page 234: ...ACER Taiwan ...
Page 235: ...ACER Taiwan ...
Page 236: ...ACER Taiwan ...
Page 237: ...ACER Taiwan ...
Page 238: ...ACER Taiwan ...