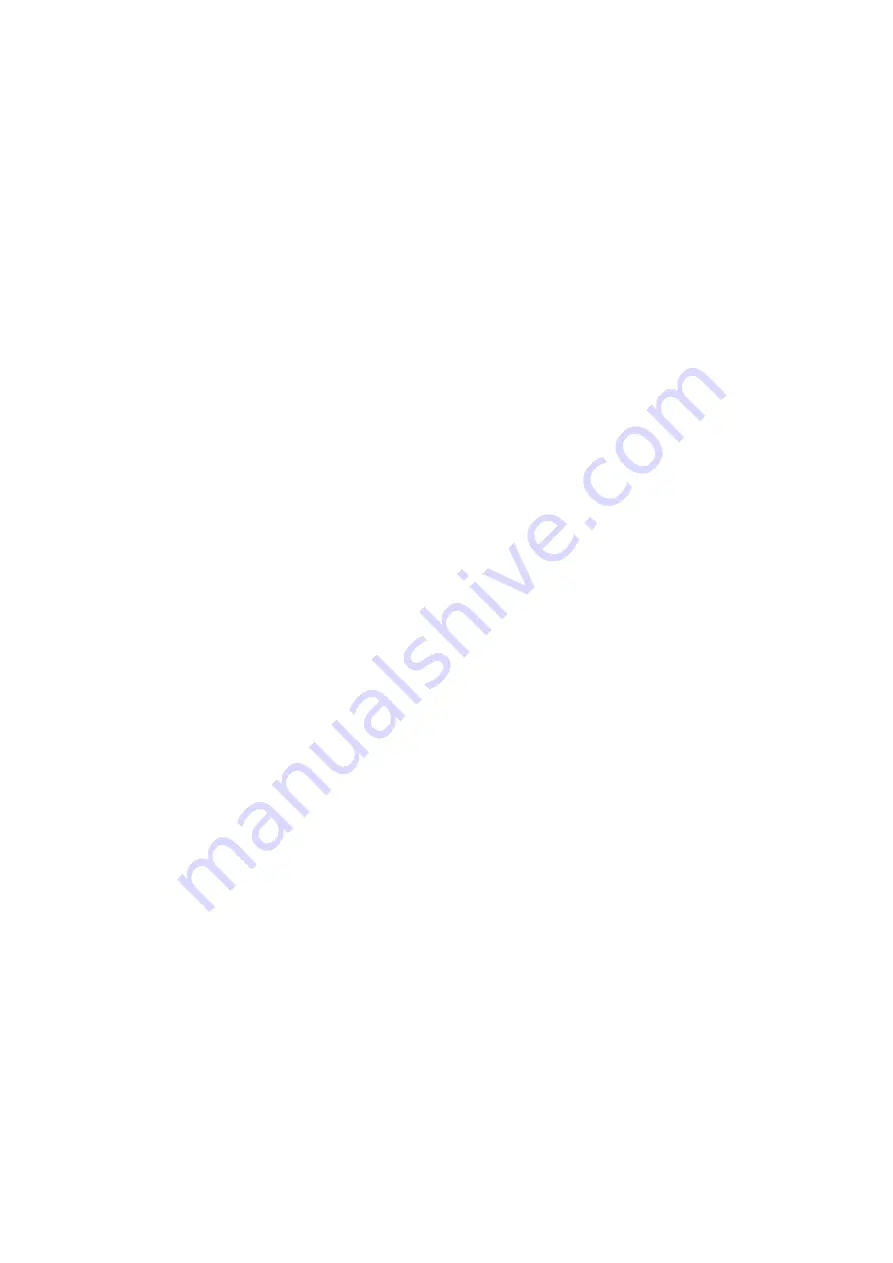
818~2040 PD
___________________________________________________________________________
5-8
Q. Perform several times of coarse grinding as desired. Grind out complete cutting marking until size
approaches to your desired value.
R. Fine sharpening on the grinding wheel.
S. Apply a dressing strip to slightly chamfer both sides of the grinding wheel, that reduces grinding wheel feed
lines on the workpiece.
T. Lower the grinding wheel until it just touches the workpiece surface and slight sparks occur. Then lower the
grinding wheel again by 0.0125~0.025mm to perform fine grinding.
U. Properly adjust the table cross feed speed to obtain the finish as you desired.
V. Perform
fine
grinding.
W. Under the condition of without adjustment of downfeed, perform final cross feed grinding by reversing the
cross feed direction until sparks disappear. Also, make sure the grinding wheel leaves away the workpiece.
X. Close coolant, and then stop table movement.
Y. Keep grinding wheel running about half minute to completely remove coolant from the grinding wheel. Then
stop the machine.
Z. If only one surface grinding is required, release the magnetic chuck. Raise one side of the workpiece to
release magnetism, then remove the workpiece to avoid damage to the chuck surface. If you need to grind
the opposite side of workpiece, perform parallel surface grinding to your desired size, according to following
procedures.
5.3.2 PARALLEL SURFACE GRINDING ON A WORKPIECE
After the first surface grinding has been finished, you may use this surface as a
reference plane for grinding the parallel surface. If the grinding machine condition is
unchanged, the parallel surface can be fast and accurately ground to your desired size.
Grinding procedures are shown as below:
A.
After the first surface of workpiece grinding has been finished, turn the cross feed handwheel to move the
table away from the grinding wheel. Do not change the positions of the wheel head and the table reversing
dog.
B.
Apply a pencil to mark each side position of the morkpiece on the side of the magnetic chuck.
C.
Lift the workpiece on the magnetic chuck for removing all burrs.
D.
Thoroughly clean the magnetic chuck and workpiece.
E.
Measure the workpiece thickness, and determine the material removal amount.
F.
Place a thin paper on the magnetic chuck, and make sure the paper thickness is same as that for the first
surface grinding. .
G.
Place the workpiece on the magnetic chuck between the lines marked by the pencil, then increase magnetic
force.
H.
When the first surface has been ground and the wheel head position is unchanged, then the grinding wheel
can perform coarse grinding.
I.
Perform coarse grinding until the workpiece size approaches a tolerance of 0.025mm or 0.05mm to the final
size.
J.
Sharpen the grinding wheel.
K.
Perform slight grinding on the workpiece.
L.
Remove workpiece from the chuck, and then measure its thickness.
M.
Clean the chuck and workpiece. Mount the workpiece on the chuck again.
N.
Lower the wheel head to perform grinding until your desired size is obtained.
Summary of Contents for Supra 2040PD
Page 57: ...818 2040PD 3 CHAP 1 CONTROL PANEL OPERATION 1 1 LAYOUT OF CONTROL PANEL ...
Page 58: ...818 2040PD 4 1 2 MAIN DISPLAY AND BUTTON NUMBERS ON CONTROL PANEL ...
Page 59: ...818 2040PD 5 1 3 GRINDING SETTING DISPLAY AND BUTTON NUMBERS ...
Page 75: ...818 2040PD 21 3 5 SCREEN CONTRAST BRIGHTNESS WINDOW ...
Page 82: ...818 2040PD 28 4 5 SYSTEM PARAMETER Enter from 4 5 1 OPERATOR ...
Page 83: ...818 2040PD 29 SYSTEM MAINTENANCE PERSONNEL ...
Page 84: ...818 2040PD 30 4 5 2 SETTING PASSWORD TABLE ...
Page 85: ...818 2040PD 31 4 5 3 SYSTEM DATE TIME ...
Page 86: ...818 2040PD 32 4 5 4 ADJUSTING CONTRAST BRIGHTNESS ...
Page 91: ...818 2040PD 37 5 2 10 SYSTEM DATA SETTING KEEP SET SYSTEM DISPLAY ...
Page 178: ...1020 PD 1224 PD LUBRICATION SYSTEM 258 PL 16 ...
Page 183: ...14 16 PD SPINDLE PL 01 ...
Page 185: ...14 16 PD COLUMN 3821 3821H 14SERIES 4821 4821H 16SERIES PL 02 ...
Page 187: ...14 16 TD WHEEL GUARD WHEEL FLANGE PL 04 ...
Page 208: ...14 16PD LONGITUDINAL HYDRAULIC SYSTEM PL 10 ...
Page 222: ...14 16 PD LUBRICATION SYSTEM 368 PL 15 ...
Page 225: ...ACER Taiwan ...
Page 226: ...ACER Taiwan ...
Page 227: ...ACER Taiwan ...
Page 228: ...ACER Taiwan ...
Page 229: ...ACER Taiwan ...
Page 230: ...ACER Taiwan ...
Page 231: ...ACER Taiwan ...
Page 232: ...ACER Taiwan ...
Page 233: ...ACER Taiwan ...
Page 234: ...ACER Taiwan ...
Page 235: ...ACER Taiwan ...
Page 236: ...ACER Taiwan ...
Page 237: ...ACER Taiwan ...
Page 238: ...ACER Taiwan ...