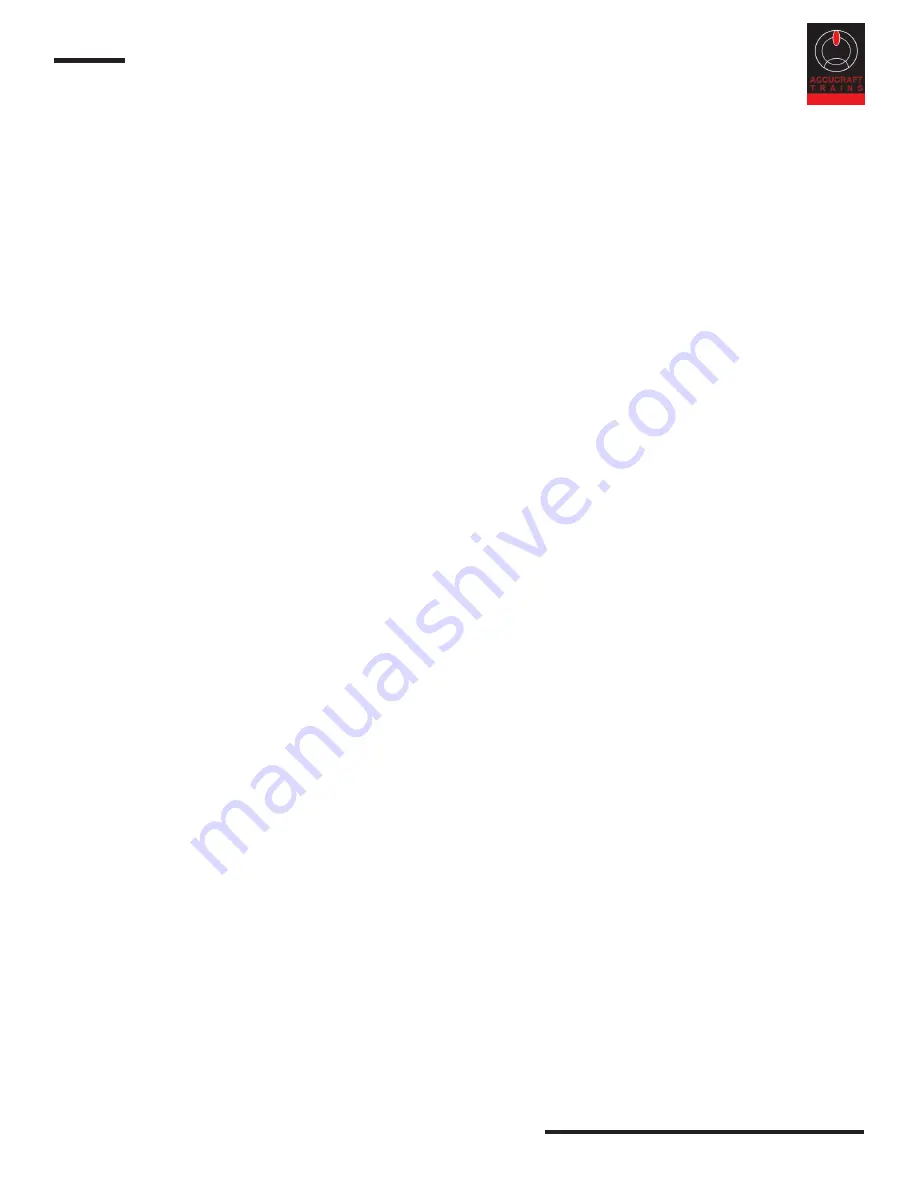
D&RGW K-28 COAL FIRED MANUAL
3
STEAM OIL
Your coal fired conversion contains an adjustable feed lubricator with the feed line separate from the main steam
line. This allows you to adjust the feed rate to provide adequate oil to the cylinders without creating an excess of
oil soaked residue of cinder and ash in the smoke box. A heavy grade of steam oil will work best in this capacity.
The best oil to use for your K-28 conversion is an ISO 460 AGAMA 7 compounded steam cylinder oil. We have
been using oil that meets this criteria that was purchased from an Accucraft dealer, but Sulphur Springs Steam
Models has a comparable oil. ISO 460 AGAMA 7 compounded cylinder oils are also available from your local
petroleum bulk dealer. This is a darn, thick oil that allows easy adjustment of the lubricator. Flow rate of this oil
should be adjusted to provide about 1 to 1.5 cc per hour of running time . On our locomotive this flow rate results
from opening the needle valve between 1/8 and 1/4 of a turn from closed.
LUBRICATOR SYRINGE
The best way to adjust your lubricator is by measuring the condensed water remaining after a run. Your lubricator
is fitted with a drain to use for removing the condensate at the end of a run, but this makes measuring it difficult.
The best way to accomplish this is by using a syringe with an 1/8 inch tube to draw out the water from the bottom
of the lubricator. This allows you to adjust the feed rate to provide adequate oil to the cylinders. The amount of
water should approximate 1 to 1.5 cc per hour of running. A very nice brass syringe is available from Accucraft.
Sku# AP-29201.
LUBRICATING OIL
Because of the additional loads imposed on the running gear by the axle pump, we recommend OIL the use of
STRAIGHT 40 WEIGHT, automotive lubricating oil for your locomotive. Lubrication of all moving parts prior to
each run is highly recommended , with special attention to the eccentric, ram and driving yoke of the axle pump.
AFTER RUN
BRUSHING
To clean off the light dusting of ash and cinders following a run we use a 1 1/2 to 2 inch wide, soft bristle paint
brush. Since a proper adjustment of the lubricator results in little to no oil splatter on the locomotive, the brush
down will almost completely remove all dust, cinders and ash.
CLEANING
SOLVENT
The running gear of your locomotive needs regular cleaning, We use and recommend the use of “STODDARD”
solvent for this purpose. This is a product that is designed for parts washing in the aviation and automotive indus-
try. It is an excellent grease and oil remover, has a low flammability and leaves only films or residue. It is available
from your local Petroleum Bulk Supplier, either under the name of “Stoddard” solvent or as parts washing fiJid.
Most automotive machine shops can point you in the right direction to buy it.
SOLVENT
SPRAYER
We apply the Stoddard solvent using a pressure type garden sprayer. Ours is a HUDSON brand “Bugwiser
Sprayer,” model number 67220. This has a 2 gallon, stainless steel, canister, which is solvent resistant. We pur-
chased ours from LOWES’ HOME CENTER. One note about this sprayer and Stoddard Solvent. You will have to
occasionally put some oil down the top of the sprayers pump barrel to lubricate the piston, as the solvent tends to
wash away the pumps lubricant.
VACUUM
CLEANER
One of the components of all coal is sulphur. Sulphur burns producing sulphur dioxide, which combines with mois-
ture to form sulfuric acid. To reduce the corrosive effects of sulfuric acid you should clean all of the accumulated
ash and cinders out of the smoke box following every run . This can be accomplished using a computer vacuum
. The specific brand we use is a Metropolitan Metro DataVac w/Micro-Tools. Ours was bought from a Fry Elec
-
tronics store, but they are available from various computer and electronic supply stores, and on line from Office
Quarters. Their website is : www.officequarters.com