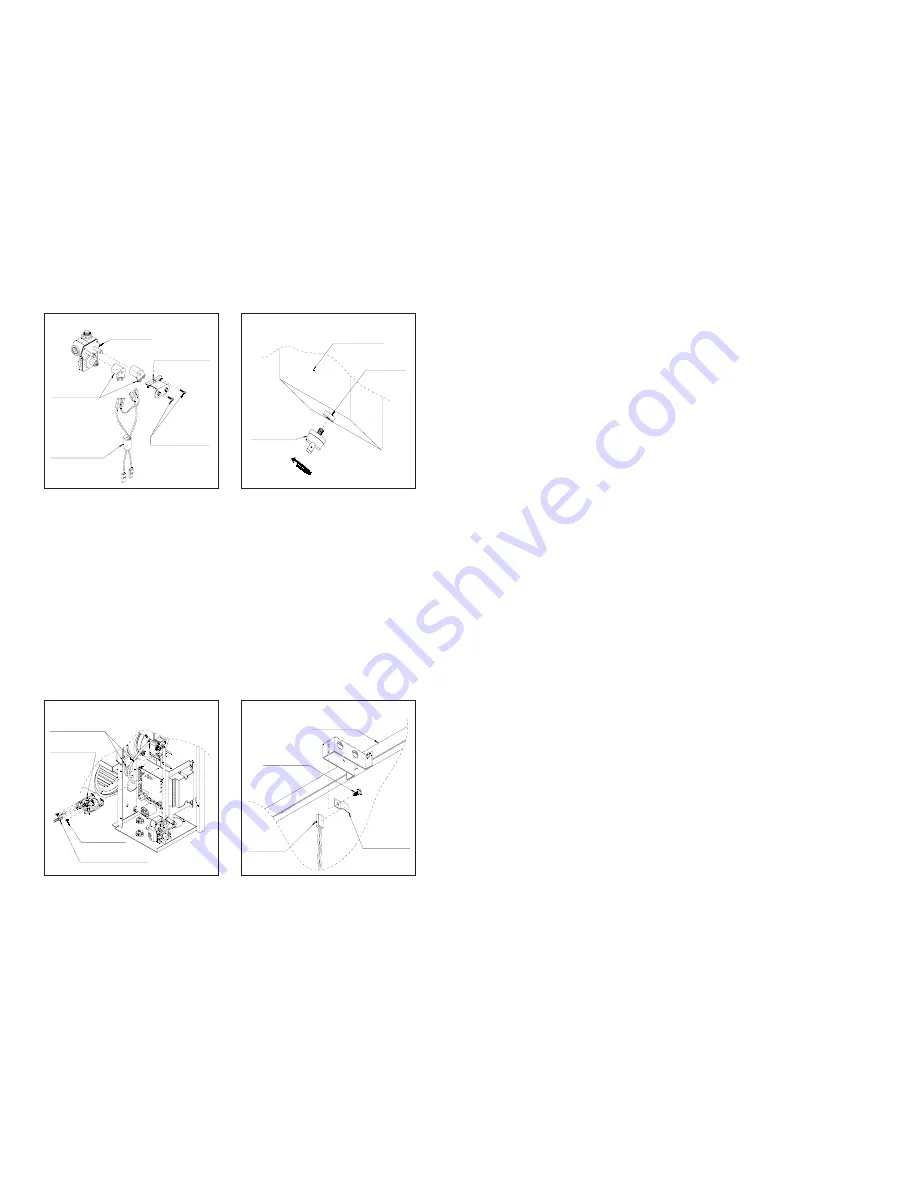
page 5
The fan takes in the room air which is then heated
as it passes through the heat exchanger. The
warm air is discharged directly into the environment
through the grille located at the top or front of the
appliance.
Fan operation is controlled by a thermostat: to
prevent cold air from entering the environment.
The fan begins operating shortly after the burner
has ignited. The fan runs for a short time after the
burner is extinguished, to allow the exchanger to
cool off gradually.
If the air filter becomes blocked or if the fan does
not turn on or function correctly, and as a
consequence the exchanger overheats, a safety
device will be triggered that will cut off the gas
flow to the burner. This shutdown condition will
also be indicated on the control panel.
The combustion products are exhausted outdoors
by a centrifugal fan whose correct functioning is
controlled by a differential pressure switch. The
fan is located after the sealed combustion circuit.
The combustion circuit’s pressure is always lower
than the room’s air pressure, thus providing an
additional safety feature.
Air heater operation is controlled by the electronic
room thermostat on the remote-control panel
and by an optional programmable timer that is
installed separately.
1.4 CONSTRUCTION CHARACTERISTICS
The casing is built with epoxy-powder painted
metal plate which guarantees its durability. In
the WD versions with ducts the casing is built
with galvanized metal plate and has removable
inspection panels.
The air delivery side (in the W and WR versions)
has a grille with painted aluminum blades which
can be individually oriented to permit you to
direct the air flow where you want in the room.
The blades are attached to supports made of
heat-resistant plastic. They rotate by means of
an exclusive friction system on silicone guides.
There is a small door to the side of the grille
which, in the W version for installation on the
wall, protects the access to the control panel.
This is especially useful when the unit is installed
in public places, because it prevents the controls
from being set to undesired positions, for
example, by children (the small door is not used
in the ceiling version since the remote-control
panel is installed on the wall).
In the WD versions with ducts the grille and the
adjustable blades have been replaced by an air
outlet that is designed to have ducts attached to
it. Also the air intake side has been designed to
have ducts attached to it.
The air intake side (in the W and WR versions)
houses a filter made of regenerable synthetic
material in a metal frame which can be removed
for cleaning.
The following are installed inside the unit:
- The heat exchanger unit with gas burner.
This module, which was developed using
patented technical solutions, is made of
stainless steel. It is basically made up of a pair
of finned tubes which exchange heat very
efficiently and a combustion chamber which
houses an atmospheric burner which generates
an axial flame. The combustion products are
exhausted outdoors by a centrifugal fan.
- The ventilation unit, which is made up of two
centrifugal fans with double intake. They have
a high air capacity and a low noise level. They
are activated by an electric motor whose
rotation speed is controlled from the control
panel. The unit is mounted on a galvanized
steel support.
- The set of control devices, which includes:
- Burner control unit with electronic ionization
flame detection.
- Gas solenoid valve with a double closing
device and a pressure regulator.
- Differential pressure switch for controlling
that the combustion products are exhausted
properly.
- Fan control thermostat.
- Safety thermostat.
- The control panel (operated by remote
control in the WR and WD versions). It is
able to control the room temperature by means
of a built-in probe and to indicate the
functioning status or any problems with the
unit. It also allows you to select one of its two
ventilation speeds.
1.5 PACKAGE CONTENTS
The unit is shipped in two separate packages:
a) The unit: The air heater is shipped with
cardboard packing and polystyrene foam
protection corners and sheets. For the W
version, for installation on the wall, the
electronic control panel is already installed
on the unit. Instead, for the WR and WD
versions for installation on the ceiling, the
control panel is already connected to the unit
with four meters of cable; the accessories for
page 32
8.4 DIFFERENTIAL PRESSURE SWITCH
Disconnect the electrical connection and the
silicone tubes. Unscrew the screws and remove
the pressure switch. Install the new pressure
switch (which has been calibrated specifically for
your air heater model) and re-establish the
connections, making sure that you place the
contacts in their proper positions. Put the silicone
tube back in place (fig. 27).
8.5 CONVECTION FAN CONTROL
THERMOSTAT
Disconnect the cables and unscrew the
thermostat from the threaded support. Insert the
new thermostat, screwing it all the way in by
hand (do not use tools which might damage the
thermostat). Make sure that the distance between
the thermostat enclosure and the threaded
support is not greater than 3 mm, to guarantee
that the sensor remains in contact with the wall
of the exchanger. Re-establish the electrical
connection (fig. 28).
8.6 SAFETY LIMIT THERMOSTAT
Disconnect the electric connection of the
thermostat on the terminal board. Release the
thermostat by disassembling the attachment
plate from the support. Mount the new thermostat
by reversing the order of the previous operations.
Make sure to insert the side of the thermostat
with the printed data facing the air heater shield
(fig. 29).
Fig. 28
CHANGING THE FAN THERMOSTAT
Exchanger
Threaded
support
Thermostat
Unscrew
Fig. 27
CHANGING THE PRESSURE SWITCH
Silicone tubes
Pressure switch
Screws
Electrical connection
Fig. 29
CHANGING THE SAFETY THERMOSTAT
Back plate
Thermostat
Screw
Attachment
plate
Fig. 26
CHANGING THE GAS UNIT’S COIL
Coil support
Gas unit
Screws
Solenoid
valve coils
Valve rectifier
bridge
Summary of Contents for W
Page 2: ......