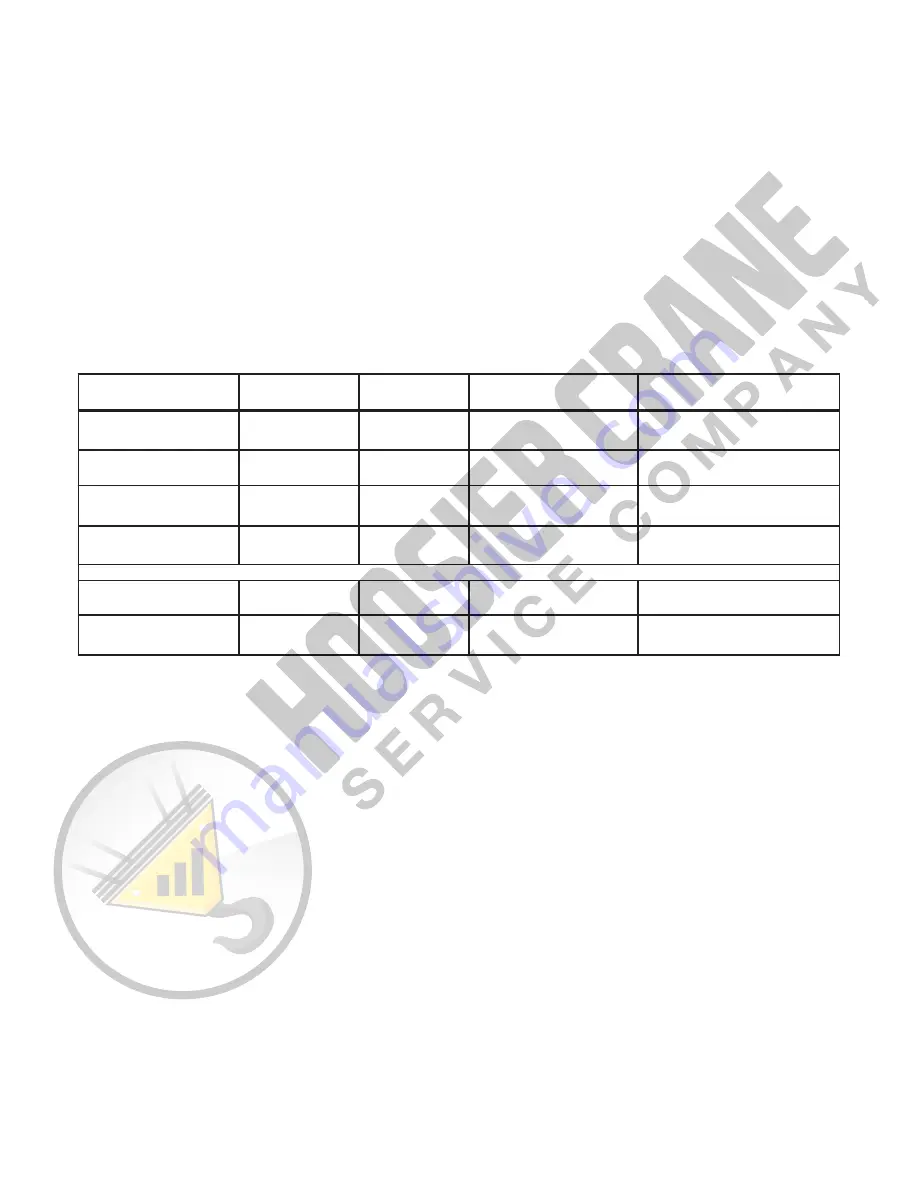
4
NOTE:
Do not mix oils from different manufacturers. If a change to another type or brand of oil is made, the existing lubricant should be
drained and the gearcase flushed with a small quantity of the new lubricant before refilling with the new lubricant. This is necessary to
avoid possible incompatibility problems between the two lubricants. The list below gives approved alternative lubricants. This is not an
exclusive list. Equivalent lubricants from other manufacturers may be used.
All reducers are factory filled according to the mounting position indicated on the order.
If the mounting position is changed from
the ordered mounting the position, the oil level must be changed.
The oil volumes shown in the mounting position charts are
approximate. The correct oil level is determined by the oil level hole in the housing except for size 38 reducers. If the reducer is ordered
with the standard mineral oil and the oil is later changed to synthetic oil, it is recommended the shaft seals be changed to Viton (FKM)
material.
ILH is furnished with oil level, drain, and fill plugs except for the size 38, which only has a fill plug. Before starting operation, the breather
must be located in the correct location.
Continued operation in cold ambient conditions requires special modifications. Contact DODGE Gearing Application Engineering,
Greenville, SC for application assistance (864-284-5700).
The density of the standard factory fill oil is 0.93 lbs/pint (1.98 lbs/liter).
The list below shows lubricants that are available as factory fill in QUANTIS reducers. The standard factory fill lubricant is Mobilgear 600
XP 220, which is a high performance mineral oil lubricant with special additives for use in industrial gear products.
Table 2 - Lubricant Selection Table
Ambient
Temperature*
Oil Type
ISO
Viscosity Grade
Available Oils
Available Food Grade Oils (NSF H1)
10°F to 105°F
(-12°C to 41°C)
Mineral Oil
220
Mobilgear 600 XP 220
(standard factory fill **)
-
-20°F to 50°F
(-29°C to 13°C)
Synthetic Oil
68
Mobil SHC 626
-
-10°F to 115°F
(-23°C to 46°C)
Synthetic Oil
220
Mobil SHC 630
-
30°F to 140°F
(-0° C to 60° C)
Synthetic Oil
460
Mobil SHC 634
-
25°F to 75°F
(-4°C to 29°C)
Mineral Oil
220
-
Chevron FM 220
45°F to 105°F
(7°C to 41°C)
Mineral Oil
460
-
Chevron FM 460
*
Ambient temperatures listed are for lubricant only and do not indicate a particular gear unit’s suitability to run in that ambient.
**
Previous factory fill oil was Mobilgear 630 - Mobilgear 600 XP 220 and Mobilgear 630 are compatible with each other and do not
require a flush.
Recommendations will be made based on specific application details.
LONG TERM STORAGE:
NOTE:
Unless an extended warranty has been negotiated prior
to sale, time in storage is considered time in service for warranty
purposes.
If the drive is not installed immediately, it should be stored in a
clean, dry, protected area. During periods of long term storage
(six months or longer) special procedures must be followed. The
unit should be filled to the highest oil level hole with an approved
lubricant blended with 2%, by volume, of “Daubert Chemical Co.
Nox-Rust VCI-105” oil. Apply a thick coating of rust preventative
on all unpainted surfaces including threads, bores, keyways,
and shafts. Apply a thick coating of chassis-type grease to all
exposed shaft seals. If the unit is to be stored outdoors or in a
damp, unheated area indoors, cover the entire exterior with a
rust preventative. Seal the unit in a moisture proof container or
wrapping with a desiccant inside. Shade the enclosure from direct
sunlight. Rotate the input shaft at least 60 revolutions once a month
to redistribute the lubricant and prevent brinnelling of bearings and
drying of seals.
Upon removal from storage, remove all protective coatings applied
for protection during storage. Check all hardware for proper
tightness. Drain and refill the gear reducer with a recommended
lubricant. If the gear reducer has been stored for more than three
years or in an area with high ambient temperatures, replace the
oil seals.
Summary of Contents for LOUDEN 200 Series
Page 1: ......
Page 2: ......
Page 3: ......
Page 4: ......
Page 5: ......
Page 6: ......
Page 7: ......
Page 8: ......
Page 9: ...FIGURE 8 FIGURE 9 FIGURE 10 FIGURE 11...
Page 10: ......
Page 11: ......
Page 12: ......
Page 13: ......
Page 14: ......
Page 15: ......
Page 16: ......
Page 17: ......
Page 18: ......
Page 19: ......
Page 20: ......
Page 21: ......
Page 22: ......
Page 23: ......
Page 24: ......
Page 25: ......
Page 26: ......
Page 27: ......
Page 28: ......
Page 29: ......
Page 30: ......
Page 31: ......
Page 32: ......
Page 33: ......
Page 34: ......
Page 35: ......
Page 36: ......
Page 37: ......
Page 38: ......
Page 39: ......
Page 40: ......
Page 41: ......
Page 42: ......
Page 43: ......
Page 44: ......
Page 45: ......
Page 46: ......
Page 47: ......
Page 48: ......
Page 49: ......
Page 50: ......
Page 51: ......
Page 52: ......
Page 53: ......
Page 54: ......
Page 55: ......
Page 56: ......
Page 57: ......
Page 58: ......
Page 59: ......
Page 60: ......
Page 61: ......
Page 62: ......
Page 63: ......
Page 64: ......
Page 65: ......
Page 66: ......
Page 67: ......
Page 68: ......
Page 69: ......
Page 70: ......
Page 71: ......
Page 72: ......
Page 73: ......
Page 74: ......
Page 75: ......
Page 76: ......
Page 77: ......
Page 78: ......
Page 79: ......
Page 80: ......
Page 81: ......
Page 82: ......
Page 83: ......
Page 84: ......
Page 85: ......
Page 86: ......
Page 87: ......
Page 88: ......
Page 89: ......
Page 90: ......
Page 91: ......
Page 92: ......
Page 93: ......
Page 94: ......
Page 95: ......
Page 96: ......
Page 97: ......
Page 98: ......
Page 99: ......
Page 100: ......
Page 101: ......
Page 102: ......
Page 103: ......
Page 104: ......
Page 105: ......
Page 106: ......
Page 107: ......
Page 108: ......