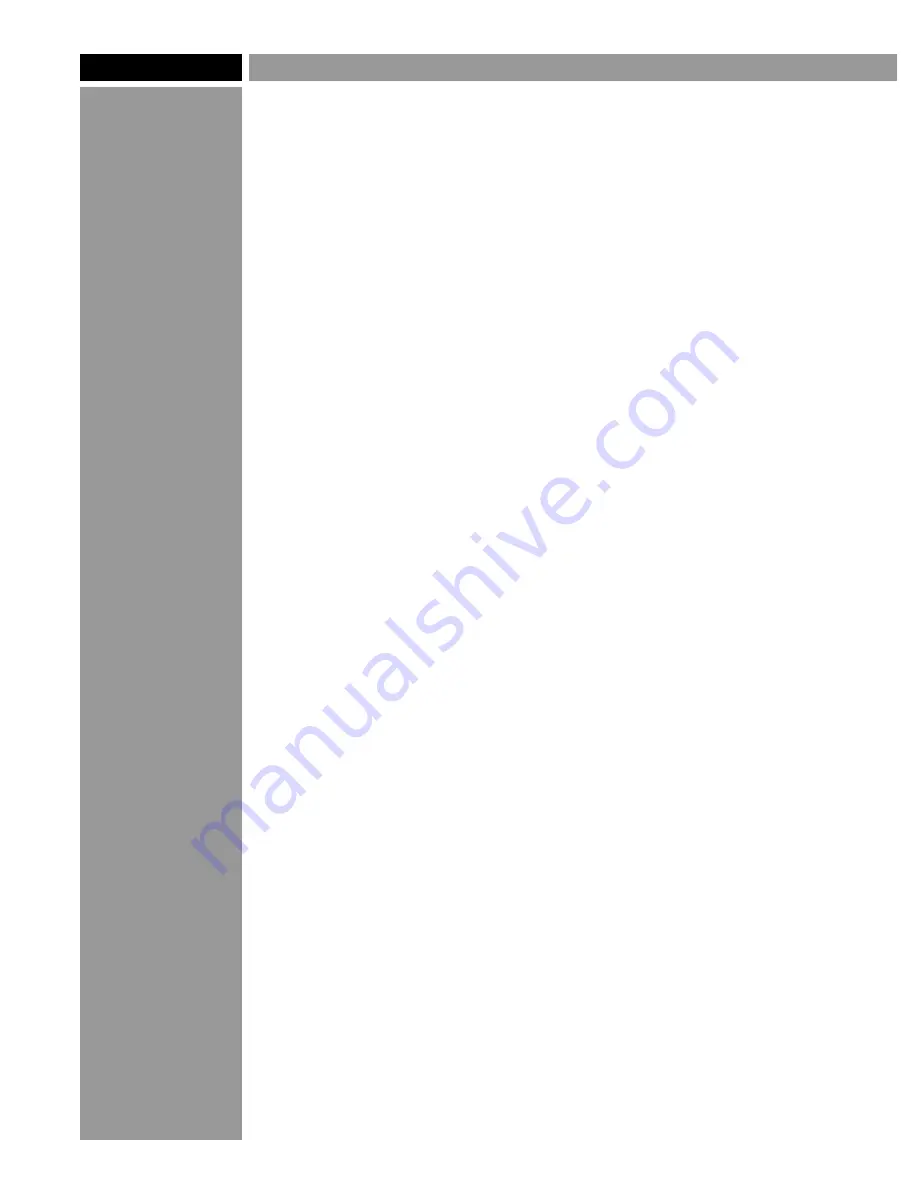
If you have difficulty drilling holes or inserting Rasters™:
1. Re-read the instructions, paying special attention to any specific notes for
specific types of material. Double-check all your settings, both on the
machine and in the engraving software.
2. If the Rasters™ are difficult to insert, or do not stay in the holes, the fault
usually lies with the dimensions of the holes. Try drilling the holes deeper; it
that doesn't work, see page 6 for information on balancing the cutter.
3. Make sure you are using the proper technique with the Raster
Pen. Hold
the Pen
vertical
and push
straight down
. If you hold it at an angle it will
not work.
3. Raster™ Braille cutters and carbide drill bits are designed to last a long
time, but they don't last forever. If you have been using a cutter for a long
time, especially on hard or abrasive substrates, it may be worn out.
If your Raster™ Pen stops dispensing Rasters™:
1. Acrylic Rasters™ are prone to static cling in dry or cold climates. To break
up the static charge, shake the Pen. If you keep the barrel full or nearly full,
static will be less of a problem. Don't use dryer sheets or anti-static spray on
Rasters™ because these products can make the Rasters™ turn cloudy.
3. Check the tip of the Raster™ Pen to make sure no debris is obstructing
the passage. Any foreign matter inside the barrel will be carried along the
passage and may cause a jam. If you accidentally break a Raster™ while
inserting it, shards of acrylic may lodge inside the Pen, keeping Rasters™
from dropping into the tip or causing them to all run out at once. Empty the
barrel and blow out the Pen's internal passages with compressed air. You can
also try feeding a few metal Rasters™ through the Pen; the heavier metal
Rasters™ should dislodge anything blocking the passage.
3. If you use the adhesive-assist method, check the tip to make sure no
adhesive has built up on or inside the Pen's tip. Clear away the adhesive and
the Rasters™ should start dispensing again.
4. Push on the tip with your finger. Make sure the tip moves smoothly and
returns to the "down" position on its own. Examine the tip and the plunger
inside for wear or damage. If there is mechanical damage, you may need to
return the Raster™ Pen for repair.
If none of these answers solves your problem, please call Angie Francis or
Shevy Parasivam at (800) 215-9437 or (612) 377-9156 for further assistance.
™
Troubleshooting
Page 9
©2005 Accent Signage Systems, Inc. All rights reserved.
TM
Raster Method of Braille