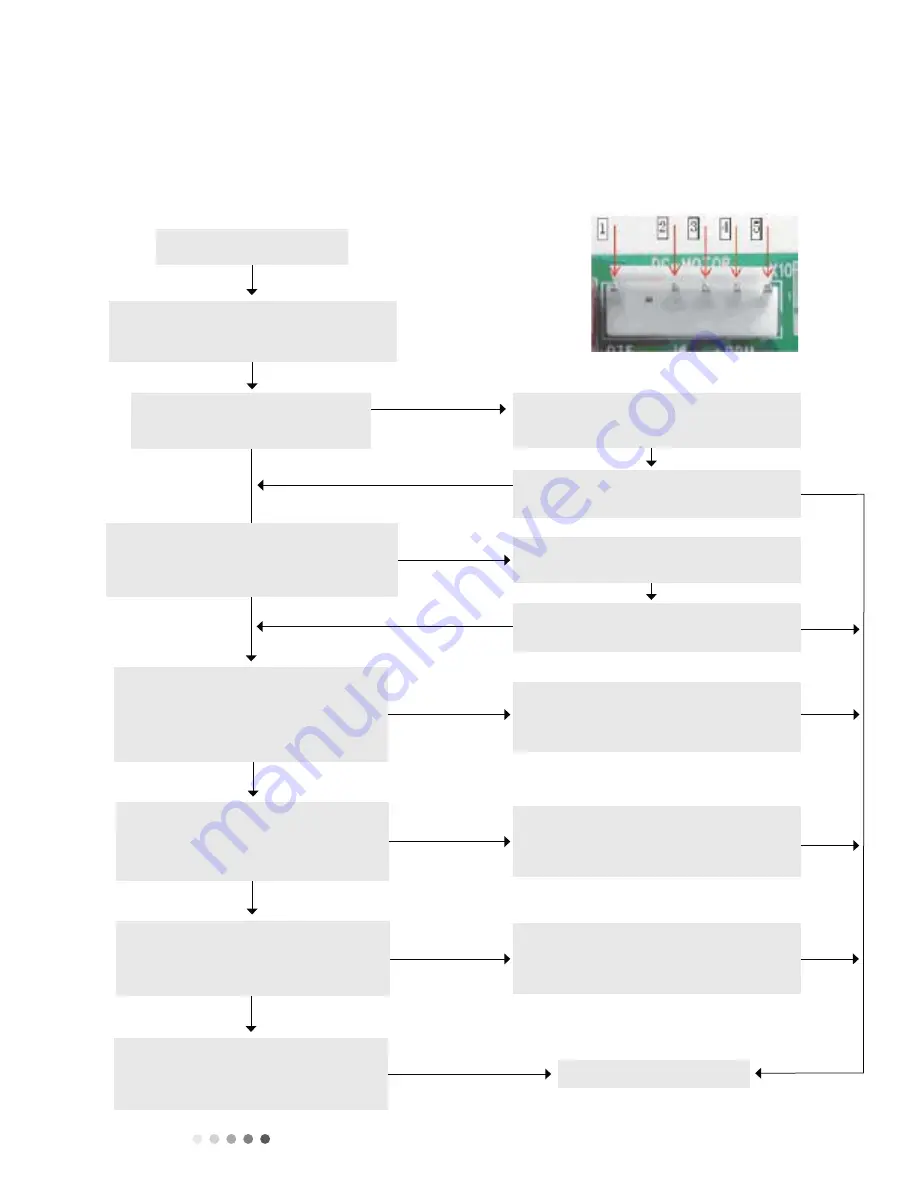
Technical Information
ƳƷ
YES
YES
NO
NO
NO
2. Malfunction of Blocked Protection of IDU Fan Motor H6
Main detection points:
• Is the control terminal of PG motor connected tightly?
• Is the feedback interface of PG motor connected tightly?
• Is the fan motor inoperable?
• Is the motor is broken?
• Is detection circuit of the mainboard defined as abnormal?
Malfunction diagnosis process:
YES
YES
NO
Turn unit on to check whether the
malfunction is eliminated
NO
Adjust the motor and blade assembly
so rotor can run smoothly
End
Turn the fan blades by
hand power is off
Do the fan blades
run smoothly?
Connect power and restart the unit.
Test whether the voltage between
terminal 1 and terminal 2 of motor
interface is within 280~310VDC.
While power is off, check the wiring
terminal between indoor fan
and main board.
Check whether the voltage between
terminal 2 and terminal 3 of the motor
interface is 15VDC.
Start
Reinsert the wiring terminal
of indoor fan
NO
Check whether there is voltage
between terminal 2 and terminal 4 of
the motor interface.
If the main board malfunctions.
Replace a new main board that is of
the same model.
YES
YES
YES
Turn unit on to check whether the
malfunction is eliminated
If the main board malfunctions.
Replace a new main board that is of
the same model.
If the main board malfunctions.
Replace a new main board that is of
the same model.
If the main board malfunctions.
Replace a new main board that is of
the same model.
YES
NO
YES