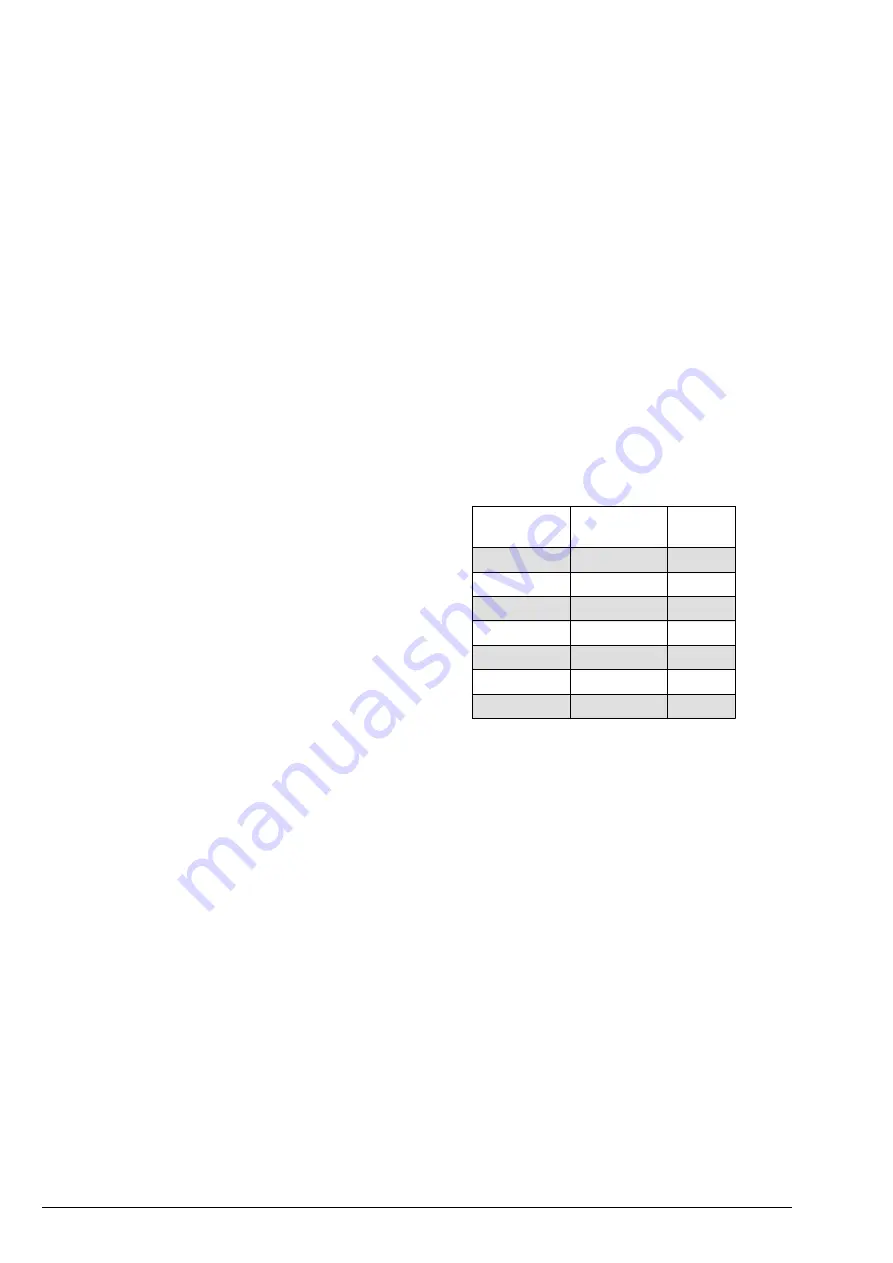
Page 6
Data : 01.03.2016
The motor circuit breakers installed in the electrical
control system are therefore no longer required
The main contactor is also switched off if a motor
current is detected without a lifting or lowering con-
trol signal.
Following a shut- down, the unit display flashes
and the current measured is indicated.
The unit is switched back on automatically after a
delay of 2 minutes.
To reset the unit before this delay has elapsed, pro-
ceed as follows:
a. Switch off the power supply.
b. Press the up and down buttons on the
digital operator terminal at the same time.
2.6
Safety Functions
The LIS- SE is a microprocessor- controlled unit. In or-
der to ensure the highest level of operational safety, the
unit is equipped with an additional switching relay
which only enables lifting or lowering if the correct
mode of operation of the microprocessor is detected.
The mode of operation is monitored by integrated logic
which operates independently of the microprocessor.
Before hoist motor starting is enabled, the system
checks whether the switching relay is in rest position. If
this is not the case, for example as a result of ”welding”
of the relay contacts, the monitoring system positively
prevents hoist start- up.
As a further safety function, the system monitors whe-
ther the lifting or lowering signal is present at all times
when the hoist motor is in operation. If the logic circuitry
does not detect a control signal at any time, the hoist is
automatically shut down by the safety circuit.
_________________________________
3
Components
3.1
LIS–SE evaluation unit
The LIS–SE unit (see
Figur 1
) is designed for evalua-
ting the power of one hoist motor.
The terminals for motor voltage evaluation are designa-
ted L1 to L3 and the current module terminals are desi-
gnated I1 to I3.
The functions of the isolated control inputs E1 to E4 are
as follows:
E1 = not used
E2 = lowering control signal
E3 = taring control signal
E4 = monitoring of fast lifting speed
E5 = receipt of malfunction signal from hoist 2
E6 = lifting control signal
E7 = fast control signal
EA = activation of second overload shut- down point
Output Q supplies a serial data protocol for the control
of the ABUS load indicators LAZ (display in pendant
control) and GLZ (large load display).
The 5V power supply for the LAZ unit is provided by the-
LIS–SE unit.
The GLZ unit has an integrated 24 V AC power supply.
The integrated digital operator terminal DBE is used for
reading and setting the variable parameters of the LIS–
SE unit (see also Section 5.1).
3.2
Current Measurement Module
The current module is selected on the basis of the rated
current of the hoist motor in main lifting speed (see ta-
ble).
Measuring
range
Rated cur-
rent [A]
Art.–No.
0
3
19683
I
8
9743
II
16
9744
III
23
9745
IV
36
9746
V
60
9747
VI
136
19682
The marked conductors of the current terminal are con-
nected to terminals I1, I2, I3 and GND of the SE unit.
3.3
Load indicator
(Optional)
The LIS–SE is equipped with contacts for the connec-
tion of an ABUS load indicator. The load can then be in-
dicated by a three or four–digit LAZ load indicator incor-
porated in the pendant control and/or a large GLZ load
indicator. Both types of load indicator are so designed
that it is easy to read the load value even in poor visibi-
lity.
During lifting operation, the driver stage of the display is
updated at intervals of 2 seconds, ensuring that any
load changes are rapidly indicated. In the case of pole–
changing hoist motors, loads are evaluated separately
for the main and precision lifting speeds. In order to
distinguish the indication of precision lifting, the display
flashes at 2/1 second intervals. In the precision lifting
speed, the accuracy at rated load is normally better
than 10 % of rated load. In the main lifting speed, the
accuracy is normally approx. 5 %. In the event of
overloading, the display flashes at intervals of 1 sec.