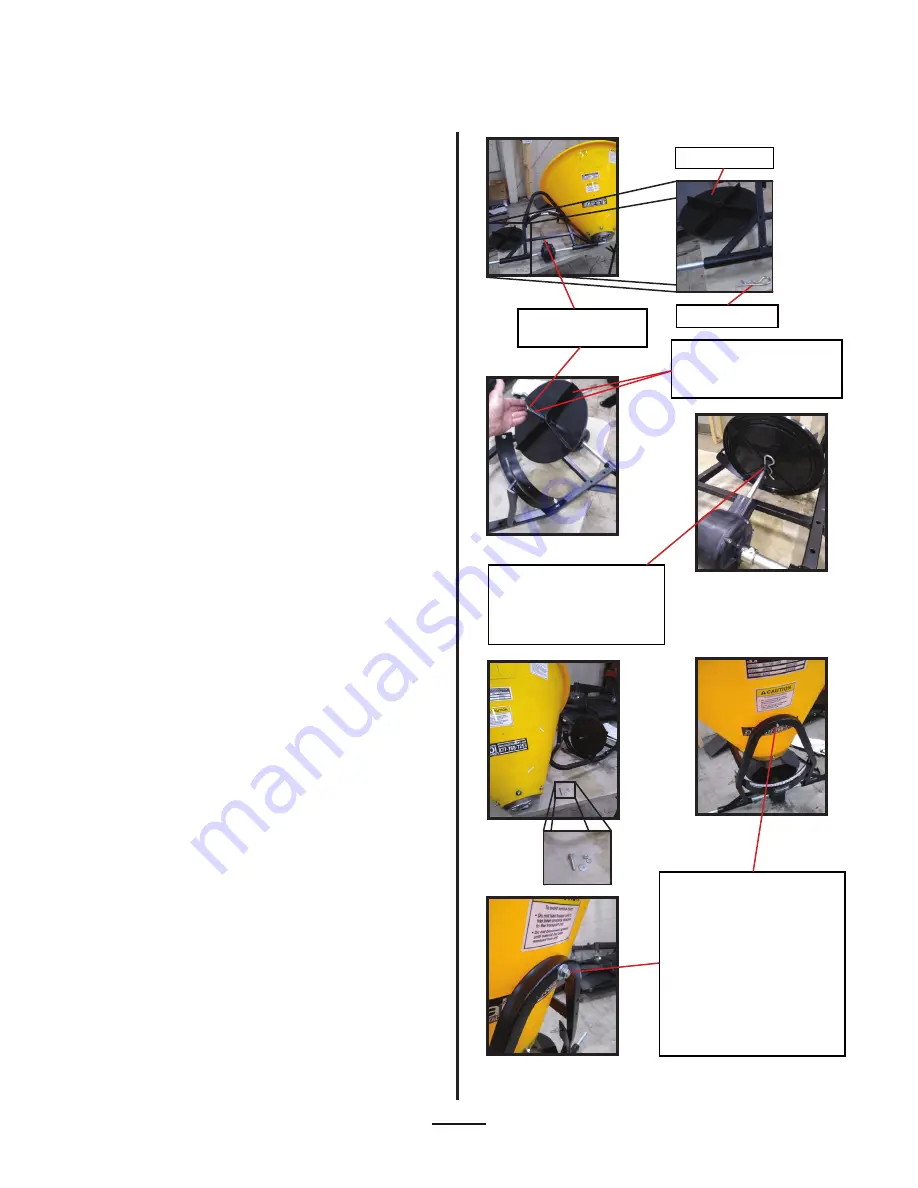
Visit:
www.abisupport.com
10
Initial Setup (cont'd)
Fig 9.
Fig 12.
Fig 11.
Fig 10.
Fig 7.
Fig 8.
Spreader disc
Flat cotter pin.
Outgoing shaft
from axle gearbox.
Slide cotter pin thru holes
in spreader disc and
outgoing shaft to secure
spreader disc to shaft.
From the inside of the
hopper, slide carriage bolt
thru the hole pointed out
in (
Fig 2
) then thru the hole
in the main support frame.
Slide fender washer and
lockwasher onto end of
bolt. Thread nut onto bolt
and tighen using (2) 13mm
wrenches or socket set.
"X" ribs of spreader disc
faces toward the end of
the outgoing shaft.
If this is the case, set the lockwasher off to the side and
thread the nut as tight as it will go to draw the square
section of the carriage bolt into the wall of the hopper. This
will give more thread length at the end of the bolt to remove
the nut and reinsert the lockwasher onto the bolt then
reinsert the nut and tighten.
7.
Locate stirrer, M6x30 Hex head bolt, (2) Ø6 washers and
the M6 locknut (
Fig 13
).
8.
Looking inside the hopper, slide the stirrer over the
outgoing shaft. Slide (1) washer onto the M6x30 bolt then
insert the bolt into the slot on the side of the stirrer then
thru the hole on the end of the outgoing shaft then thru the
2nd slot on the other side of the stirrer. Slide 2nd washer
onto the bolt then thread the M6 locknut onto the bolt and
tighten using (2) 10mm wrenches or socket set (
Fig 14
).
9.
Locate the stirrer guard, (2) M8x20 carriage bolts , (2)
fender washers, (2) lockwashers and (2) M8 nuts (
Fig 15
).
10.
Looking inside the hopper, place the stirrer guard over
the stirrer and align the slots on the stirrer guard over the
two holes in the hopper wall on either side of the stirrer (
Fig
16
). Insert the (2) M8x20 carriage bolts thru the slots on the
stirrer guard then thru the holes in the hopper wall and on
thru the long hopper support brackets welded on the main
support frame (
Fig 16 & 17
). Slide a fender washer onto
each bolt then slide a lockwasher onto each bolt. Thread an
M8 nut onto each bolt and tighten using a 13mm wrench or
socket set (
Fig 17
).
11.
Locate the flow control assembly and remove the lower
knob and washer and set aside for the moment (
Fig 18 &
19
).
12.
Slide the flow control assembly flat plate into the
slots of the mobile shutter (mention in
Fig 1 thru 4
) while
pivoting the bracket on the flow control assembly over and
behind the curved guard (
Fig 20 & 21
). If threaded hole in
flow control assembly bracket is not centered in slot on the
curved guard, rotate the curved guard up or down as needed
to center the hole in the bracket with the slot on the guard
(
Fig 20 & 21
). Once hole in the bracket is cenetered, fully
tighten the (2) nuts that hold the curved bracket to the main
support frame using (2) 13mm wrenches or socket set (
Fig
22 & 23
). Re-thread the flow control adjustment knob and
washer (that were removed in step 11) thru the curved guard
slot and into the threaded hole on the flow control assembly
bracket (
Fig 24
).
13.
Locate both wheels, (2) Ø28 shims, (2) Ø20 washers, (2)
bent cotter pins (
Fig 26
).