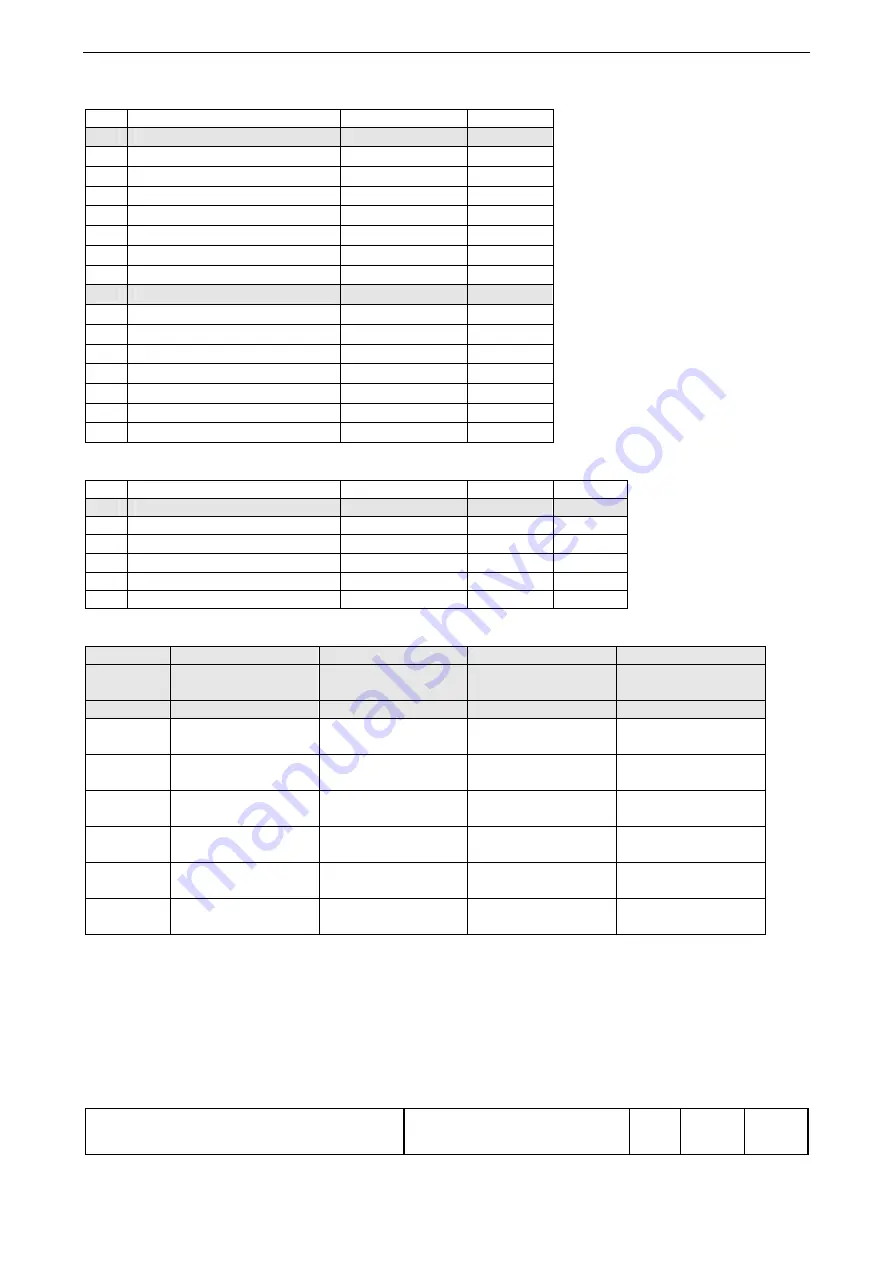
Operating Instructions
SYN 5201/SYN 5202
Document No Art Part
Language Revision
page
abb
ABB Switzerland Ltd
3BHS109762 E01
en D 135
Template: CHIND Techn doc stand, A4 P de, R1.DOT; Filename: 3BHS109762E01 D.doc; Print: 12/6/2011 5:48:00 PM; Save: 12/1/2011 2:37:00 PM; CHIND No. 3BHS109763 ZAB D14 Rev. -; I-Q
Parameter settings: Configuration parameters
Parameter
Abbreviation Value
1
Digital inputs
1.1
Digital input 1
I 1
1.2
Digital input 2
I 2
1.3
Digital input 3
I 3
1.4
Digital input 4
I 4
1.5
Digital input 5
I 5
1.6
Digital input 6
I 6
1.7
Digital input 7
I 7
2
Digital outputs
2.1
Digital output 1
O 1
2.2
Digital output 2
O 2
2.3
Digital output 3
O 3
2.4
Digital output 4
O 4
2.5
Digital output 5
O 5
2.6
Digital output 6
O 6
2.7
Digital output 7
O 7
Parameter settings: Channel 2 (SYN 5202)
Synchrocheck
Abbreviation Value Unit
1
Synchrocheck parameters
1.1 Slip
limit
smax
%
1.2 Angle
limit
max
DEG
1.3
Max. voltage difference
Umax
%
1.4
Max. zero voltage
U0max
%
1.5 Nominal
voltage
Un
VAC
SYN 5500
Device
No
Device 1
Device 2
Device 3
Device 4
Name
Jumper
open / closed
open / closed
open / closed
open / closed
W1
W2
W3
W4
W5
W6