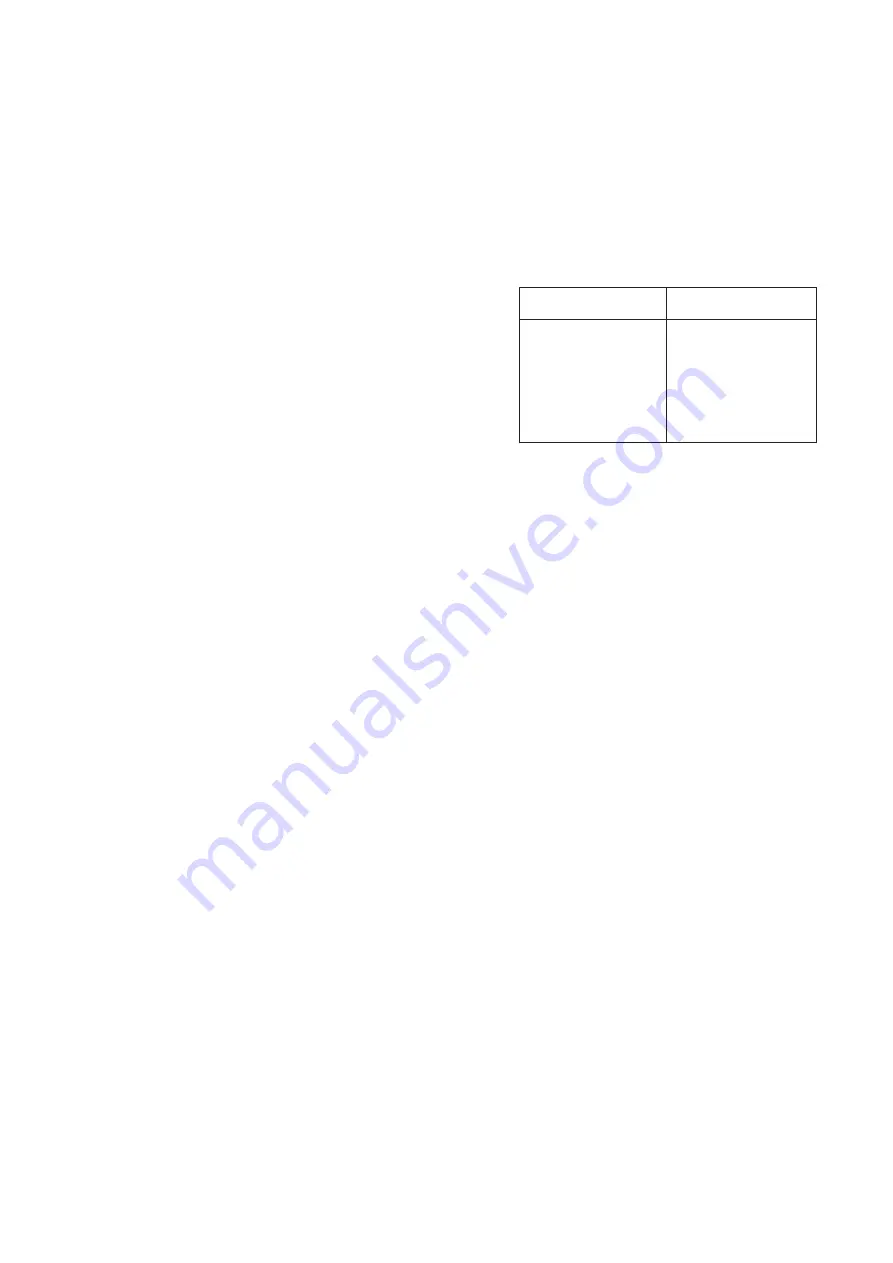
16
The start-up should be done according to the
following instructions. Checks1 and 2 have to
be performed before the auxiliary power supply
is switched on.
1. Voltage ranges of the binary inputs
Before connecting a voltage to input channels
1…9, check the operative voltage range of the
inputs. The voltage range, U
aux
, is marked on
the front panel of the control module.
2. Auxiliary supply voltage
Before switching on the auxiliary supply voltage
check the input voltage range of the power
supply module. The voltage range, U
aux
, is
marked on the front panel of the control mod-
ule.
3. Programming of the control module
SPTO 1D2
All the non-volatile EEPROM parameters have
been given default values after factory testing.
The default configuration and interlocking 1
has been selected. The default parameters are
explained in the manual of the control module
SPTO 1D2.
If the default parameters are not satisfactory, the
following parameters can be programmed:
- Configuration; default or user defined con-
figuration
- Interlocking; default or user defined inter-
locking
- OPEN and CLOSE outputs; pulse lengths
- Measurements; ratio of primary current trans-
formers, settings for active and reactive power
measurement, settings for energy measure-
ment
- Input channels 4…13; settings for polarity
and output activation
- Event reporting; event masks, event delay
times
The programming can be done via the front
panel RS 232 connection or the rear panel RS
485 connection by using a SPA protocol. In-
structions are given in the manual of the control
module SPTO 1D2.
4. Settings of the protection module SPCJ 4D29
At the factory default setting values have been
programmed for the protection module. All the
current and time settings are at their minimum
values. The default checksum values for the
switchgroups are:
Switchgroup
∑
SGF1
0
SGF2
0
SGB
0
SGR1
171
SGR2
165
SGR3
0
All tripping signals I>, I>>, I
0
> and I
0
>> are
connected to the signal TS2, which controls the
OPEN output. The signal SS1 which controls
the SIGNAL 1 output indicates starting of the
I> stage. The signal SS2 which controls the
SIGNAL 3 output indicates tripping of the I>
and I>> stages
These values can be changed manually from the
push-buttons on the front panel of the protec-
tion module. Also the RS 232 connection on the
front panel of the control module or the RS 485
connection on the rear panel of SPAC can be
used for changing the settings of the protection.
In that case SPA protocol commands are used.
The exact meaning of the switchgroups is ex-
plained in the manual of the overcurrent protec-
tion module SPCJ 4D29.
Start-up