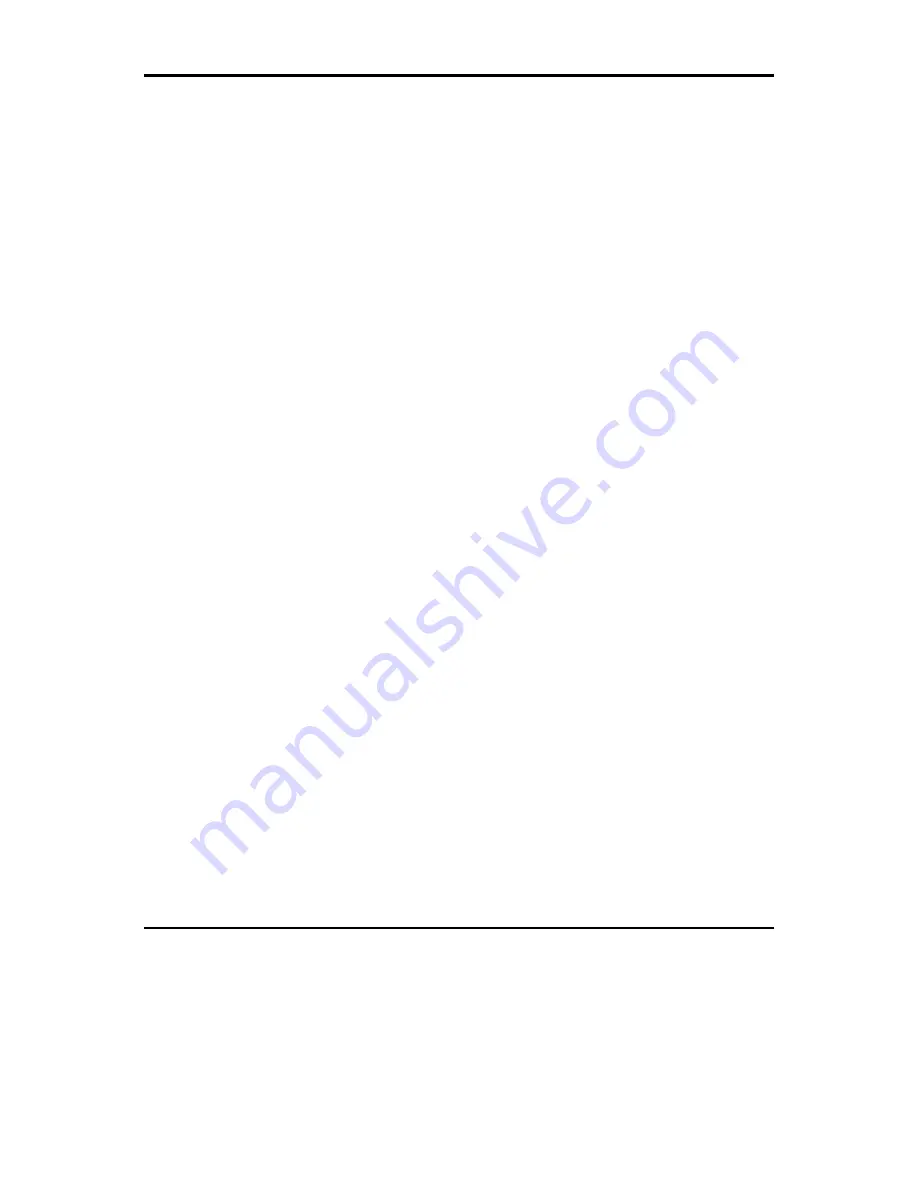
I/O System S900
Communication Interface for PROFIBUS DP, CI920
44
3BDD010422R0101
the data telegram. The modules have to be parameterized then, to define
features like line break monitoring or data formats. Refer to the S900
reference manual for details about setting the parameters.
When the project is released, the slave can communicate with the master and
can be commissioned. The application in the master can access individual I/O
data. Data processing takes place in the master application. In the case of
AC800F and Control Builder F it is entered in graphical form in the function
chart.
Commissioning with a master system that does not support
GSD file import
The easiest way to configure and parameterize a S900 is to use the DTM.
Another convenient way to configure a S900 slave is to import and interpret a
modular GSD file (device data file).
In all other cases, this document helps you to parameterize a S900 by editing
only few bytes of User_Parameters. This draft document describes
parameterization mode 1. In this mode, the CI920 has 4 bytes of parameters,
all I/O modules, and an empty slot with one byte as parameter. It is assumed
that the user or reader is familiar with importing and setting up a PROFIBUS
DP slave in the used master system or DCS.
Key features of parameterization mode 1
Generally, the settings made for one slot influence all channels of the
corresponding module. Parameterization is done by selecting a number for a
set of features or parameters.
How to configure an S900 station in mode 1
The configuration defines the "layout" of the station. S900 is a modular slave
i.e. a slave consisting of several modules. In some parts of this document, the
term "slot" is used as a synonym for "module".
The configuration is very important for both the slave and the master. It
informs the slave about the arrangement of its I/O modules and enables it to
perform a diagnostics if there should be a difference between target and real