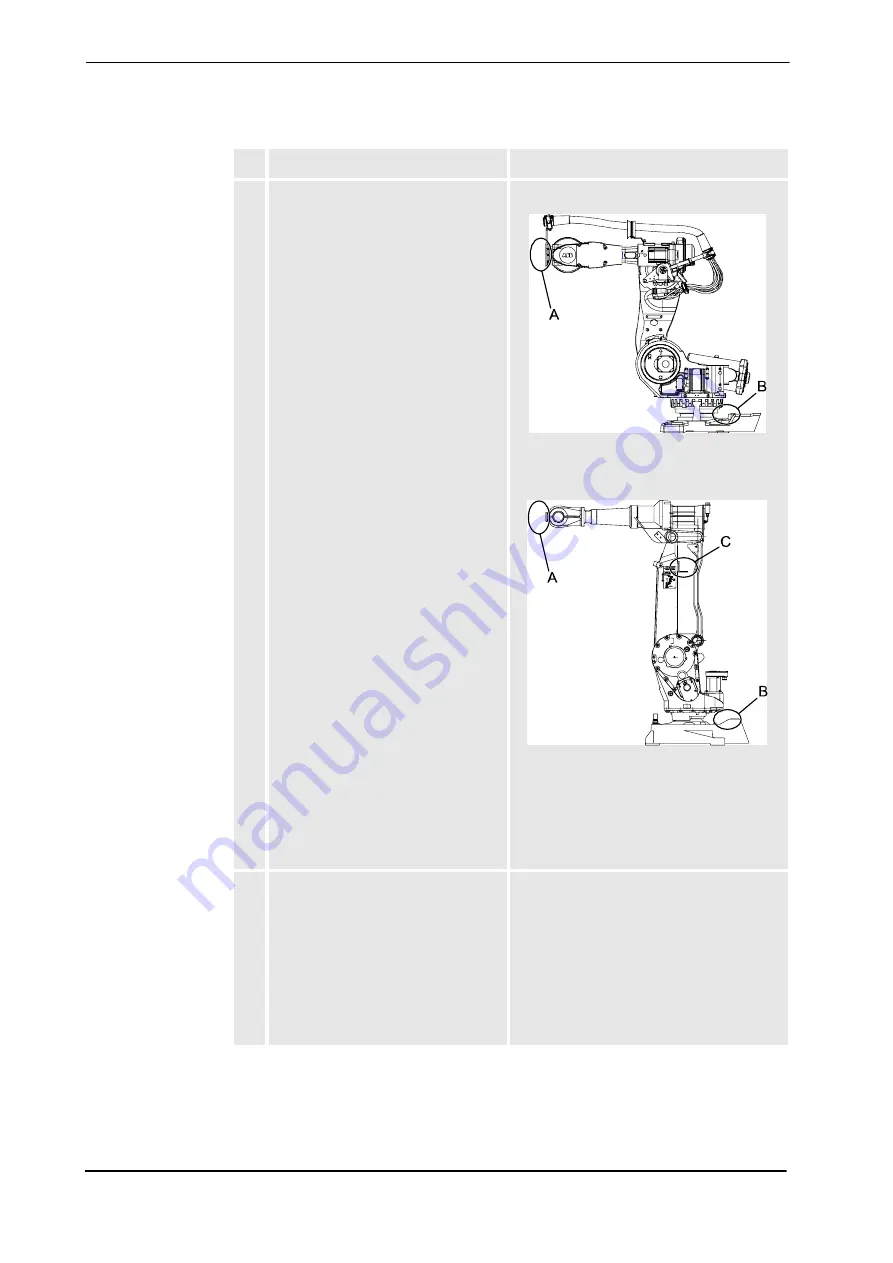
&DOLEUDWLRQ
3.3.3. Defining reference values for calibration of axes 2-6
3HAC 16578-1 Revision: E
76
© Copyri
ght
200
3-2007 ABB.
All rights reserved.
6. Prepare and clean the reference
surfaces to be used.
Clean with isopropanol.
Reference surfaces for bending backward
robots (IRB 1600, 6600, 6650, 6650S, 7600):
xx0500002470
Reference surfaces for parallel rod robots
(IRB 140, 1400, 2400, 260, 4400, 4450S,
660):
xx0500002471
A. Reference surface at the tool.
Preparation is detailed in section
3UHSDUDWLRQRIUHIHUHQFHVXUIDFHDW
.
B. Reference surface at base.
C. Reference surface of axis 2.
7. Run the service routine CalPendulum
from the FlexPendant and choose
Reference Calibration. If there are no
reference values set for the robot, the
program senses it and requires to
define these.
:DUQLQJ
The robot will automatically
move to the calibration position,
keeping the manually set axis 1 position
and setting axes 2-6 to zero.
The program will guide the operator through
the complete procedure, giving information of
each step to perform. Follow the steps in the
program carefully.
How to run a service routine from the
FlexPendant is detailed in the
2SHUDWLQJ
PDQXDO,5&ZLWK)OH[3HQGDQW
.
$FWLRQ
1RWH
&RQWLQXHG
&RQWLQXHVRQQH[WSDJH
Summary of Contents for S4Cplus
Page 1: ...DOLEUDWLRQ 3HQGXOXP LQVWUXFWLRQ DOLEUDWLRQ HTXLSPHQW S4Cplus IRC5...
Page 2: ......
Page 6: ...7DEOH RI RQWHQWV 4 3HAC 16578 1 Revision E Copyright 2003 2007 ABB All rights reserved...
Page 84: ...QGH 82 3HAC 16578 1 Revision E Copyright 2003 2007 ABB All rights reserved...
Page 85: ......