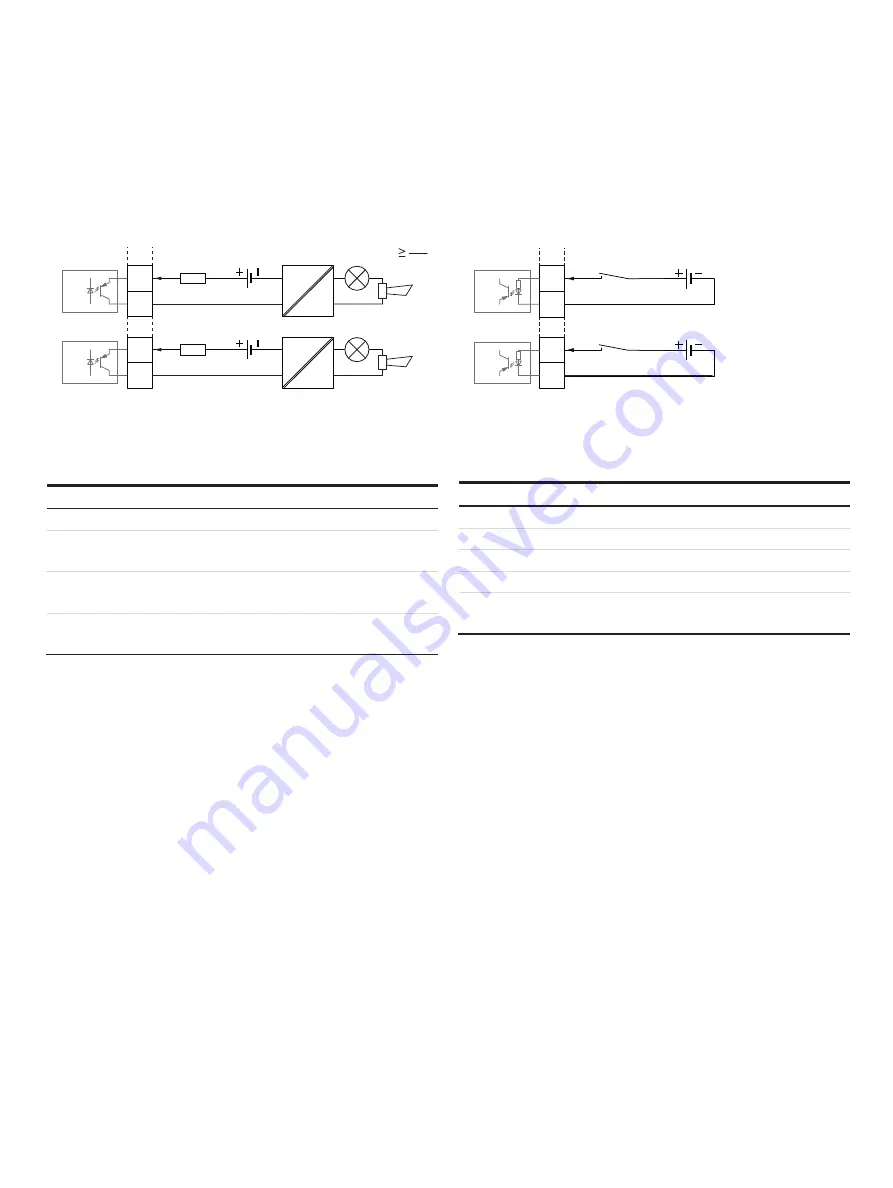
34
FEP630, FEH630
ELECTROMAGNETIC FLOWMETER | CI/FEP630/FEH630-EN REV. D
… 5 Electrical connections
… Pin assignment
Digital output V1 / V2, V3 / V4 (plug-in module)
The ‘digital output passive (green)’ plug-in card can be used to
create
one
additional binary output.
G11898-01
R
B
U
CE
I
CE
16...30 V DC
V2-
V3+
I
E
V1+
V4-
16...30 V DC
R
B
R
B
O
C
2
O
C
1
Figure 46: Plug-in card as binary output (I = internal, E = external, RB = load)
The plug-in module can be used in slot OC1
or
OC2.
Binary output (passive)
Terminals
V1 / V2, V3 / V4
Output ‘closed’
0 V
á
U
CEL
á
3 V
2 mA < I
CEL
< 30 mA
Output ‘open’
16 V
á
U
CEH
á
30 V DC
0 mA
á
I
CEH
á
0.2 mA
Switching function
Parameterization possible.
Digital input V1 / V2, V3 / V4 (plug-in module)
A digital input can be implemented via the ‘Passive digital input
(yellow)’ plug-in module.
G11598-01
16...30 V DC
V2-
V3+
I
E
V1+
V4-
16...30 V DC
O
C
2
O
C
1
R
i
R
i
Figure 47: Plug-in card as digital input (I = internal, E = external)
The plug-in module can be used in slot OC1
or
OC2.
Digital input
Terminals
V1 / V2, V3 / V4
Input ‘On’
16 V
á
U
KL
á
30 V
Input ‘Off’
0 V
á
U
KL
á
3 V
Internal resistance R
i
6.5
k
έ
Function Parameterization
possible.