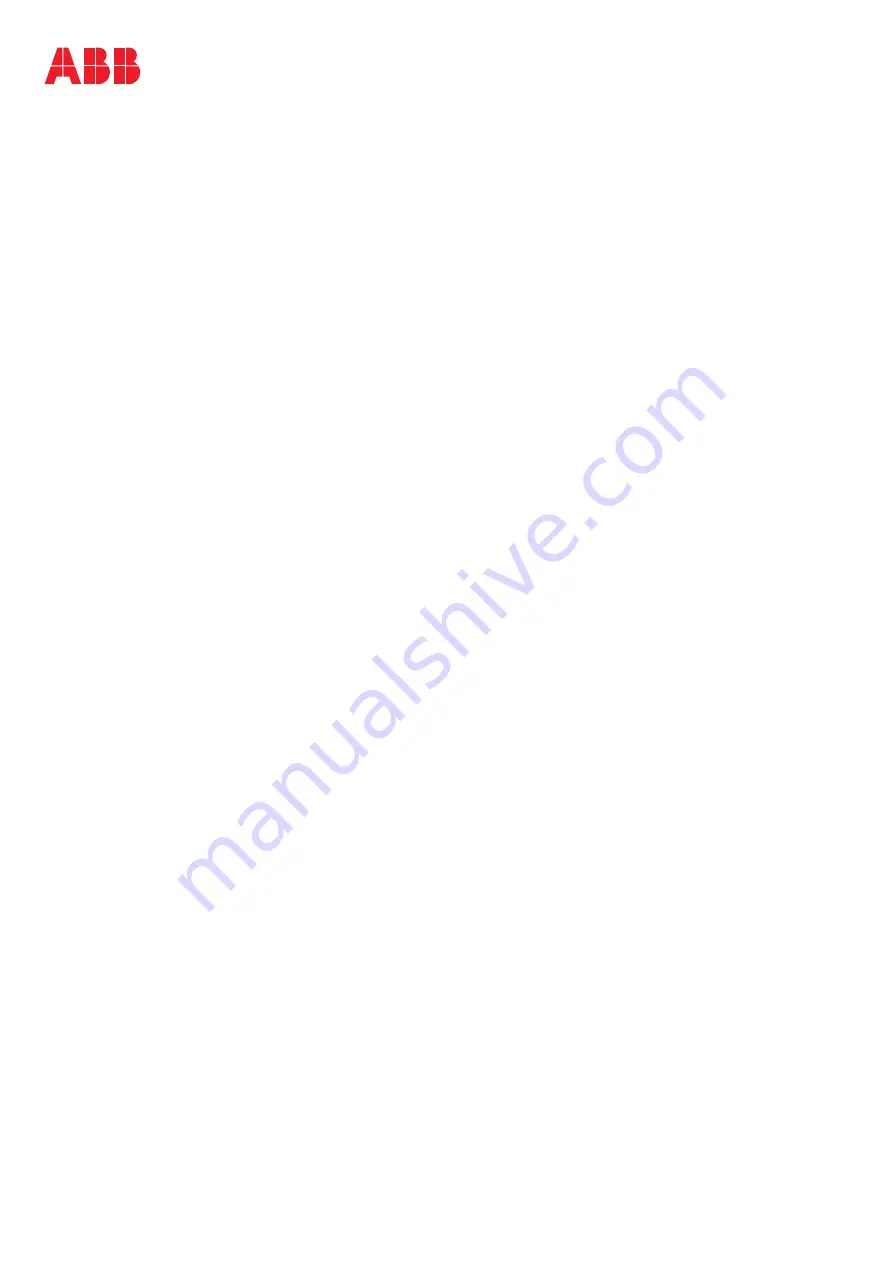
ABB AB
Robotics & Discrete Automation
S-721 68 VÄSTERÅS, Sweden
Tel46 (0) 21 344 400
ABB AS
Robotics & Discrete Automation
Nordlysvegen 7, N-4340 BRYNE, Norway
Box 265, N-4349 BRYNE, Norway
Telephone: +47 22 87 2000
ABB Engineering (Shanghai) Ltd.
Robotics & Discrete Automation
No. 4528 Kangxin Highway
PuDong District
SHANGHAI 201319, China
Telephone: +86 21 6105 6666
ABB Inc.
Robotics & Discrete Automation
1250 Brown Road
Auburn Hills, MI 48326
USA
Telephone: +1 248 391 9000
abb.com/robotics
3HAC064627-001,
Rev
G,
en
© Copyright 20192020 ABB. All rights reserved.
Specifications subject to change without notice.
Summary of Contents for IRB 14050
Page 1: ...ROBOTICS Product specification IRB 14050 ...
Page 84: ...This page is intentionally left blank ...
Page 86: ......
Page 87: ......