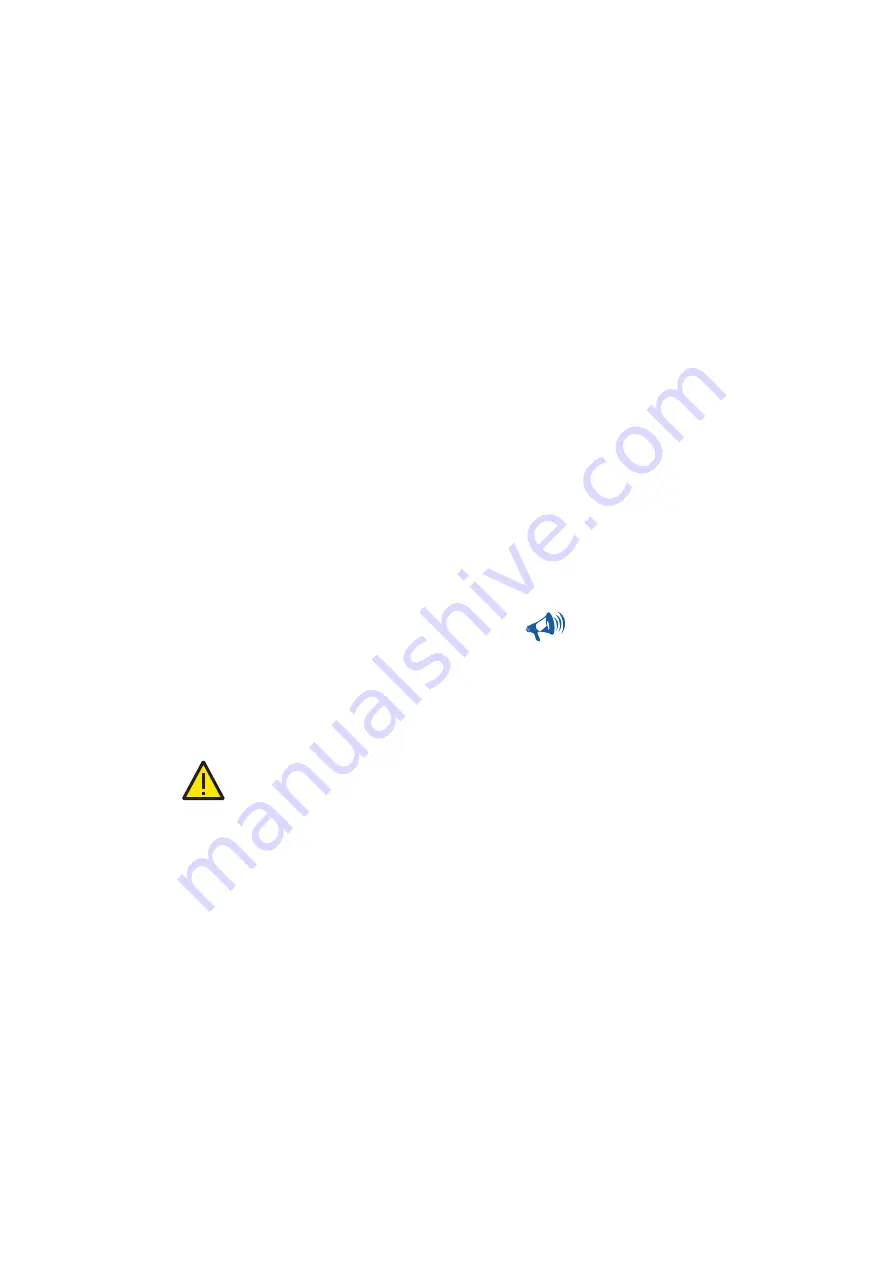
PRODUCT FAMILY: FSK II +
- OPERATING AND MAINTENANCE MANUAL
26
PRODUCT FAMILY: FSK II +
- OPERATING AND MAINTENANCE MANUAL
26
1V
S
R
6
3
0
2
0
6
E
N – e
n – E
D
O
-D
0
0
0
2
8
5
2
– I
n
st
ru
ct
io
n m
an
u
al – 2
0
21
.1
0 D
es
ig
n a
n
d s
p
ec
if
ic
at
io
n a
re s
u
b
je
ct t
o c
h
an
g
e w
it
h
o
ut n
o
ti
ce
—
8. Maintenance
Example: The capacitor bank with two parallel 0.1F
capacitors, is typically discharged after 10 min. to
below 20V.
The following procedure must be observed for a
visual inspection:
• Isolate the work area according to the
prescribed general “Safety Regulations”, earth,
secure against reclosing and if necessary
protect current-conducting parts safe from
contact and voltage. Erect barriers to prevent
accidental touching of potentially live parts
•
Inspect the condition of the apparatus
•
Check for soiling, corrosion and moisture
•
Check for increased temperatures that have
occurred on the main circuits
•
Visual checks for traces of partial discharges on
the insulator parts
• Screw checks of the HV terminals for firm
seating
• Condition of the wiring and screw checks of the
LV terminals for firm seating
• General screw check for firm seating. In
particular, screw connections in the drive unit
•
Check the connector pins of the multiple plug
connection
• Enter the number of switching operations
indicated by the counter in the apparatus
logbook
•
During operating voltage, no exterior discharges
may appear on the surfaces of the electrical
equipment. This can, for example, be determined
by characteristic sounds, a clearly perceptible
smell of ozone or visible glowing in the dark
IMPORTANT!
Never put oil or grease in the guide of the
moving contact of the vacuum switching
chamber!
8.2.1. Cleaning
If during inspections, the need for cleaning
measures is determined, the procedure should be
as follows:
• If necessary before cleaning, the work area is to
be isolated according to the “Safety
Regulations” prescribed by DIN VDE/IEC and
secured
• Cleaning general surfaces:
− Dry dust deposits with little adhesion with a
soft dry cloth
− Strongly adhering dirt with slightly alkaline
household cleaning agent or with Rivolta BWR
210 (Bremer & Leguil GmbH)
• Cleaning general surfaces:
−
Cleaning the surfaces of insulating parts and
conductive components
− Light dirt with halogen-free cleaning agents,
such as Rivolta BWR 210
− Heavy dirt on parts of insulation material with
a cold cleaner
− After cleaning, wipe away with clean water and
dry carefully
8.2.2. Check the Pole Inside Gas Pressure
This check CAN be performed every 5 years
Indicator:
0.2 – 0.8bar (overpressure) at 20 °C = OK
If the pressure falls below the prescribed
value, the apparatus should be refilled in the
factory
The pole is filled with an inert gas (N2). The
purpose of this is to fill the space between the
vacuum interrupter and the insulator with a
defined and controlled dry atmosphere.
The initial factory pole filling is in the range of 0.5
to 0.8bar at approx. 20°C. To check this, a specific
pressure gauge, which can be obtained as a spare
part, must be used.