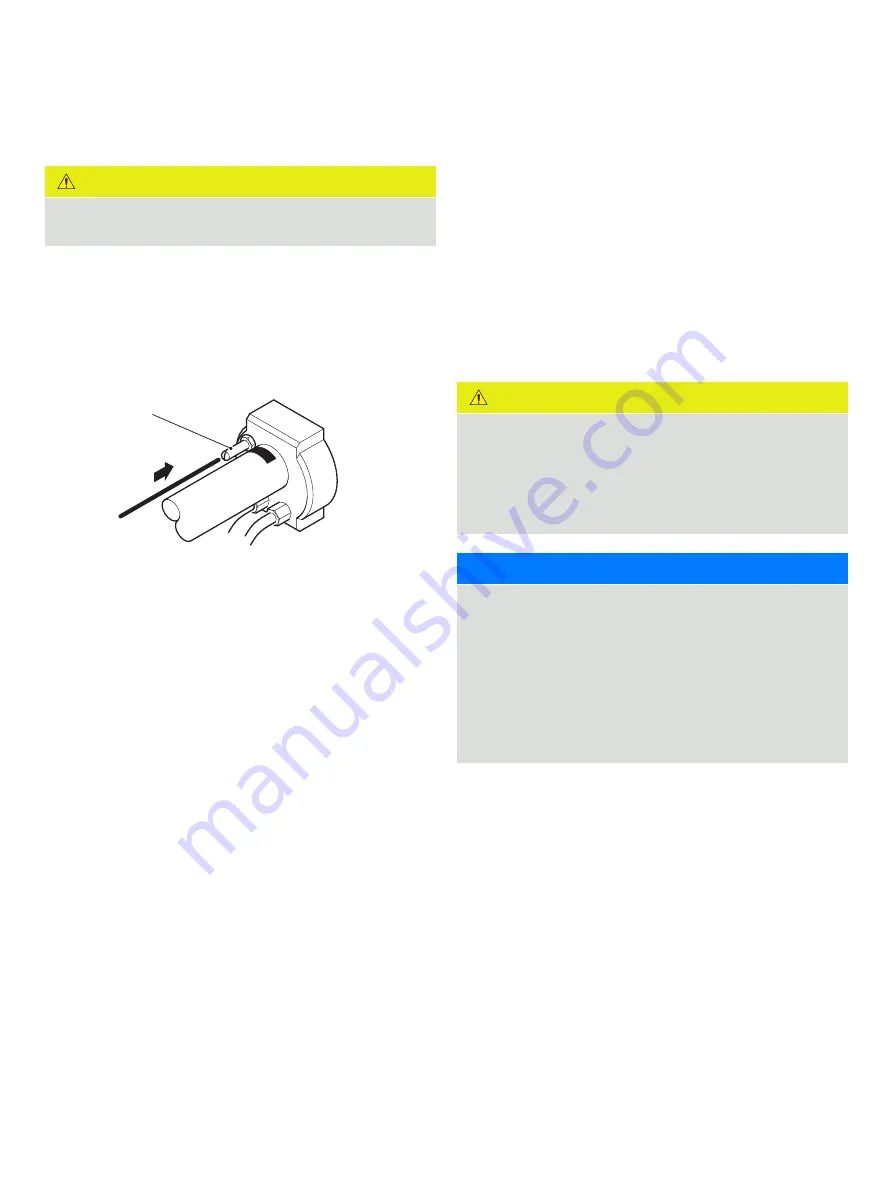
24
A Z10 OX YG E N A N A LY ZE R
| CO M B US T I O N G A S A N A LY S I S | O I/A Z 10 - EN R E V. A
8 Test gas and reference air connections
Test gas connection
CAUTION
Use clean dry instrument air free from hydrocarbons, or
traceable certified bottled test gas mixtures of O2/N2 only.
The sensor has one test gas inlet – see Figure 21. A flowmeter
must be fitted to the test gas line to restrict/regulate the flow.
The pressure is set to 1 bar (15 psi) then flow is restricted by the
flowmeter.
Refer to page 25 topage 28 for pneumatic entry types.
Figure 21 AZ10 probe – test gas connection
Test gas inlet
The sensor test gas (calibration) inlet is provided for in situ
sensor testing using a test gas.
If the sensor is connected permanently to the test gas supply
pipework:
• fit a high quality, corrosion-resistant (stainless steel),
solenoid valve, manually operated valve or non-return valve
(that is leak-tight even at zero back-pressure) in the
pipework, as close to the test gas inlet valve as possible
• keep the valve closed when the calibration system is not
in use
CAUTION
If the test gas connection is not sealed when not in use, air
leaking into the sensor via the connection causes
measurement errors. In a pressurized process, gases
venting to atmosphere through the connection cause
corrosion of, and/or block, the test gas tube. In a negative
pressure process, air leakage causes high O2 reading errors.
NOTICE
• It is preferable to use air (20.95 % O2) as one of the test
gases as this is the sensor’s zero point. Alternative
representative gases can be used according to local
environmental conditions.
• To ensure better accuracy, use 2 test gases that represent
the top and bottom limits of the known operating range.
• Due to resolution accuracies, do not calibrate the system
with gases of less than 1 % O2.