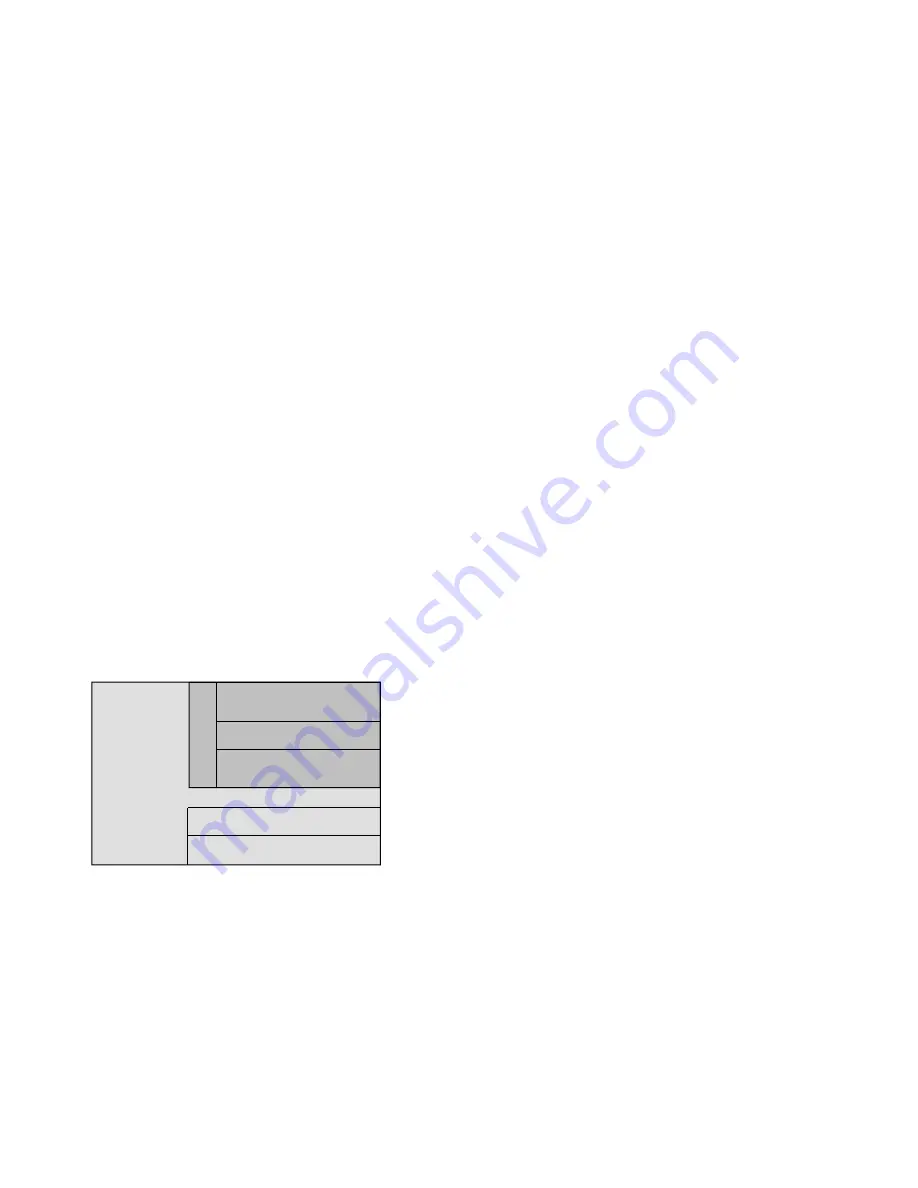
3
Overview of software (Version 15.xxx)
3.1
Basic structure of DCS 600 MultiDrive
II F 3-1
3.1
Basic structure of
DCS 600 MultiDrive
The control hardware of DCS 600 MultiDrive
consists of 2 parts:
converter control board SDCS-CON-2
drive control board SDCS-AMC-DC
(AMC =
A
pplication
M
otor
C
ontrol)
Accordingly, the software is split into 2 parts:
All control functions superimposed to the
torque reference are done inside the AMC
board. In addition, all MMI (Man Machine
Interface) and communication functions are
part of the AMC-board's software. Also the
Start/Stop functions ('Drive Logic') are realized
by the AMC-board's software. All parameters
and signals of the drive are accessed via an
AMC-board residing data structure called 'AMC-
table'.
All converter related functions and the han-
dling of standard I/O are done by the SDCS-
CON-2 software:
Armature current control
Field weakening
Motor protection
I/O handling
In general, the software functions are distributed
to the SDCS-CON-2 board and the SDCS-AMC-
DC board according to the following diagram:
3.2
Control Modes
The Control mode selects the source of control
word and references.
Local Mode
Commissioning tool Drives Window is connect-
ed to a DDCS channel (channel 3) of the AMC
Board and has entered local mode. Local mode
is also available on the panel CDP 312.
Remote Mode
Reference and control word are supplied by the
APC or a field bus adapter connected to the DDCS
channel 0.
Master/Follower Mode
Reference and control word are supplied by the
master drive via DDCS channel 2.
Fig. 3.1/1:
Distribution of software functions
Man Machine Interface &
Communication
6'&6&21
6RIWZDUH[[
Application Control
6
'
&
6
$
0
&
'
&
6
RI
WZ
DU
H
[[
Drive Control
I/O handling
Torque Control