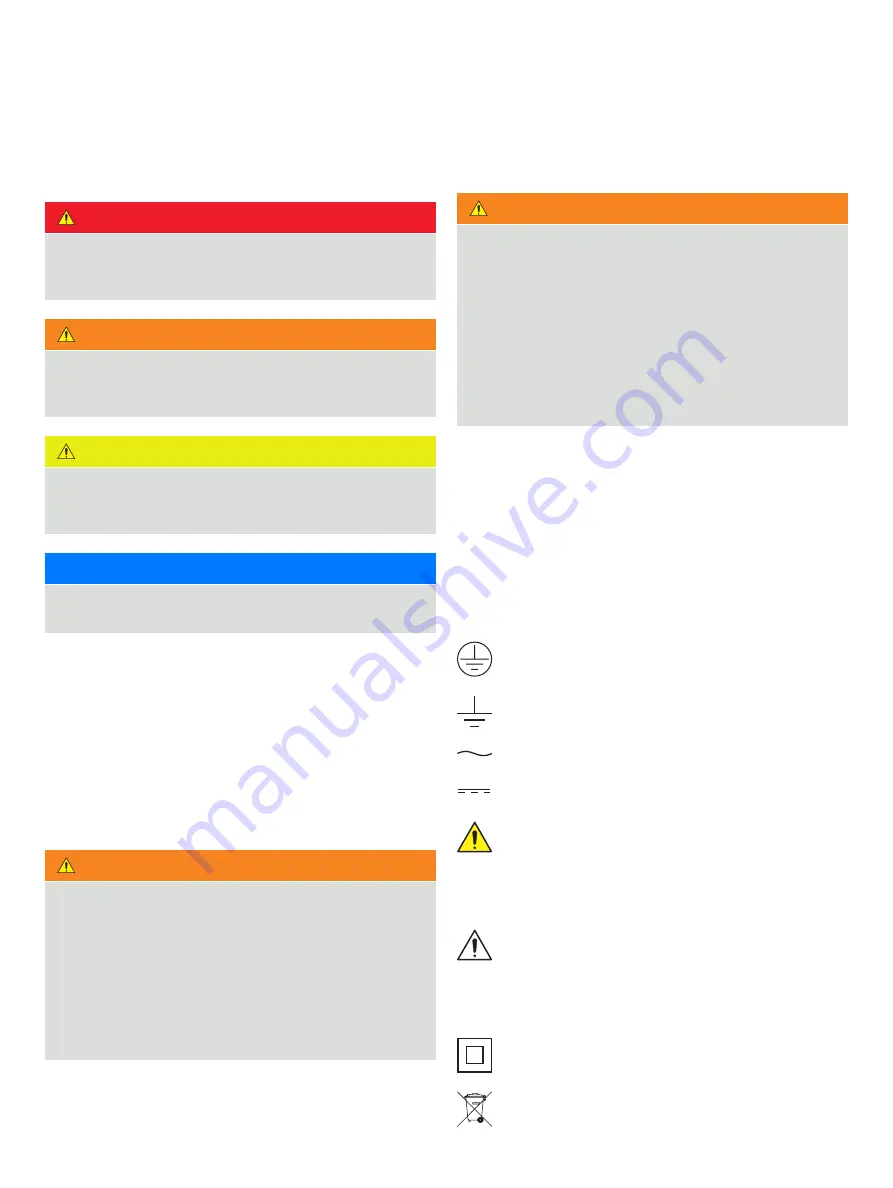
AW T4 20 |
U N I V ER S A L 4 - W I R E , D UA L- I N P U T T R A N SM I T T ER | O I/AW T4 2 0 - EN R E V. B
5
1 Health & Safety
Document symbols
Symbols that appear in this document are explained below:
DANGER
The signal word ‘
DANGER
’ indicates an imminent danger.
Failure to observe this information will result in death or
severe injury.
WARNING
The signal word ‘
WARNING
’ indicates an imminent danger.
Failure to observe this information may result in death or
severe injury.
CAUTION
The signal word ‘
CAUTION
’ indicates an imminent danger.
Failure to observe this information may result in minor or
moderate injury.
NOTICE
The signal word ‘
NOTICE
’ indicates potential material
damage.
Note
‘Note’
indicates useful or important information about the
product.
Safety precautions
Be sure to read, understand and follow the instructions
contained within this manual before and during use of the
equipment. Failure to do so could result in bodily harm or
damage to the equipment.
WARNING
Bodily injury
Installation, operation, maintenance and servicing must be
performed:
• by suitably trained personnel only
• in accordance with the information provided in this
manual
• in accordance with relevant local regulations
Potential safety hazards
AWT420 transmitter – electrical
WARNING
Bodily injury
To ensure safe use when operating this equipment, the
following points must be observed:
• Up to 240 V AC may be present. Be sure to isolate the
supply before removing the terminal cover.
Safety advice concerning the use of the equipment
described in this manual or any relevant Material Safety
Data Sheets (where applicable) can be obtained from the
Company, together with servicing and spares information.
Safety standards
This product has been designed to satisfy the requirements of
IEC61010-1:2010 3rd edition ‘Safety Requirements for Electrical
Equipment for Measurement, Control and Laboratory Use’ and
complies with US NEC 500, NIST and OSHA.
Product symbols
Symbols that may appear on this product are shown below:
Protective earth (ground) terminal.
Functional earth (ground) terminal.
Alternating current supply only.
Direct current supply only.
This symbol, when noted on a product, indicates a
potential hazard which could cause serious personal
injury and/or death. The user should reference this
instruction manual for operation and/or safety
information.
This symbol, when noted on a product enclosure or
barrier, indicates that a risk of electrical shock and/or
electrocution exists and indicates that only
individuals qualified to work with hazardous voltages
should open the enclosure or remove the barrier.
The equipment is protected through double
insulation.
Recycle separately from general waste under the
WEEE directive.