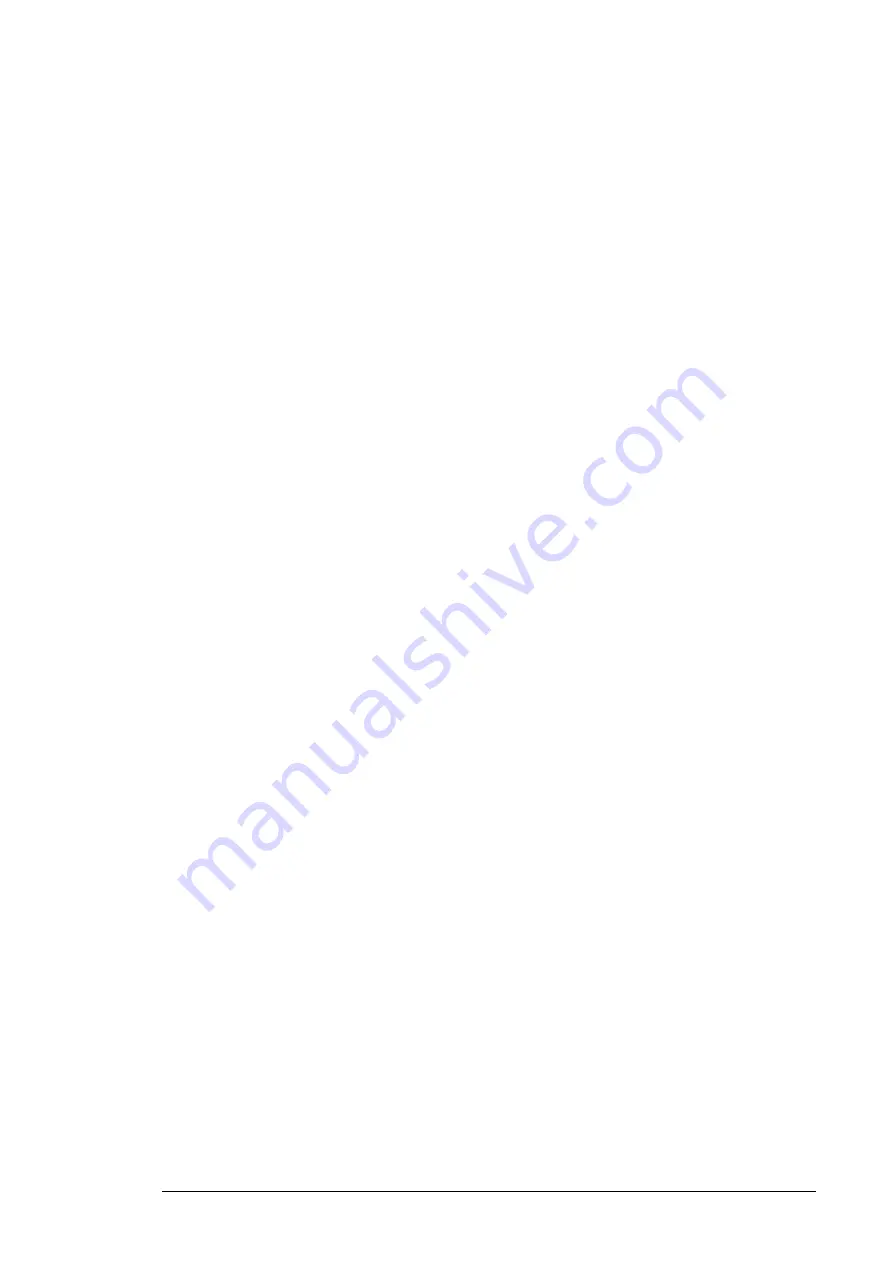
2)
Use of the signal in the control program. When parameter 120.30 External charge enable
has value Yes (default setting), the control program reserves this I/O terminal for external
charging circuit control and monitoring, and parameters 110.24 RO1 source and 110.30
RO3 source are write-protected. If the value is No, you can use the I/O terminal for other
purposes.
3)
Use of the signal in the control program (fixed). See also the delivery-specific circuit
diagrams.
4)
This input only acts as a true Safe torque off input in inverter control units. In other
applications (such as a supply or brake unit), de-energizing the IN1 and/or IN2 terminal will
stop the unit but not constitute a true safety function.
5)
Total load capacity of these outputs is 4.8 W (200 mA at 24 V) minus the power taken by
DIO1 and DIO2.
6)
Determines whether DICOM is separated from DIOGND (ie, common reference for digital
inputs floats).
DICOM=DIOGND
ON: DICOM connected to DIOGND. OFF: DICOM and DIOGND separate.
7)
Current [0(4)…20 mA,
R
in
= 100 ohm] or voltage [0(2)…10 V,
R
in
> 200 kohm] input
selected by switch AI1. Change of setting requires reboot of control unit.
8)
Current [0(4)…20 mA,
R
in
= 100 ohm] or voltage [0(2)…10 V,
R
in
> 200 kohm] input
selected by switch AI2. Change of setting requires reboot of control unit.
External power supply for the control unit (XPOW)
The control unit is powered from a 24 V DC, 2 A supply through terminal block XPOW. With
a type BCU control unit, a second supply can be connected to the same terminal block for
redundancy.
The XD2D connector
The XD2D connector provides an RS-485 connection that can be used for
•
basic master/follower communication with one master drive and multiple followers,
•
fieldbus control through the embedded fieldbus interface (EFB), or
•
drive-to-drive (D2D) communication implemented by application programming.
See the firmware manual of the drive for the related parameter settings.
Enable bus termination on the units at the ends of the drive-to-drive link. Disable bus
termination on the intermediate units.
Use shielded twisted-pair cable with a twisted pair for data and a wire or another pair for
signal ground (nominal impedance 100 to 165 ohm, for example Belden 9842) for the wiring.
For best immunity, ABB recommends high quality cable. Keep the cable as short as possible.
Avoid unnecessary loops and parallel runs near power cables such as motor cables.
The following diagram shows the wiring between control units.
Control units of the drive 57
Summary of Contents for ACS880-207LC
Page 1: ... ABB INDUSTRIAL DRIVES ACS880 207LC IGBT supply units Hardware manual ...
Page 2: ......
Page 4: ......
Page 10: ...10 ...
Page 52: ...52 ...
Page 62: ...62 ...
Page 74: ...4 74 Maintenance ...
Page 79: ...4 5 6 Maintenance 79 ...
Page 96: ...Internal cooling circuit data See chapter Internal cooling circuit 96 Technical data ...
Page 98: ...98 Technical data ...
Page 99: ... 600 mm wide incoming cubicle or input cubicle Technical data 99 ...
Page 100: ... 1000 mm wide input cubicle 100 Technical data ...
Page 108: ...108 ...
Page 118: ...118 ...