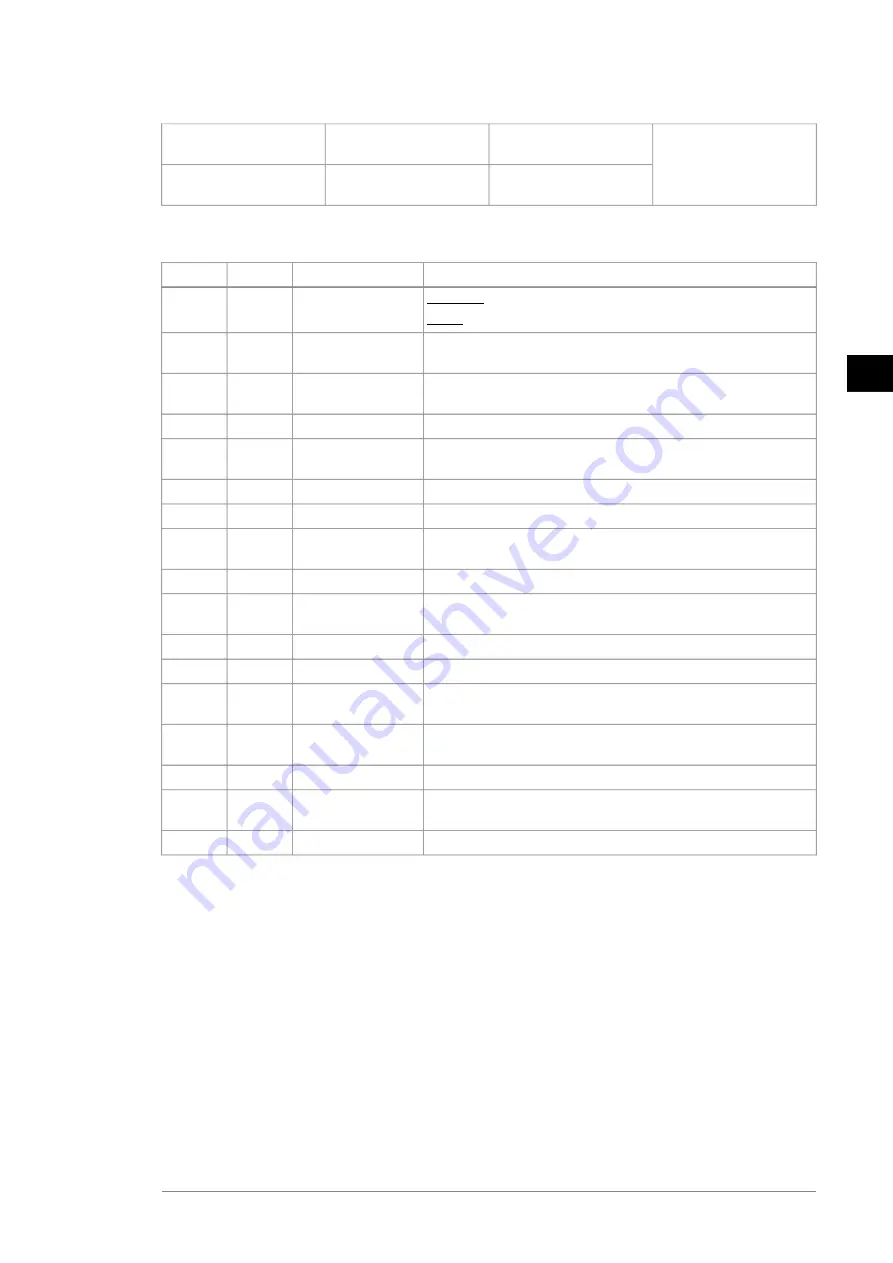
58.101 Data I/O 1
…
58.124 Data I/O 24 time
58.31 EFB act1 transpar-
ent source
58.25 Control profile
58.15 Communication
loss mode
58.33 Addressing mode
58.26 EFB ref1 type
58.16 Communication
loss time
■
Warnings and faults
Description
Aux. code
Fault
Warning
Warning: Current calibration is done at the next start.
Current calibration
2281
A2A1
Fault: Output phase current measurement fault.
The output current is more than the internal limit. This can
also be caused by an earth fault or phase loss.
Overcurrent
2310
-
A load unbalance that is typically caused by an earth fault in
the motor or the motor cable.
Earth leakage
2330
A2B3
There is a short-circuit in the motor or the motor cable.
Short circuit
2340
A2B4
The intermediate DC circuit voltage oscillates due to missing
input power line phase.
Input phase loss
3130
-
Incorrect input and motor cable connection.
Wiring or earth fault
3181
-
Intermediate DC circuit voltage is too high.
DC link overvoltage
3210
A3A1
Intermediate DC circuit voltage is too low.
DC link under-
voltage
3220
A3A2
All three phases are not connected to the motor.
Output phase loss
3381
-
STO hardware diagnostics has detected hardware failure.
Contact ABB.
STO hardware fail-
ure
5090
-
The Safe torque off (STO) function is active.
Safe torque off
5091
A5A0
Break in embedded fieldbus communication.
EFB comm loss
6681
A7CE
Communication lost between drive (or PLC) and fieldbus ad-
apter.
FBA A communica-
tion
7510
A7C1
The I/O extension module types and locations specified by
parameters do not match the detected configuration.
Extension I/O con-
figuration failure
-
ACAB
The motor ID run occurs at the next start.
Identification run
-
AFF6
The Safe torque off circuit 1 is broken.
Safe torque off 1
loss
FA81
-
The Safe torque off circuit 2 is broken.
afe torque off 2 loss
FA82
-
Safe torque off (STO)
The drive has a Safe torque off (STO) function in accordance with IEC/EN 61800-5-2.
It can be used, for example, as the final actuator device of safety circuits that stop
the drive in case of danger (such as an emergency stop circuit).
When activated, the STO function disables the control voltage of the power
semiconductors of the drive output stage, thus preventing the drive from generating
the torque required to rotate the motor. The control program generates an indication
as defined by parameter
31.22
. If the motor is running when STO is activated, it coasts
to a stop. Closing the activation switch deactivates STO. Any faults generated must
be reset before restarting.
The STO function has a redundant architecture, that is, both channels must be used
in the safety function implementation. The safety data given is calculated for redundant
use, and does not apply if both channels are not used.
EN – Quick installation and start-up guide 21
EN
DA
DE
ES
FI
FR
IT
NL
PL
PT
SV
TR
ZH
Summary of Contents for ACS880-14
Page 2: ......
Page 86: ...86 ...
Page 128: ...128 ...
Page 150: ...150 ...
Page 172: ...172 ...
Page 216: ...216 ...
Page 276: ...276 ...