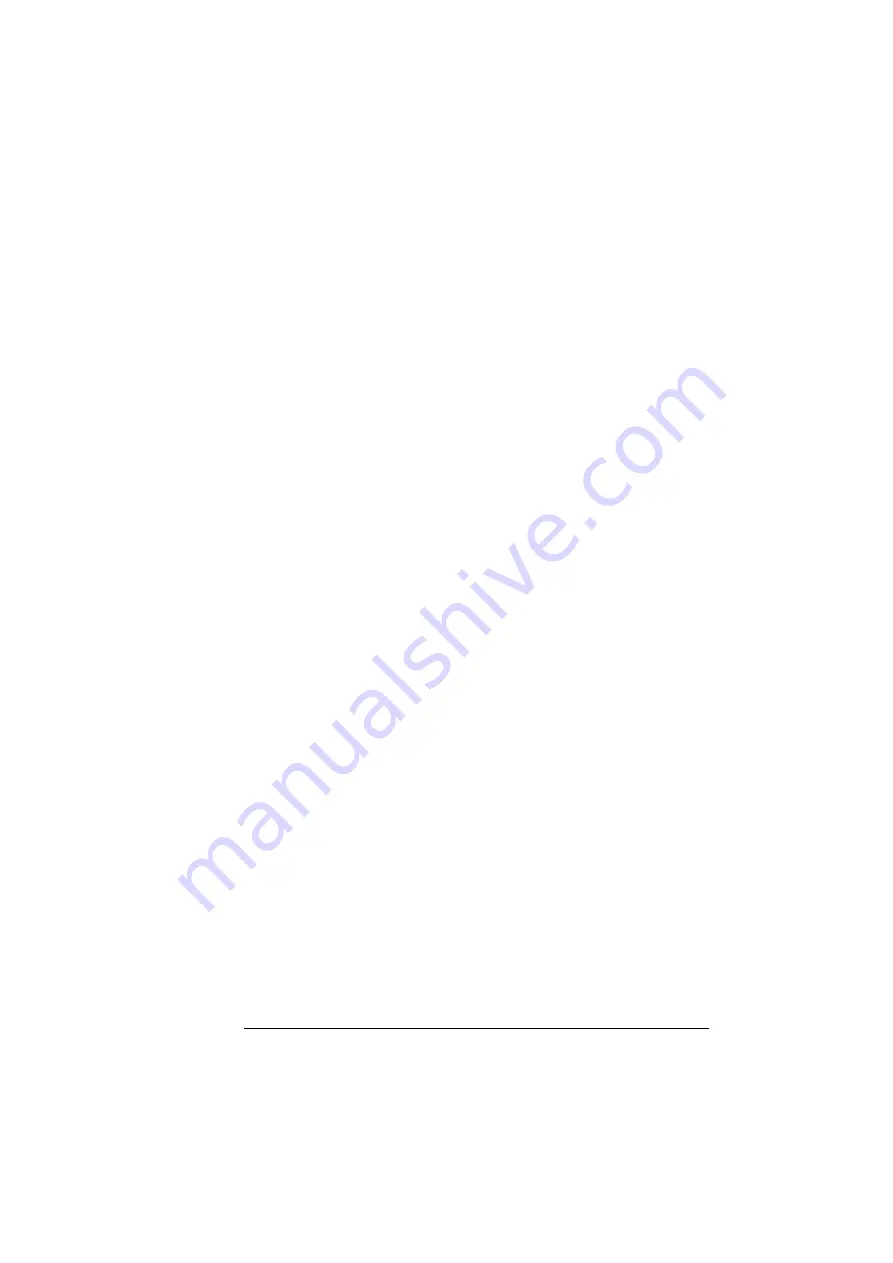
Planning – additional instructions 33
Phase loss protection
We recommend that you use phase loss guard in the AC supplies of the drives which you
connect to the AC power line. If one AC fuse blows, the semiconductors of the drives can
be overloaded and be damaged if you do not have the phase loss protection. The internal
phase loss detection of the drive will not work, as the addition DC capacitors on the system
may prevent the DC ripple becoming large enough to be detected internally.
Selecting the power cables
•
Obey the instructions in the drive hardware manual.
•
Size the conductor cross-sectional area of the drive DC cable the same as the
conductors of the drive input power cable (AC).
•
Use shielded DC cables, or only run them inside the cabinet. Ground the cable shield
at the other end only.
•
Make sure that the lengths of the individual input power cables (AC) do not differ by
more than 15% from each other.
•
Make sure that the total cable length of the DC cables between any two drives is no
longer than 50 m (164 ft).
Summary of Contents for ACS880-04 drive modules
Page 4: ......
Page 10: ...10 Introduction to the manual...
Page 16: ...16 Operation principle and hardware description...
Page 30: ...30 Planning basics...
Page 38: ...38 Planning additional instructions...
Page 48: ...Contact us www abb com drives www abb com drivespartners 3AUA0000127818 Rev B EN 2014 04 17...