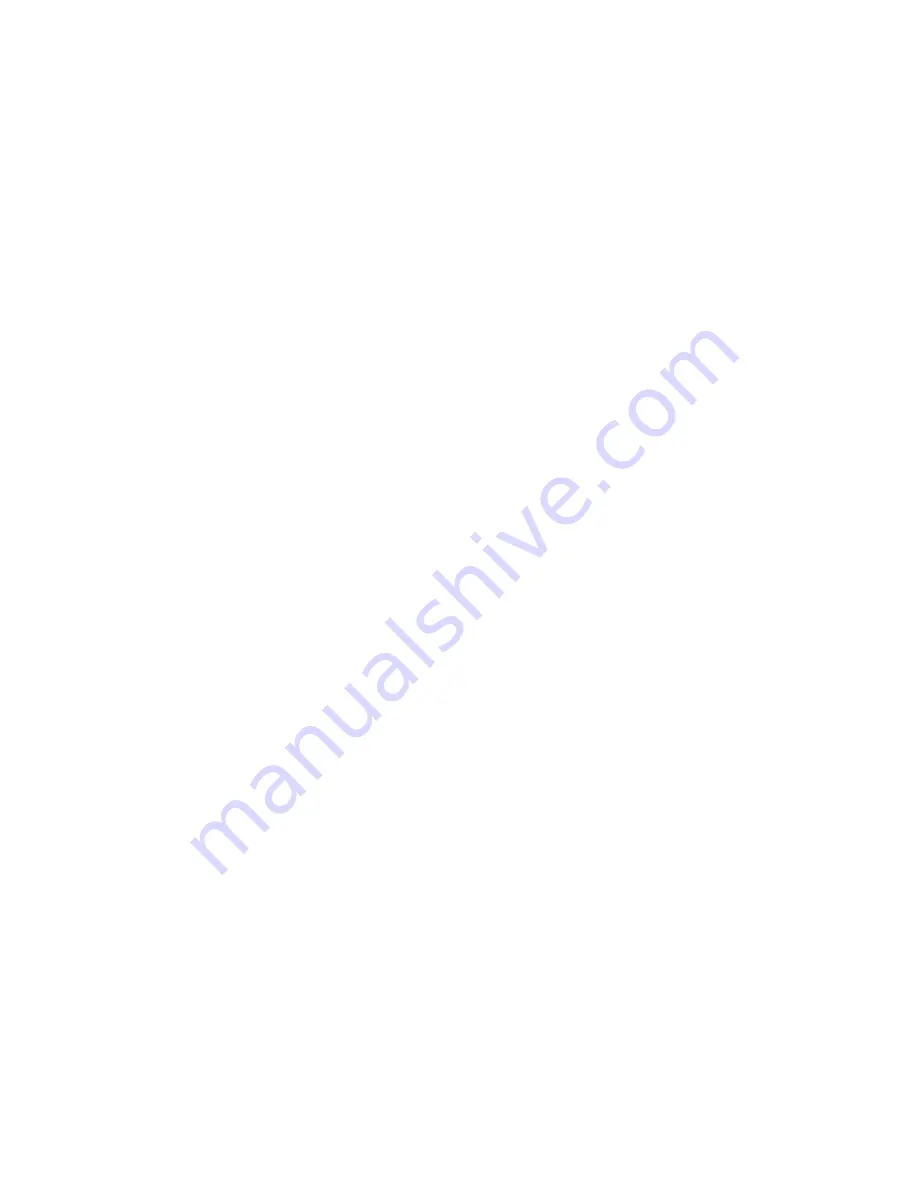
23
REFRIGERANT PIPING cont.
• If the velocity of refrigerant in the liquid line is
too great, it could cause excessive noise or piping
erosion. The recommended maximum velocities
for liquid lines are 100 fpm from the condenser
to a receiver tank to discourage fluid backup, and
300 fpm from receiver tank to the evaporator to
minimize valve induced liquid hammer.
Liquid Line Accessories:
Liquid line accessories including sight glasses
and filter driers are available and factory
installed. The total length equivalent of pressure
losses through valves, elbows and fittings must
be considered when adding additional
components in the field. It is a good practice to
utilize the fewest elbows that will allow the
mating units to be successfully joined.
Suction Line Sizing:
The suction line is more critical than the liquid
line from a design and construction standpoint.
More care must be taken to ensure that adequate
velocity is achieved to return oil to the
compressor at minimum loading conditions.
However, reducing the piping diameter to
increase the velocity at minimal load can result
in excessive pressure losses, capacity reduction,
and noise at full load.
Suction Line Routing:
• Pitch the suction line in the direction of flow
(about 1 ft. per 100 ft of length) to maintain oil
flow towards the compressor, and keep it from
flooding back into the evaporator. Crankcase
heaters are provided to keep any condensed
refrigerant that collects in the compressor from
causing damage or wear. Make sure to provide
support to maintain suction line positioning, and
insulate completely between the evaporator and
condensing unit.
• It is important to consider part load operation
when sizing suction lines. At minimum capacity,
refrigerant velocity may not be adequate to return
oil up the vertical riser. Decreasing the diameter
of the vertical riser will increase the velocity, but
also the frictional loss. A double suction riser
can be applied in this situation. The double
suction riser is designed to return oil at minimum
load while not incurring excessive frictional
losses at full load. The double suction riser
consists of a small diameter riser in parallel with
a larger diameter riser, and a trap at the base of
the large riser. At minimum capacity, refrigerant
velocity is not sufficient to carry oil up both
risers, and it collects in the trap, effectively
closing off the larger diameter riser, and
diverting refrigerant up the small riser where
velocity of the refrigerant is sufficient to
maintain oil flow. At full load, the mass flow
clears the trap of oil, and refrigerant is carried
through both risers. The smaller diameter pipe
should be sized to return oil at minimum load,
while the larger diameter pipe should be sized for
acceptable pressure drop at full load.
Suction Line Insulation:
The entire suction line should be insulated. This
prevents condensation from forming on the line,
and reduces any potential loss in capacity
associated with heat gain placing additional load
on the system.
Suction Line Guidelines:
• For proper performance, suction line velocities
less than a 4000 fpm maximum are
recommended. The minimum velocity required
to return oil is dependent on the pipe diameter,
however a general guideline of 1000 fpm
minimum may be applied.
• In a fashion similar to the liquid line, a common
guideline to consider is a system design with
pressure losses due to friction through the line
not to exceed a corresponding 1-2°F change in
saturation temperature.
• At points where small pipe size can be used to
provide sufficient velocity to return oil in vertical
risers at part loads, greater pressure losses are
incurred at full loads. This can be compensated
for by over sizing the horizontal and vertical
drop sections. This will however require
additional refrigerant charge.
Suction Line Accessories:
If the job requirements specify suction
accumulators, they must be separately purchased
and installed.