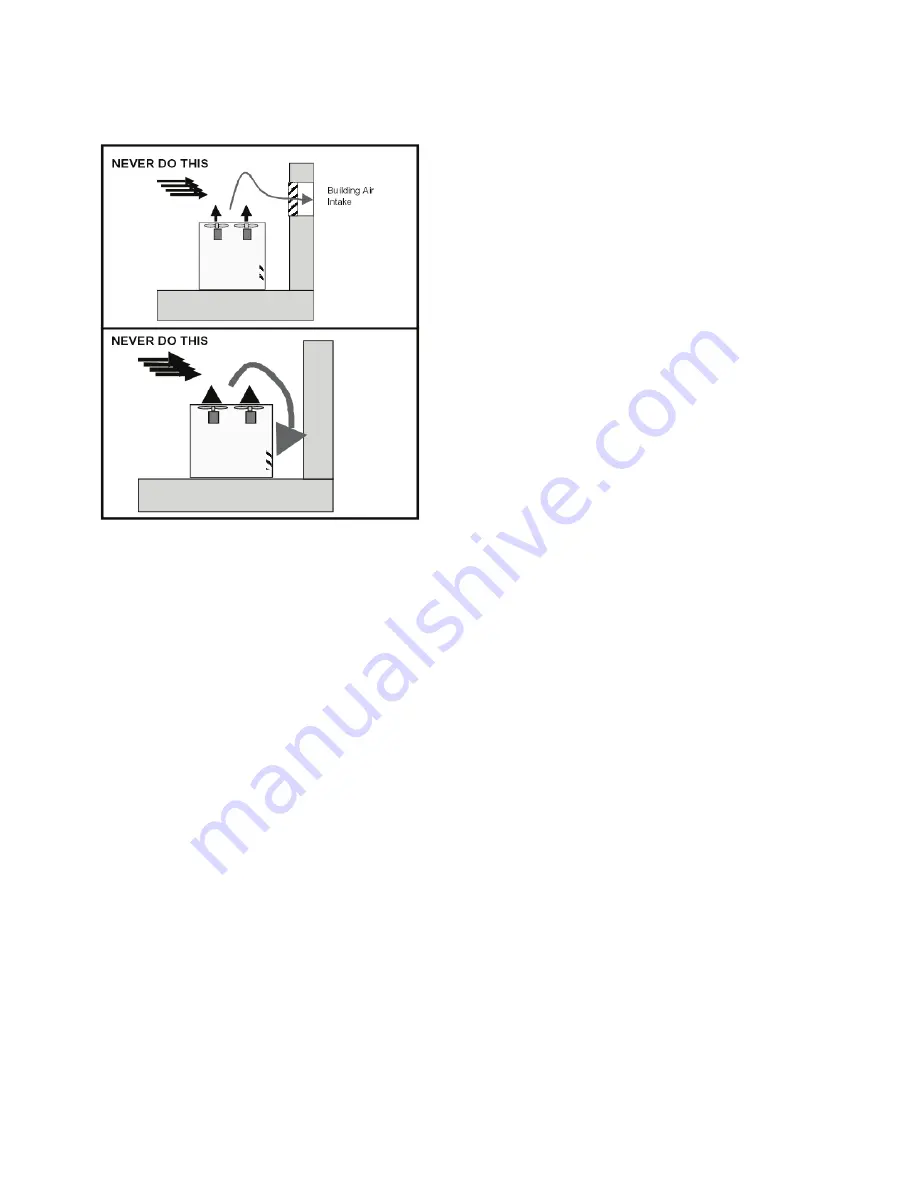
17
EVAPORATIVE-COOLED
CONDENSER cont.
Performance:
Improper location of the evaporative-cooled
condenser may seriously degrade the capacity of
the equipment. Make sure the equipment is
located such that discharge air from the
condenser does not enter the condenser air inlet.
Warranties:
Please refer to the limitation of warranties in
effect at the time of purchase.
Condenser Tube Inspection:
The coil is leak tested at 450 P.S.I.G. before
shipment. AAON will not be responsible for loss
of refrigerant. It is the responsibility of the
installer to verify that the system is sealed before
charging with refrigerant. If the unit is operated
during low ambient temperature conditions,
freeze protection for the recirculating water
system must be provided.
Freeze Protection:
In order to prevent water temperatures from
dropping below 50°F, this unit is equipped with a
variable frequency drive (VFD) on the fan
motors when the refrigeration system is
operating.
Recirculating Water System:
Electric sump heaters are available to keep the
sump water from freezing when the refrigeration
system is not operating. An electric resistance
heater is supplied in the vestibule when sump
heaters are selected.
Note: The condenser should not be operated
with the fan on and the pump cycled on and
off to maintain head pressure control under
any conditions. The unit is equipped with a
water temperature controller which varies fan
speed to maintain sump water temperature.
This unit is not equipped with a compressor
discharge pressure controller for fan speed
modulation and therefore can not be operated
without water flow.
PRE START-UP
Do not start the evaporative-cooled condenser or
compressors without installation of proper water
treatment chemicals. Contact your local water
treatment expert for correct selection of water
treatment chemical, adjustment of chemical feed
and bleed rates.
Cleanliness:
Dirt and debris may accumulate in the sump
during shipping and storage. The sump should be
cleaned prior to start-up to prevent clogging the
water distribution system. Any surfaces that
show contamination should be cleaned ONLY
with a commercial stainless steel cleaner to
restore the initial appearance. The inlet screens
should be inspected for foreign material.
Pump Operation:
Before initial start of the pump, check as follows:
1.
Be sure that pump operates in the direction
indicated by the arrow on the pump casing.
Check rotation each time motor leads have been
disconnected.
2.
Check all connections of motor and starting
device with wiring diagram. Check voltage,
phase and frequency of line circuit with motor
name plate.
3.
Check suction and discharge piping and
pressure gauges for proper operation.