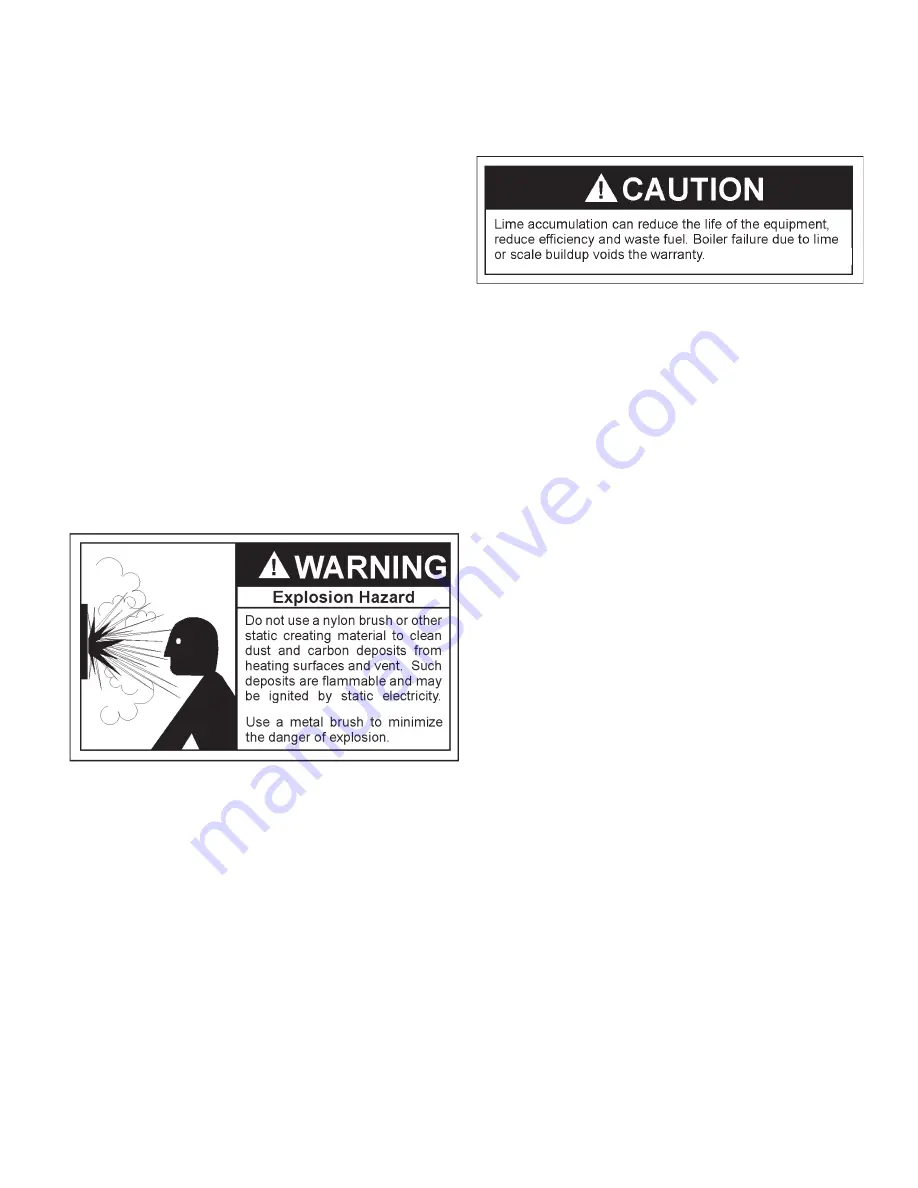
19
lines with air or water and clear or replace the blocked portions
of the line as necessary. Note that areas of the drain line which
include a sag or low spot in the line will also form a condensate trap
which can be removed by levelling the tube and does not indicate
a blocked system.
Inspect the metal vent drain and vent collector drain connectors
at six month inter vals. Remove the hoses from the connections,
then check with a small wooden dowel or plastic rod passed up
through the metal con nection to insure the passage is clear,
using caution to not bend or damage the connector. Call a
qualified service agent to inspect and correct the problem if any
obstructions are found in the connectors. Replace all hoses and
clamps immediately after inspec tion and before starting the boiler
in accordance with the lighting and operating Instructions.
DO
NOT OPERATE THE BOILER UNLESS ALL CONDENSATE
DRAIN LINES ARE PROPERLY CONNECTED AND WORKING.
When a means to neutralize condensate has been installed
you must also follow operating, inspection and maintenance
procedures specified by the manufacturer of the product. Inspect
the installed device to insure that it does not cause condensate
to remain in the boiler or vent for any reason.
VENTING MAINTENANCE
It is recommended that the intake and exhaust piping of the
appliance be checked every 6 months for dust, condensate leakage,
deterioration and carbon deposits.
Qualified service agent should follow this procedure when the
boiler’s intake and exhaust piping need cleaning:
1. Turn off the electrical power, and manual gas shut-off.
•
Allow boiler parts to cool before disassembly.
2. Remove the vent pipe.
•
Check parts and chimney for obstructions and clean as
necessary.
3. Remove burner from boiler and other metal parts as required
to clean as necessary.
•
Refer to parts list for disassembly aid.
4. Clean and reinstall the parts removed in steps 2 and 3.
•
Be sure the vent pipe has a minimum upward pitch of 1/4"
per foot (2cm/m) of length and is sealed as necessary.
5. Restore electrical power and gas supply to boiler.
•
Check for gas leaks and proper boiler and vent operation.
HEAT EXCHANGER PREVENTIVE
MAINTENANCE
In most water supply systems solids exist. As the water is heated, these
tend to drop out depositing as scale or lime. This scale must be removed
before the heat exchanger tubes become blocked.
DELIMING
The amount of calcium carbonate (lime) released from water is
in direct proportion to water temperature and usage. The higher
the water temperature or water usage, the more lime deposits are
dropped out of the water. This is the lime scale which forms in
pipes, boilers and on cooking utensils.
The usage of water softening equipment greatly reduces the
hardness of water. However, this equipment does not always
remove all of the hardness (lime). For this reason it is recommended
that a regular schedule for deliming be maintained.
The time between cleaning will vary from two to six months
depending upon water conditions and usage. A change
of approximately 5
°
F (3°C) in the normal temperature rise
through the boiler is usually an indication that scale should
be removed. For long life, copper or brass is recommended
for all valves, pipe and fittings.
TUBE CLEANING PROCEDURE
MECHANICAL REMOVAL OF DEPOSITS
Establish a regular inspection schedule, the frequency depends
on the local water conditions and severity of service. Do not let
the tubes clog up solidly. Clean out deposits over 1/16” (1.6mm)
thickness.
To service heat exchanger tubes, remove return header casting on
the side opposite the water connections. Use a U.S. standard 5/8”
deep socket ratchet to remove the nuts, exposing the tube ends.
Inspect to ensure tubes are free of scale and deposits. If scaled,
remove deposits with a stiff wire brush or mechanical tube cleaner
to bare metal. Reinstall return header casting. Flush system.
Note: Removal of the heat exchanger is not required.
REPLACEMENT PARTS
Replacement parts may be ordered through A. o. Smith dealers,
authorized servicers or distributors. Refer to the Yellow Pages for
where to call or contact (in United States) the
A. O. Smith Water
Products Company, 500 Tennessee Waltz Parkway, Ashland
City, TN 37015, 1-800-433-2545 or (in Canada) A. O. Smith
Enterprises Ltd., 768 Erie Street, Stratford, Ontario, Canada
N5A 6T3, 519-271-5800.
When ordering parts be sure to state
the quantity, part number and description of the item including the
complete model and serial number as it appears on the product.
Refer to the parts list (P/N 212802-002) for more information.
For Technical Assistance call A. O. Smith Technical Information
Center at 1-800-527-1953.
Summary of Contents for VF VB 500
Page 3: ...3 GENERAL SAFETY...
Page 6: ...6 CONNECTION DIAGRAM...
Page 7: ...7...
Page 8: ...8 Figure 1 SCHEMATIC DIAGRAM VB VW 500 750 1000 SCHEMATIC DIAGRAM...
Page 9: ...9 LIGHTING OPERATION INSTRUCTIONS FOR MODELS VB VW 500 750 AND 1000...
Page 20: ...20 notes...
Page 21: ...21 notes...
Page 22: ...22 notes...