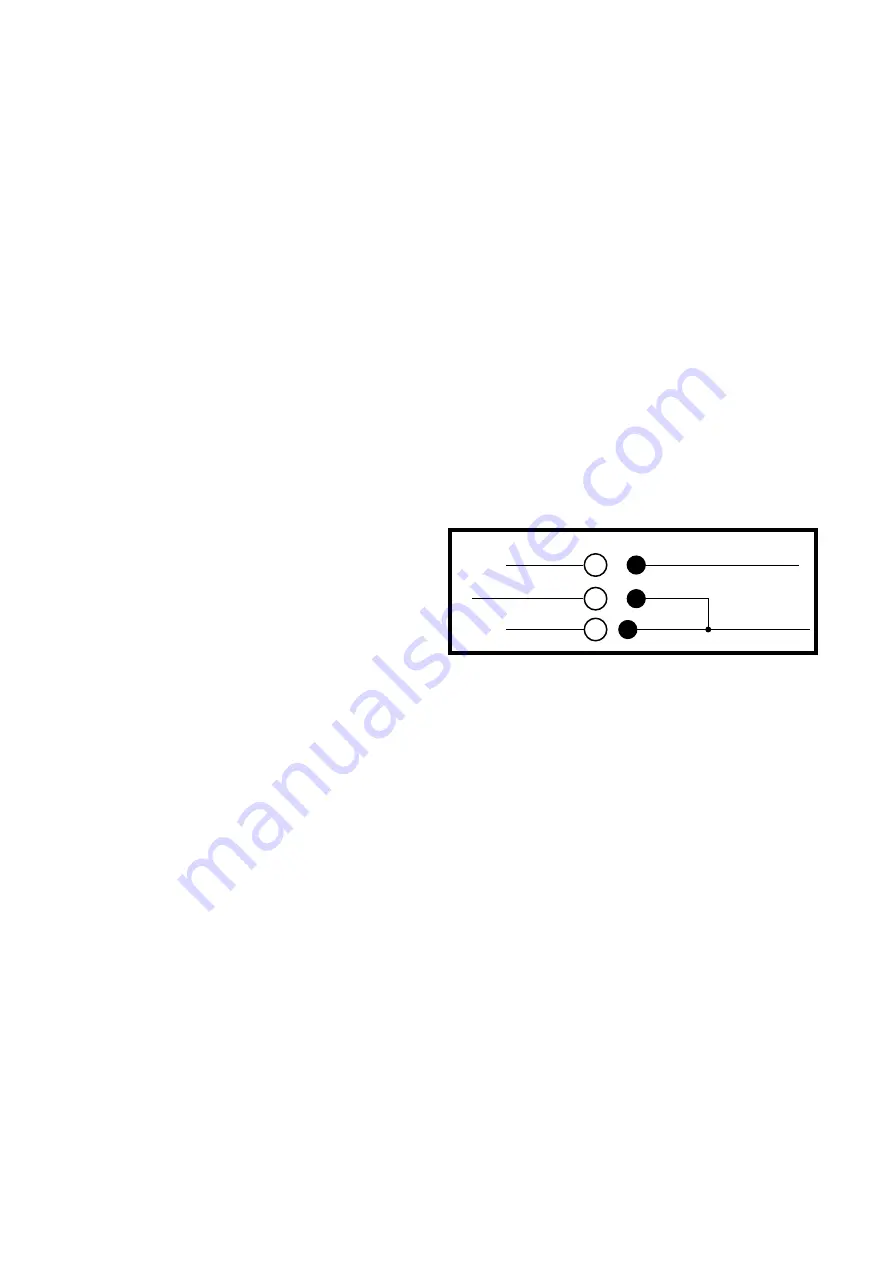
Page 3
Pro-120 controller instructions
controller down, slowing the machine.When the
controller’s output stops switching (i.e. at zero
speed), the power relay switches off.
Reversing on the Pro series controllers is normally
‘dual ramp’ but can be changed to 'pre-select' by
removing a jumper on the board.
Dual Ramp Reversing
means that, when the
reversing switch is operated at speed, the controller
slows down under control of the deceleration ramp,
automatically reverses when motor speed gets near
zero and accelerates again under control of the
acceleration ramp. If the ramp controls are set for
quick response this process can be quite violent.
Also, reversing is done by monitoring the demand
speed (after the ramping circuit) and not by
measuring the motor voltage. Therefore, if the
vehicle is reversed when going down a hill, motor
will still be rotating and the vehicle will be travelling
when reversing occurs. Reversing can therefore be
accomplished on any hill but it will be more or less
violent depending on the setting of the ramp
controls. The user is however best advised therefore
not to reverse at speed. We make no guarantees
about the mechanical effects!
Pre-select Reversing
Dual ramp reversing can be disabled on-board, when
the reversing becomes pre-select. The selected
direction will only be engaged when the throttle pot
is advanced from zero. If pre-select is used with a
joystick the controller will not reverse unless the
stick is held at zero until the motor has stopped.
Regen Braking
Regenerative braking is very reliable. However, it
works by feeding power back into the battery. If
your battery is already fully charged then regen
braking may have difficulty in operating as it has to
overcharge the battery. A similar problem exists if
the battery is disconnected, or the wiring faulty.
There are several options as to how the controller
should react under such fault conditions so if in
doubt, ask!
In any case, all passenger carrying vehicles should
be fitted with mechanical brakes: it is unwise to rely
on the battery as an emergency brake!
Charger Inhibit
Some machines have in-situ battery charging. Other
machines are designed so that the batteries have to
be removed for charging. Where the batteries are left
connected during charging, it may be considered
desirable to stop the user driving off before
disconnecting. This is the function of ‘Charger
inhibit’.
The Pro-120 has no separate inhibit input, so it is
necessary to be a little clever with the existing
inputs. You can use a switched socket for the
charger. This is a socket with an auxiliary switch
which is broken when the (charger) plug is inserted.
Such a break switch should be wired in-series with
the ignition switch, so the ignition cannot be
activated when the charger is connected.
Failing this, you can use a third pin on the charger
connector, wired as shown below.
When the charger is inserted, the link is made,
shorting the wiper of the throttle pot to battery
negative. Even if the ignition is now switched on, no
speed can be selected so the machine cannot drive.
The female part should be on the vehicle with its
sockets arranged so no metal object can touch them
when the charger is unplugged.
Many 3 pin connectors have one pin advanced so
that it is the first contact to make when the plug is
inserted. This pin should be battery negative since, if
any other pin made contact, battery positive could be
applied back to the pot wiper with destructive
consequences!
Socket
B+
B-
centre of pot (pin E)
C
Charger -
Plug