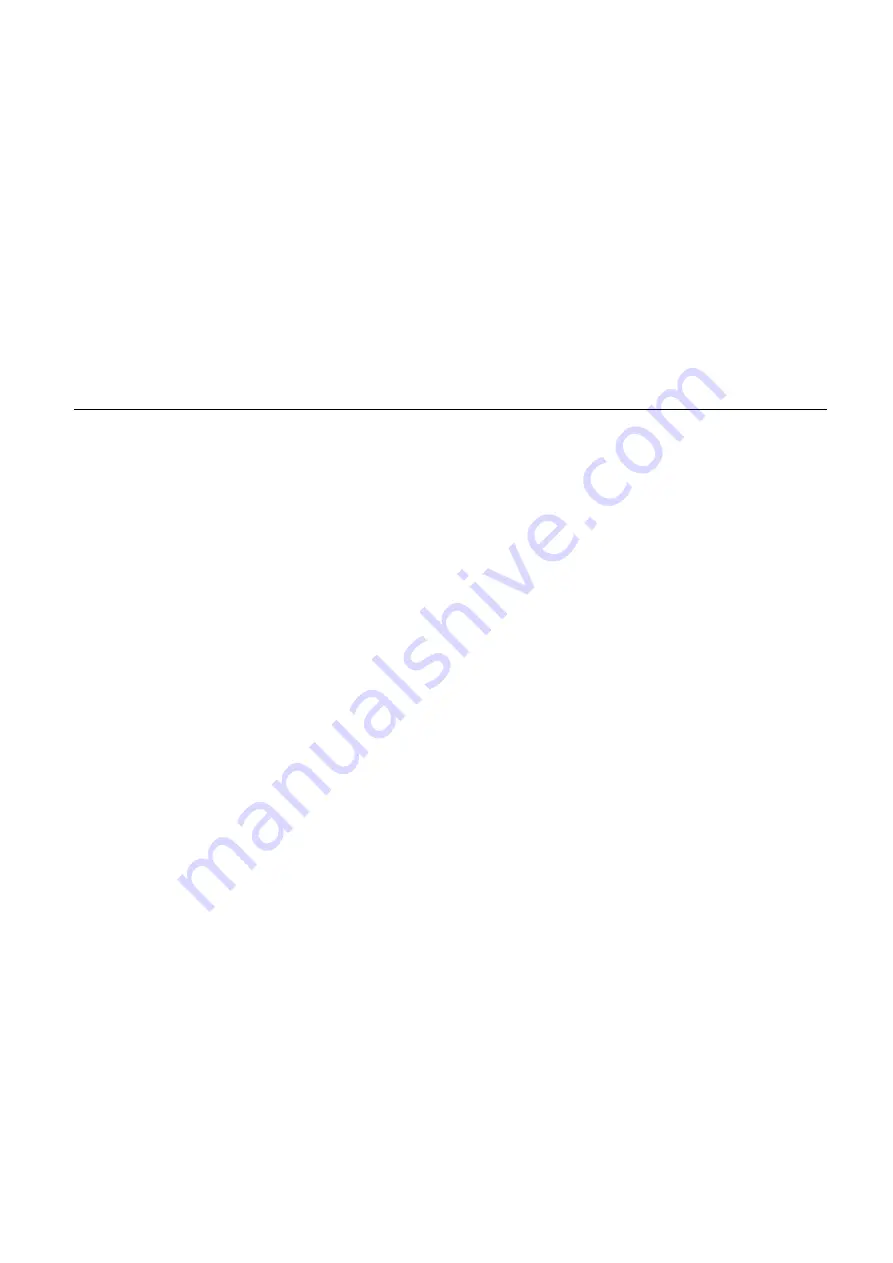
Page 12
Pro-120 controller instructions
14 Base and cover option.
(facing page)
The diagram shows the dimensions of 4QD’s base
which is available as an option.
Two A holes are for mounting the Pro-120’s
heatsink onto the base plate.
Four B holes are for mounting the cover.
Two C holes are mounting holes in the baseplate.
The board is shown cut away (the oval hole) to show
the position of the Pro 120’s heatsink block.
Base and cover are available separately so you may
use your own base.
The cover is supplied with four plastic ‘push rivets’
which locate in the ‘B’ holes.
Alternatively the cover may be fixed by using double
sided adhesive tape around the rim of the cover.
Mounting the cased controller.
Mounting holes are pre-drilled in the base plate but
if alternative mounting points are required and there
are virtually no restrictions on positioning.
The supplied holes are M5 tapped.
You can of course clamp mount the controller by
metal plates clamping onto the periphery of the
controller.
Do not drill extra holes in the base: swarf could get
into the controller and this will invalidate any
warranty.
13 Heat & Heatsinking
The long time current the controller can give is
limited by the build up of heat in the heatsink. The
controller will give over 110 amps for one minute -
this is limited by the heatsink and by heating in the
printed wiring, relays and other components. For
periods of more than a minute you need an external
heatsink to remove heat.The available continuous
current will depend on this external heatsink.
Steel is not a good heatsink material: heat does not
flow easily in steel. Aluminium or copper is far
better. If you have a steel plate, sandwich an
aluminium sheet between the steel and the Pro to
spread the heat.
For really arduous use we suggest heatsink
compound between the Pro’s heatsink and your own:
this helps heat flow across the join. Make sure both
surfaces are flat and free of grit.
Pro-120 incorporate a thermal sensor which cuts
back the output current if the controller gets too hot
(95°C) so the available current is (only) about 25
amps. At this current the MOSFETs will dissipate
about 20 watts. This is still enough to keep the
heatsink hot so don’t rely too heavily on it!