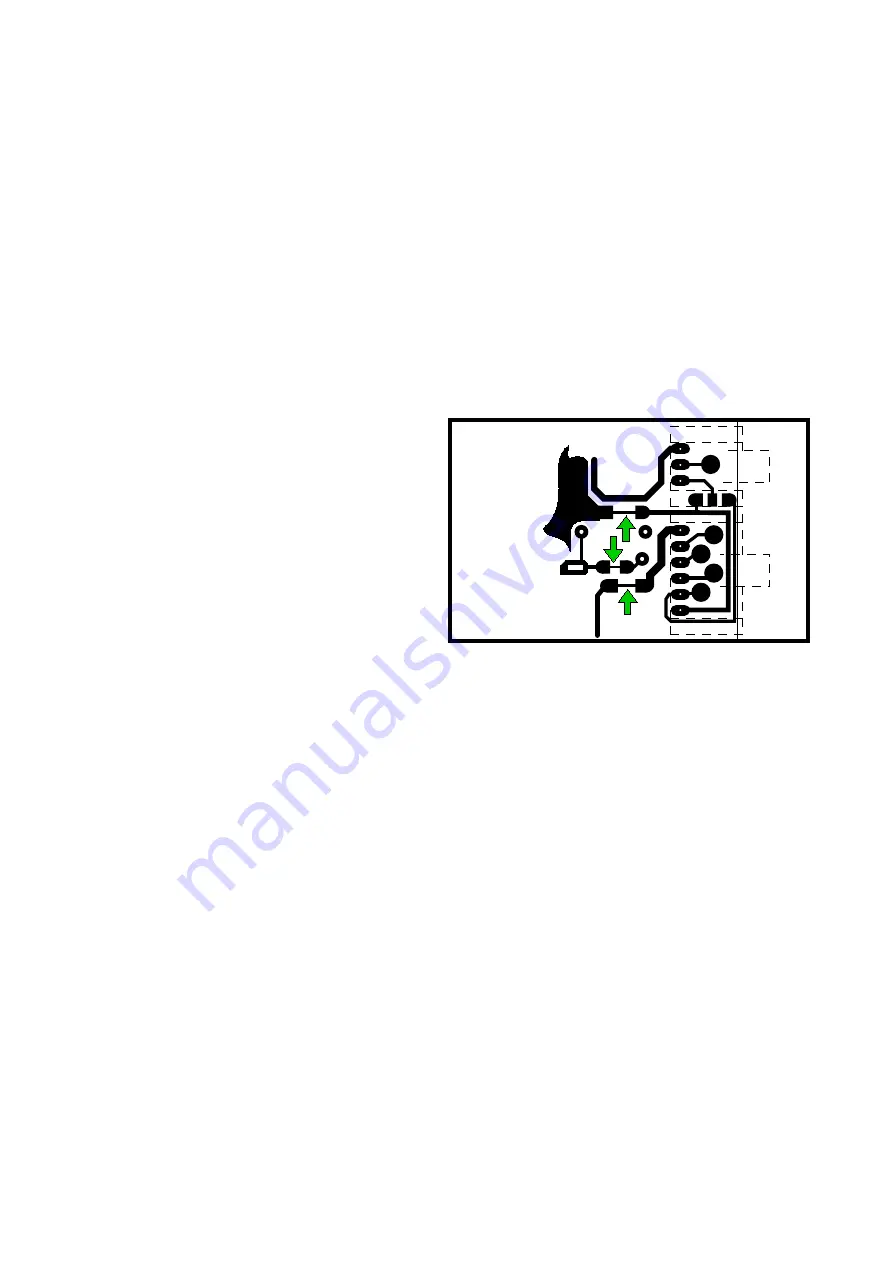
Page 15
Pro-120 controller instructions
18 Common faults
There are no ‘common’ faults: as soon as 4QD find a
fault which occurs which can be prevented, we try to
alter the design to eliminate it. This makes it difficult
to give you sensible fault finding tips - but it does
improve our product!
Most controllers returned for attention are either nor
faulty or have been damaged by ‘foreign bodies’:
nuts and bolts in the works or water etc.
There's a lot more service and fault finding info on
our www site: www.4QD.co.uk/serv/ than we can
print here!
Controller appears to be dead
Check the High Pot lockout (page 8) and the pot you
are using. HPLO and pot fault detector are intended
to detect faults and stop the controller from
working.
If HPLO engages, it will cause the power relay to
deactivate.
If a Pot fault is detected, it will simply prevent the
controller giving any output, but will not disengage
the relay.
Controller switches off erratically
The protection circuitry will switch the controller off
in the event of a fault: faults inside the controller are
rare and generally are not erratic: the controller
works or it fails.
Parking brake is used: if this is faulty or is drawing
too much current, the controller will switch off and
this will seem erratic.
Otherwise: if too low a pot value is used or some
other device draws current from the pot supply, a
fault will be detected.
Fuse and fuse tracks
These are present to prevent major damage to the
controller is there is an external wiring fault.
There are three special sections of track which
should blow if a major fault occurs in the controls or
the brake (connected to the 6 pin and 3 pin input
connectors). They are situated beneath the input
connectors on the back of the board. They are thin
‘waists’ in the track and are is as shown arrowed in
the diagram, above. If one fuses, solder a fine piece
of wire over it - one strand from 7/0.2 cable is fine.
If you cannot cope with fixing the fuse track, should
it blow, then you should fit the fuse shown in the
‘Connections’ diagram, page 7. Use a 1 amp fuse.
Overheating
Beware of sustained overheating: the heatsink can
operate up to 95°C but not more (the overheat sensor
will operate).. The main decoupling capacitors may
get warm, but should not be allowed to remain too
hot to touch for too long.
The other limit is the soldering to the relays: the
current is limited just below that required to cause
the solder to melt!
earth track
There are few applications where regenerative
braking is deleterious and it should normally be left
engaged. However it is possible to disengage it.
When regen braking is disengaged:
1: the controller must be also switched to pre-select
reversing (section 9.08)
2: Chose a long deceleration ramp setting, as the
motor will brake only under friction.
Failure to do this will cause jerky performance and
may burn out the relays.
To deactivate regen braking, the two links shown as
RB1 and RB2 on the features diagram, page 4 must
be broken. Holes are present so removable headers
can be fitted, but these are normally not present.
17 Disabling Regen Braking