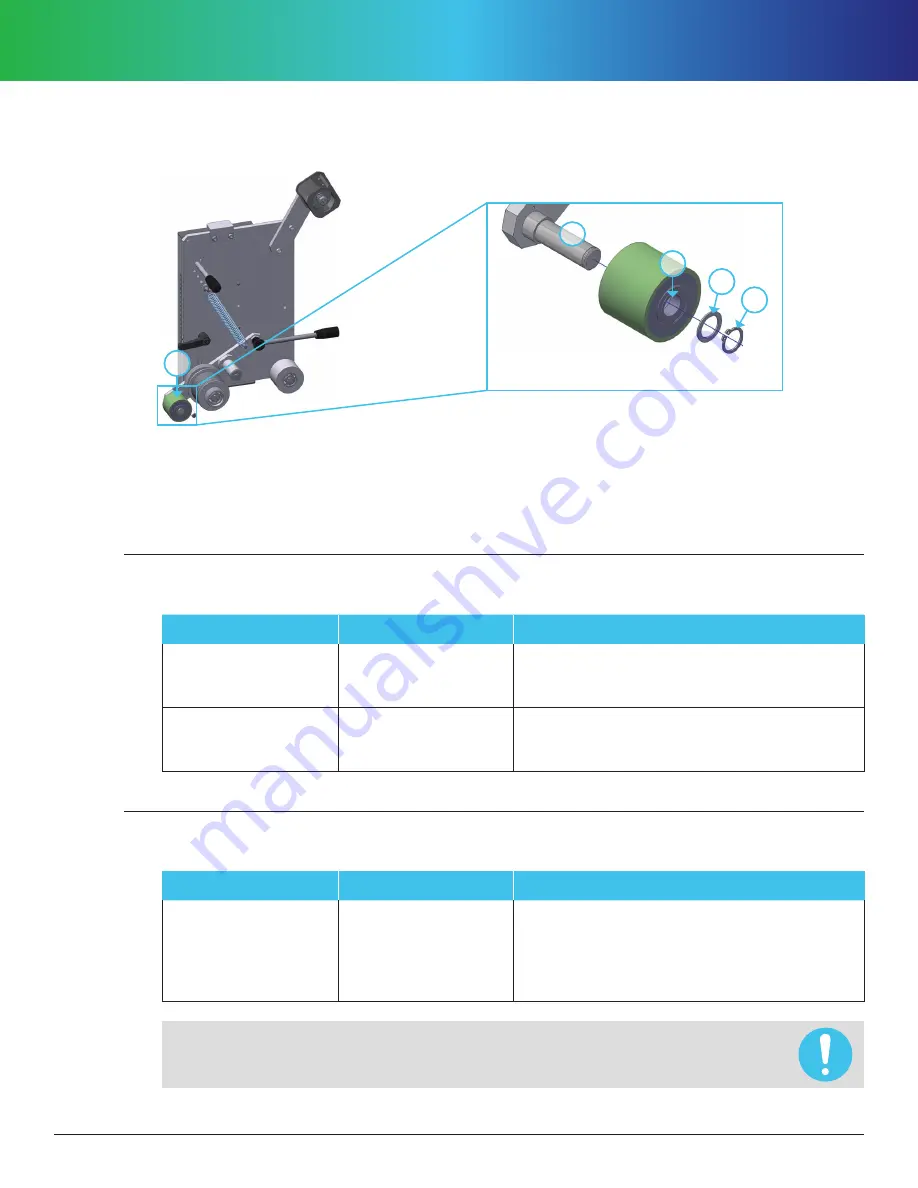
Page 36
3M
™
Straight Line Laminator Single Head Manual
|
Original Assembly and Operation Instructions
Effective: August 2022
9.1.4 Maintenance and Replacement of the Application Roller
Figure 36
1 . To replace the application roller (Figure 36A) remove the retaining ring (Figure 36E) .
2 . Then you call pull the washer (Figure 36D) and the application roller (Figure 36C) off the axle of the
application roller (Figure 36B) .
3 . Assembly takes place in reverse order .
9.2 Maintenance Schedule
Assembly Group
Interval
Work to be Performed
Continuous Laminator
As required .
Over time, residues of the adhesive tape may
deposit . In case of increased wear, it may be
necessary to replace highly stressed components .
Non-stick Coated Parts
Monthly/immediately
when adhesive tape
begins to stick!
Check for damages and non-stick effect and
replace, if necessary .
9.3 Cleaning Schedule
Assembly Group
Interval
Work to be Performed
Continuous Laminator
Every 3 days .
Daily if necessary .
Cleaning of the coated deflection pulleys .
Over time, residues of the adhesive tape
may deposit . Remove moderate soiling with
FT 100, heavy soiling with GS 200 .
Please Note: No mechanical cleaning!
NOTE:
Please observe the operating instructions of the respective purchased parts as well .
A
B
C
E
D