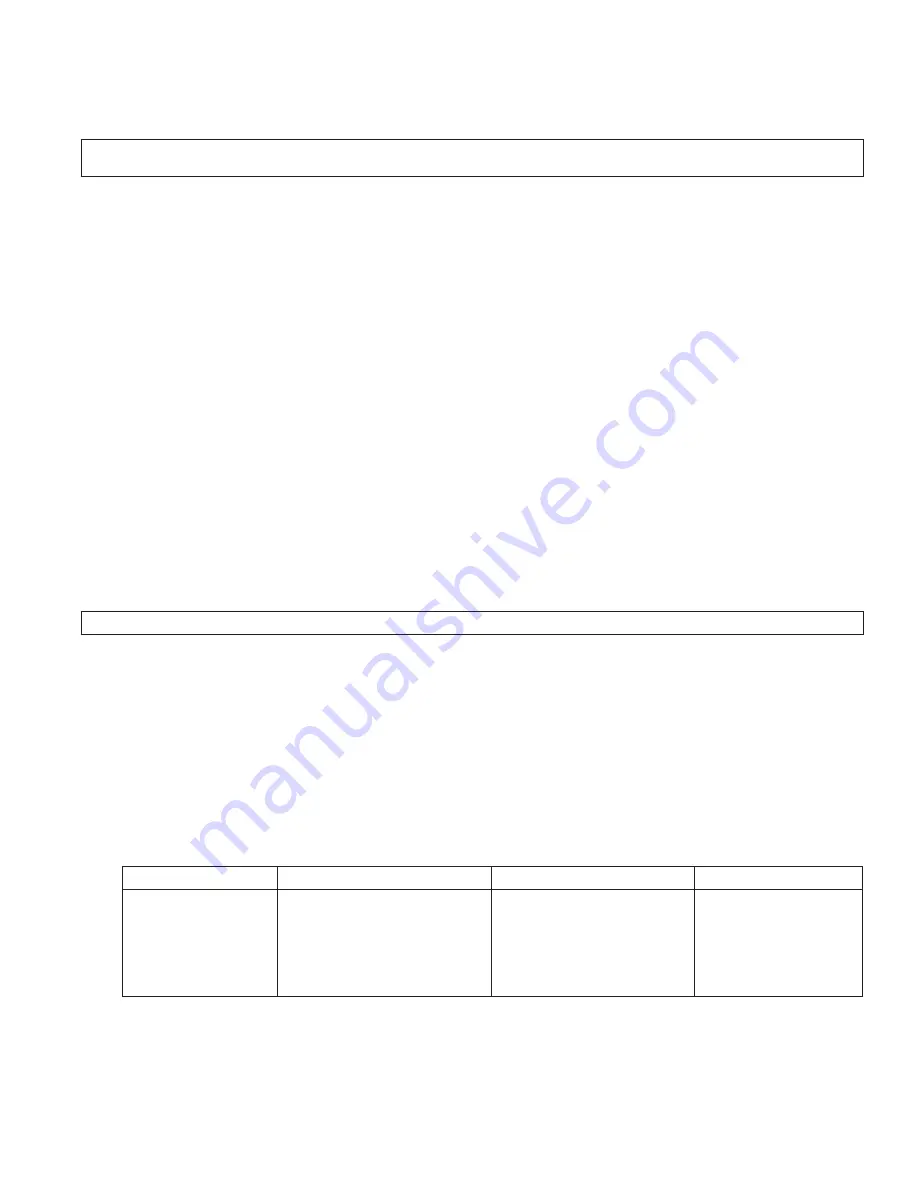
7
4.0 TRAINING
4.1 TRAINING:
The user and the user’s employer must be trained in the correct use and care of this equipment. Both
parties must be aware of the operating characteristics, application limits, and consequences of improper use of this
equipment.
IMPORTANT:
Training must be conducted without exposing the trainee to a fall hazard. Training should be repeated on a
periodic basis.
5.0 INSPECTION
5.1 FREQUENCY:
•
Before Each Use:
inspect according to steps listed in sections 5.2 and 5.3.
•
This Equipment
must be inspected according to steps listed in this section by a competent person, other than the
user, at least annually. Record the results of each inspection in the inspection and maintenance log in section 10.0.
5.2
INSPECTION STEPS:
To ensure safe efficient operation, components of the Lineman’s Belt should be inspected per the
following guidelines:
Step 1.
Inspect Lineman’s Belt hardware (D-Rings, buckles, loop keepers, body pad, etc.). Hardware must not be
damaged, broken, or distorted. Hardware must not have any sharp edges, burrs, cracks, worn parts, or
corrosion. Ensure buckles work properly. Do not use Lineman’s Belts that have missing loop keepers.
Step 2.
Inspect Lineman’s Belt webbing and stitching. Webbing must be free of frayed, cut, or broken fibers. Inspect
webbing for tears, abrasions, mold, burns, and discoloration. Webbing must be free of knots, excessive
soiling, heavy paint build-up, and rust staining. Inspect webbing for chemical or heat damage, indicated by
brown, discolored, or brittle areas on the web surface. Inspect webbing for ultraviolet damage, indicated by
discoloration and splinters or slivers on the web surface. Inspect stitching for broken, pulled, or cut stitches.
Broken stitches may be an indication the Lineman’s Belt has been impact loaded and must be removed from
service. All of the above factors are known to reduce webbing strength. Damaged or questionable Lineman’s
Belts must be removed from service.
Step 3.
Inspect labels. All labels must be present and fully legible. See section 8.0. Replace missing or illegible labels.
Step 4.
Inspect each system component according to manufacturer’s instructions.
Step 5.
Record the inspection results in the inspection and maintenance log in section 9.0 of this manual.
5.3
If inspection reveals an unsafe or defective condition, remove Lineman’s Belt from service and destroy, or contact
DBI-SALA for repair or replacement.
NOTE:
Only DBI-SALA or parties authorized in writing may make repairs to this equipment.
6.0 MAINTENANCE, SERVICING, STORAGE
6.1
Clean the Lineman’s Belt with water and a mild detergent solution. Wipe off hardware with a clean, dry cloth and hang to
air dry. Do not force dry with heat. An excessive build-up of dirt, paint, etc., may prevent the Lineman’s Belt from working
properly, and in severe cases, weaken the webbing. If you have questions about the condition of your Lineman’s Belt,
contact DBI-SALA .
6.2
Additional maintenance and servicing procedures must be completed by DBI-SALA or parties authorized in
writing. Do not
disassemble this equipment. See section 5.1 for inspection frequency.
6.3
Store the Lineman’s Belt in a cool, dry, clean environment, out of direct sunlight.
7.0 SPECIFICATIONS
•
All models meet OSHA requirements
.
Model
Materials
Hardware
Stitching
Regular Belt and Back
Support Belt
D-Ring Component Webbing:
Nylon, 1 3/4 inch, 7,000 lbs
minimum tensile strength; Belt
Webbing: TPU coated Polyester,
1 3/4 inch, 6,000 lbs minimum
tensile strength; Leather: 10 oz.
top grain.
Zinc plated D-Rings, 5,000 lbs
minimum tensile strength; zinc
plated tongue buckle, 4,000
lbs minimum tensile strength;
nickle plated latch hook and
small D-Ring accessory.
Bonded high strength
nylon thread, 5 - 7
stitches per inch.