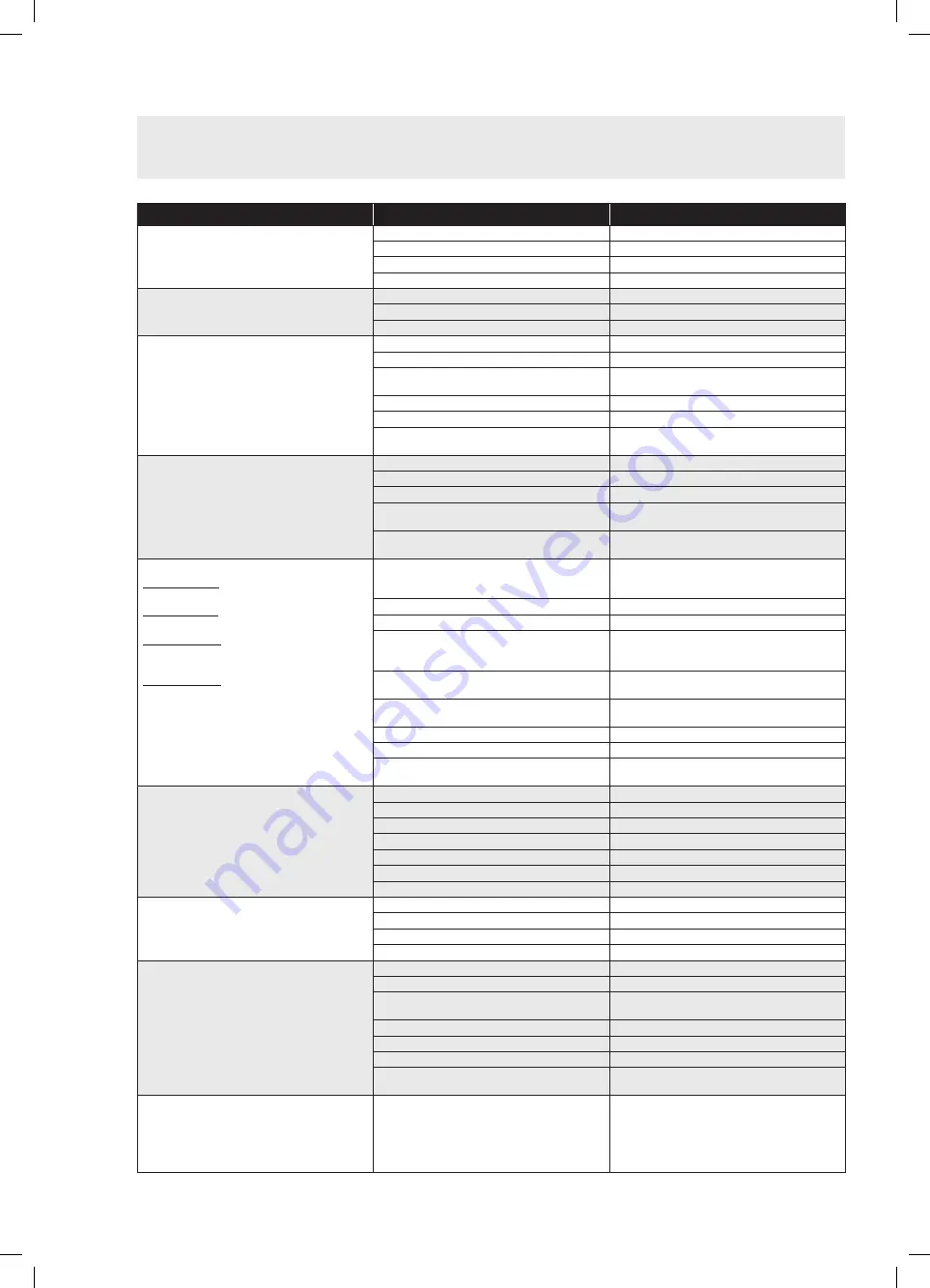
14 | 3MWTS Series Water Softeners – Installation Instructions
3MWTS Series Water Softeners – Installation Instructions | 15
Problem
Possible Cause
Solution
Timer does not display time of day
AC Adapter unplugged
Connect power
No electric power at outlet
Repair outlet or use working outlet
Damaged AC Adapter
Replace AC Adapter
Damaged PC Board
Replace PC Board
Timer does not display correct time of day
Switched outlet
Use uninterrupted outlet
Power outage
Reset time of day
Damaged PC board
Replace PC board
No softening/filtering display when water is
flowing
Bypass valve in bypass position
Put bypass valve in service position
Meter connection disconnected
Connect meter to PC board
Restricted/stalled meter turbine
Remove meter and check for rotation or foreign
material
Damaged meter
Replace meter
Damaged PC board
Replace PC board
Meter wire not securely installed into connector.
Verify meter wire installed securely into three pin
connector labelled METER.
Control Valve regenerates at wrong time of day
Power outages
Reset control valve to correct time of day
Time of day not set correctly
Reset to correct time of day
Time of regeneration incorrect
Reset regeneration time
Control valve set at “ON” (which initiates an
immediate regeneration).
Check program setting and reset to NORMAL
(for a delayed regeneration time.
Control valve set at “ on 0” (delayed
and/or immediate.
Check program setting and reset to NORMAL
(for a delayed regeneration time.
ERROR followed by code number
Error Code 1001:
Unable to recognize start of regeneration
Error Code 1002:
Unexpected stall
Error Code 1003:
Motor ran too long, timed out trying to reach
next cycle position
Error Code 1004:
Motor ran too long, timed out trying to reach
home position
If other Error Codes display, contact 3M
Control valve has just been serviced or unplug
power source jack (black wire) and plug back in
to reset control valve.
Press NEXT and REGEN for 3 seconds
Foreign matter is lodged in control valve
Check piston and spacer stack assembly
High drive forces on piston
Replace piston(s) and spacer stack assembly
Control valve piston not in home position
seconds
Press NEXT and REGEN for 3 seconds or unplug
power source jack (black wire) and plug back in
to reset control valve
Motor not inserted fully to engage pinion, motor
wires broken or disconnected, motor damaged
Check motor and wiring. Replace motor if
necessary
Drive gear label dirty or damaged, missing or
broken gear
Replace or clean drive gear
Drive bracket incorrectly aligned to back plate
Reseat drive bracket properly
PC board is damaged
Replace PC board
PC board incorrectly aligned to drive bracket
Ensure PC board is correctly snapped on to drive
bracket
Control valve stalled in regeneration
Motor not operating
Replace motor
No electric power at outlet
Repair outlet or use working outlet
Damaged AC Adapter
Replace AC Adapter
Damaged PC board
Replace PC board
Broken drive gear or drive cap assembly
Replace drive gear or drive cap assembly
Broken piston retainer
Replace drive cap assembly
Broken main or regenerant piston
Replace main or regenerant piston
Control valve does not regenerate automatically
when “REGEN” button is depressed and held
AC Adapter unplugged
Connect AC Adapter
No electric power at outlet
Repair outlet or use working outlet
Broken drive gear or drive cap assembly
Replace drive gear or drive cap assembly
Damaged PC board
Replace PC board
Control valve does not regenerate automatically
but does when “REGEN” button is depressed
Bypass valve in bypass position
Put bypass valve in normal operating position
Meter connection disconnected
Connect meter to PC board
Restricted/stalled meter turbine
Remove meter and check for rotation or foreign
matter
Damaged meter
Replace meter
Damaged PC board
Replace PC board
Set-up error
Check control valve set-up procedure
Meter wire not security installed into connector.
Verify meter wire installed securely into three pin
connector labelled METER.
Time of day flashes on and off
Power has been out more than eight hours, the
AC Adapter was unplugged and then plugged
back into the wall outlet, the AC Adapter plug
was unplugged and then plugged back into the
board or the NEXT and REGEN buttons were
pressed to reset the valve
Reset the time of day
SECTION 5: CONTROL VALVE TROUBLESHOOTING GUIDE AND SERVICE
INSTRUCTIONS
Summary of Contents for 3MWTS Series
Page 22: ......