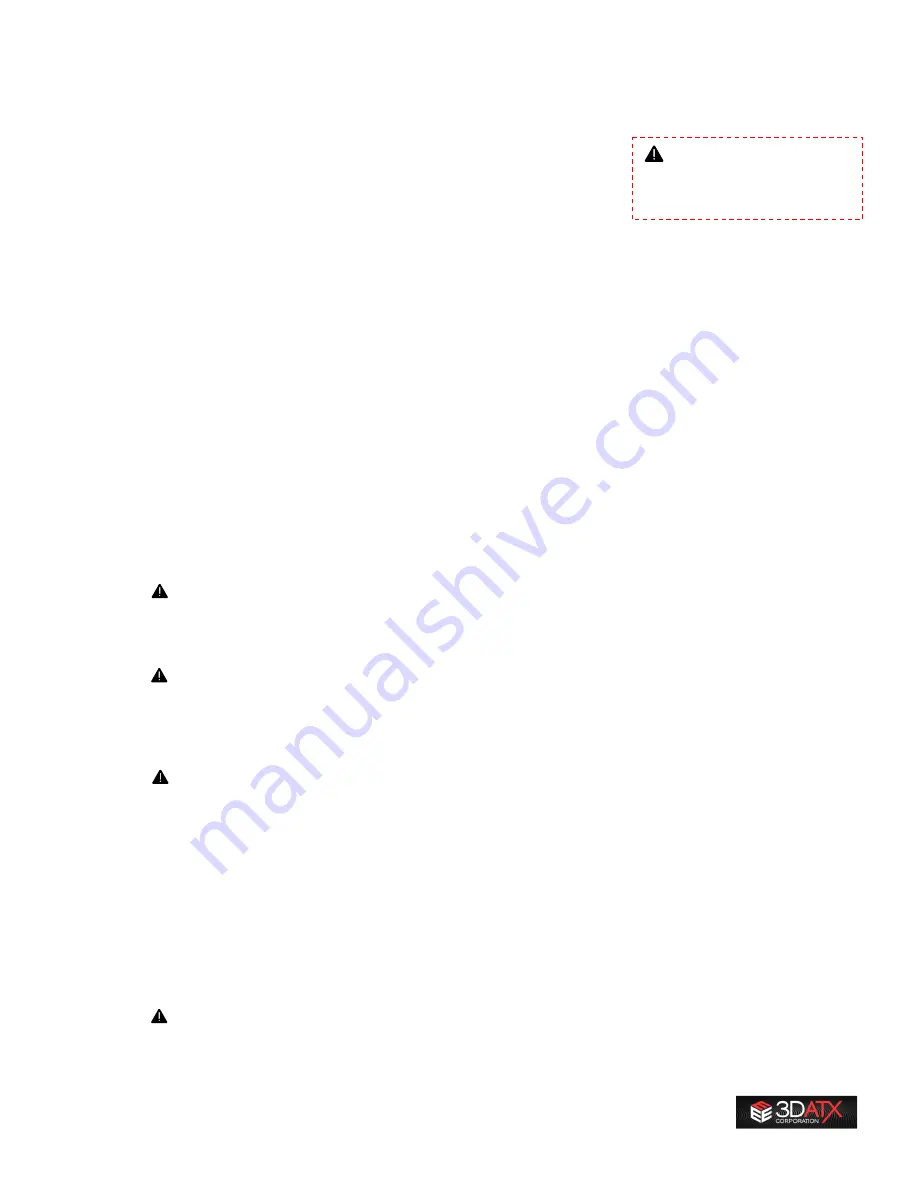
22
5
Test Checklist - parSYNC® and CUBE™
5.1
Day before test
•
Charge batteries in parSYNC® & CUBE™ overnight (5 - 6 hrs. or overnight)
•
Plug both chargers into both heater and pump battery connections
•
Charge tablet
5.2
Test Day
•
Place parSYNC® in warming field bag pack and turn on the warming pad
•
Set temperature using + button to max temp (77
o
C), and allow it to pre-condition the unit for 45 min
•
Keep the tablet on shore power until the start of test
•
Turn on the parSYNC® internal heater power (POWER button is on the temperature controller
of parSYNC®); This is the “Driver” temperature, should initially be set to 10 degrees C above ambient
temperature of testing facility
•
Target for internal sensor temperature is 32 degC – 38 degC, dependent on ambient temperature.
•
Turn on parSYNC® pump and analyzer using Silver ON/OFF Button, run system for 15 min
•
On 3DATX computer tablet, run parSYNC® (executable software) shortcut from desktop
•
Press “Connect” to link to parSYNC® and open a data file
•
This will load the current configuration and the last used calibration, and directs you to the Zero Tab
5.2.1
Zero Sensors
•
Ensure the inlet is sampling ambient air (see Section 4.2.1)
•
Press Zero Start, then allow to complete (~30 seconds) measurement of ambient conditions, ensure
the internal temperature reported on the Temperature tab in the parSYNC software on the tablet
(and not the one on the hardware LCD panel) is stable and operating within 32 degC –
38 degC, dependent on ambient temperature.
o
Zeroing, Calibration and Data acquisition should be made with the set temperature lowered
by 2 degrees so as to keep the heating plate passive during acquisition to avoid sudden shifts
in temperature.
5.2.2
If Calibration is needed, proceed below, (IF NOT, skip this section)
o
During calibration, the hose lengths used should be approximately the same as those used
during acquisition
•
Connect the inlet hose to a “tee barb” hose fitting (to ambient air) and sample audit gas from an
appropriate port, flow rate approximately 2.0 liters/min. (Example: Bar 97 HIGH gas with NO and a
separate NO
2
specialty gas)
o
When connecting reference gases to the parSYNC during calibration, over- or under- pressure
applied through the input hose to the parSYNC must not exceed ±150 mbar in the
measurement cartridges. This is because the membrane in our electrochemical sensors,
particularly the NO sensor, can be damaged by excessive pressure differential, requiring
replacement of at least the GasMod cartridge. Excessive over- or under- pressure is avoided
by connecting a "tee barb" hose fitting between the regulator outlet from the sample audit
gases and the parSYNC inlet hose. Setting the audit gas flowrate to ~ 2.1 liters/min might
exceed the parSYNC sampling flowrate and a small amount of audit gas will leak through the
"tee barb" hose fitting, preventing damage to the cartridges. Note that the correct flowrate
can be determined by gradually increasing flowrate until audit gas is detected flowing from
the "tee barb" hose fitting.
Routine measurement should be made of the parSYNC sampling flowrate (with the standard
lengths of hoses used during acquisition or calibration because flowrate will increase with no
Only use 3DATX supplied
chargers when charging the
system.
Summary of Contents for parSYNC
Page 1: ...User Guide 3DATX Corp parSYNC miniPEMS Updated July 2020 ...
Page 21: ...21 ...
Page 38: ...38 ...