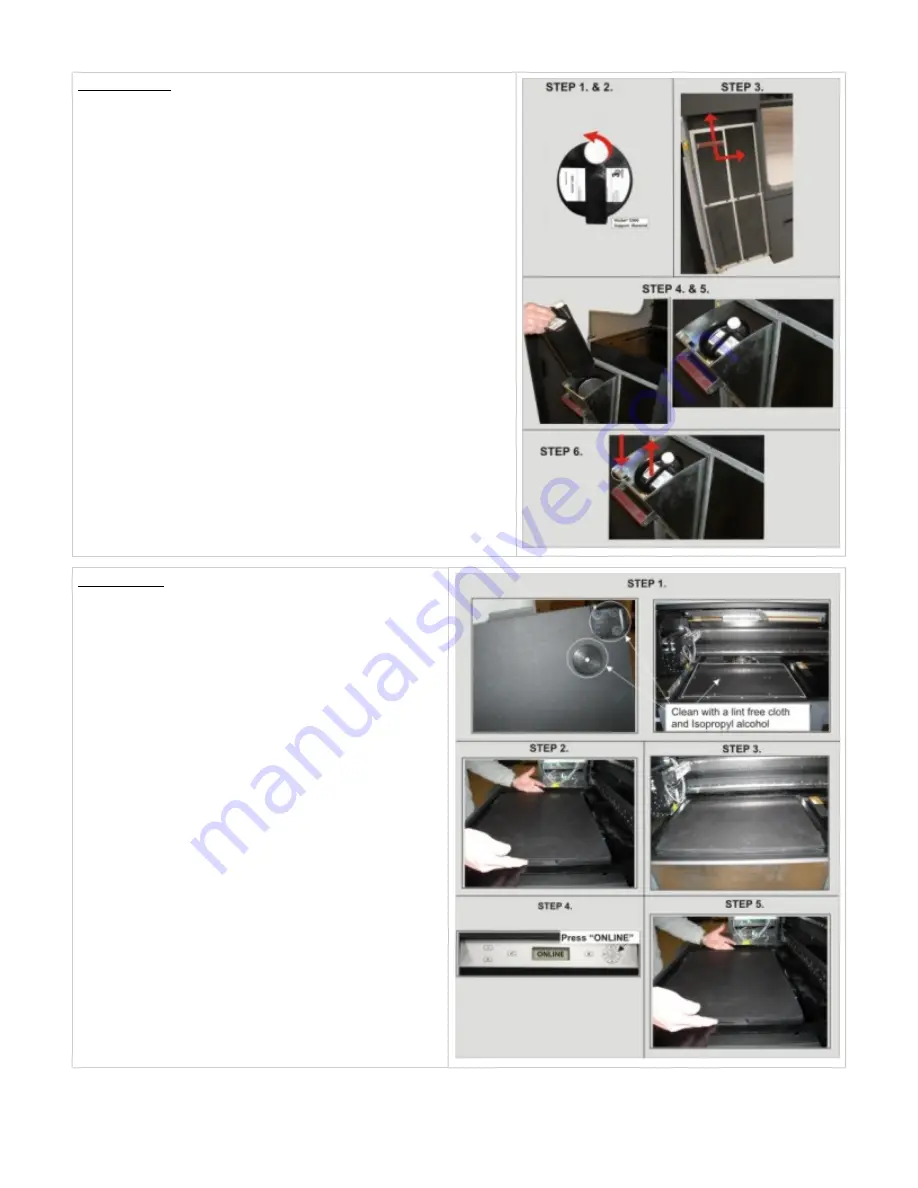
1.
2.
3.
4.
5.
6.
1.
2.
3.
4.
Material Bottles: The printer has up to four material delivery modules for build
materials and up to four material delivery modules for support materials. The
support delivery modules are located on the left side and the build is located on
the right side of the printer. Each delivery module holds one (1) bottle of material.
NOTE: Before handling the build material bottle, read the Material Safety
Data Sheet (MSDS).
Install Material Bottles: Unpack bottles and the MSDS/SDS Sheet from
cartons.
Open left and/or right material delivery doors. Pull material delivery
module (MDM) handle down and out to open.
Install bottle into the MDM; press bottle down until a click sounds.
To ensure that bottle is locked in place, gently pull on bottle. If bottle is
loose, press bottle down to ensure it is secured in MDM.
Loosen bottle cap 1/2 to 3/4 turn counterclockwise to allow the bottle to
vent.
Before removing bottle from the MDM, re-tighten bottle cap to prevent
spillage. To remove bottle, open material delivery module and press
release latch down and lift bottle out of module.
Build Platform:
Ensure that the corner guides on the backside of platform
are clean and free of debris. If debris exists when installing,
the platform guides will not lock into the platform elevator.
NOTE: Clean platform elevator and platform using a lint
free cloth and Isopropyl alcohol. When cleaning
platform, clean the front and back sides.
Lift build chamber door; place platform with corner guides
and pads facing down onto the platform elevator. Seat onto
elevator. The corner guides will affix the platform to the
elevator and if properly installed, platform will not move. It
should sit squarely on the elevator and be firmly located by
the corner guides. Use caution not to drop the platform or
hit the printhead.
Close build chamber door and press ONLINE.
To remove platform, lift from the sides; pull up and out from
the platform elevator.
The ProJet™ Production Printing System can now be used to produce prints.
Summary of Contents for ProJet 5000
Page 5: ......