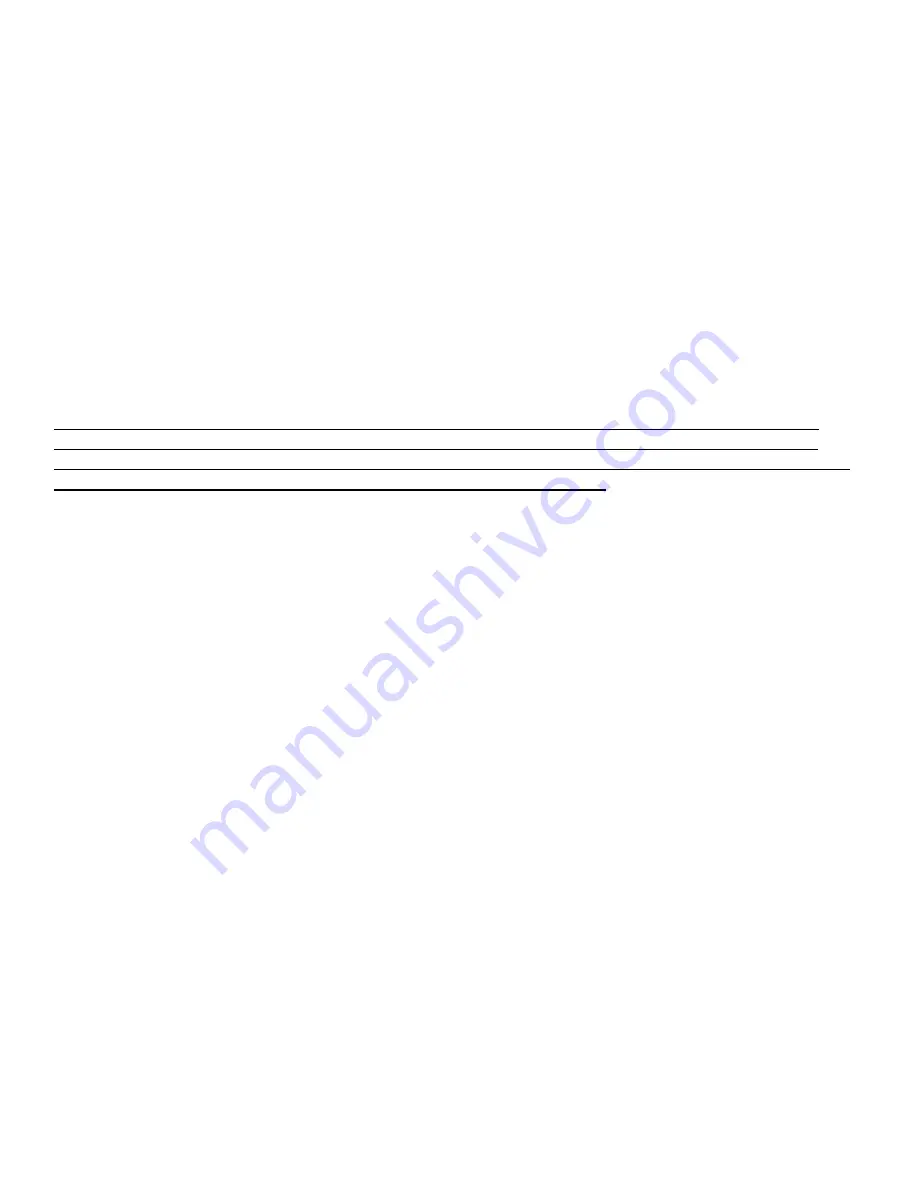
3D Platform
WorkSeries 200, 300 & 400 Manual
Revision: C
Date: December 28, 2017
3dplatform.com
• 3DP
-DOC-005 (12-2017)
29
Appendix 1: Warranty Information
3D Platform offers a ninety (90) day limited warranty commencing on date of shipment for each machine bought
through 3D Platform or an authorized 3D Platform reseller. An extended one (1) or two (2) year warranty is available for
purchase. 3D Platform warrants that the 200, 300 and 400 WorkSeries shall conform to the description stated on the
sale order and shall be free from defects in material or workmanship during the applicable warranty period when used
under the normal conditions described in 3D Platform
’s documentation found
at www.3dplatform.com. 3D Platform will
promptly repair or replace the 200, 300 and 400 WorkSeries, if required, to make it free of defects during the warranty
period. Only the items explic
itly stated in the “Items Covered Under Warranty” section of the warranty are covered. All
other items and conditions are excluded, including but not limited to (i) normal consumable or expendable parts, (ii)
repairs required during the warranty period because of abnormal use or conditions such as riots, floods, misuse, neglect,
or improper service by anyone except 3D Platform or its authorized 3D Platform service provider, and (iii) repairs
required during the warranty period because of the use of modifications made by Customer or anyone else to the 200,
300 and 400 WorkSeries. Any modification to the 200, 300 and 400 WorkSeries will void the warranty. For additional
information and to view the full warranty, please visit www.3dplatform.com.
THIS WARRANTY IS THE ONLY WARRANTY PROVIDED FOR THE PURCHASE OF A 200, 300 and 400 WORKSERIES. 3D
PLATFORM DISCLAIMS ALL OTHER WARRANTIES, EXPRESS OR IMPLIED, ORAL OR WRITTEN, INCLUDING, WITHOUT
LIMITATION, THE IMPLIED WARRANTIES OF MERCHANTABILITY AND FITNESS FOR A PARTICULAR PURPOSE. THERE ARE
NO WARRANTIES THAT EXTEND BEYOND THE DESCRIPTION ON THE FACE HEREOF.